Simufact用于锻造轮毂工艺研究
更新于2022年12月19日 09:50 浏览:2164
铝合金旋压轮毂具有重量轻
,强度高
,寿命长
,表面光洁
,机械加工余量少等优点
,而旋压工艺过程复杂
,影响因素多
,造成实际旋压加工中工艺参数和工装的选择和调试较为困难。
Simufact.forming软件可以提前判断旋压工艺的可行性及合理性(旋压件的应力应变
,厚度尺寸变化
,旋压力变化情况)
,为旋压产品的研制提供重要参考。
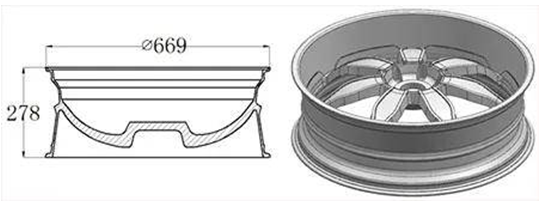
图1 铝合金轮毂结构
铝合金轮毂结构如图
1所示,材料为
6061铝合金,直径为
ϕ
669mm,高度为
278mm。由于铝合金轮毂尺寸较大,锻造成形过程复杂,采用一次性锻造成形通常需要较大的成形力且材料填充不饱满,需要增加一道预锻工序。预锻成形可以有效降低金属回流和防止起皱,保证零件的成形质量,另外增加预锻工序可以减少一次性变形程度,有利于降低成形载荷,使金属填充饱满,并且可以减少模具零件的损伤,延长模具使用寿命。将直径为
ϕ669mm、高度为
52mm的圆形坯料加热以提高材料塑性,再采用反挤压的方式将坯料挤成杯状预锻件,再将杯状预锻件锻成碗状终锻件,然后将该碗形终锻件作为旋压坯料与加热坯料,旋压成旋压件,最后将旋压件机加工、涂装成成品,具体过程如图
2所示。
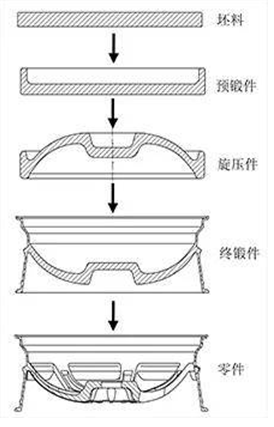
图2 轮毂法兰盘锻造工艺
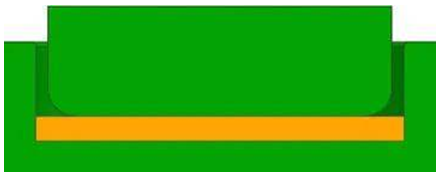
图3 预锻模型
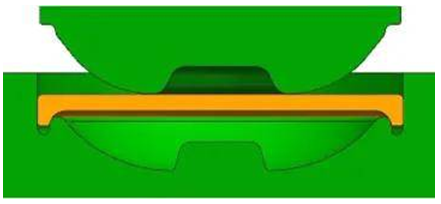
图4 终锻模型
simufact软件中进行处理,采用
Ringmesh模式对坯料进行网格划分。零件材料为
6061铝合金,模具材料为
H13钢,预锻、终锻时坯料温度设置为
400℃,模具温度设置为
350℃;摩擦类型采用剪切摩擦,摩擦因数取
0.3。首先对预锻过程进行模拟,再将预锻件及相关信息导入终锻过程,作为终锻过程坯料,进行终锻模拟,结果如图
5所示。
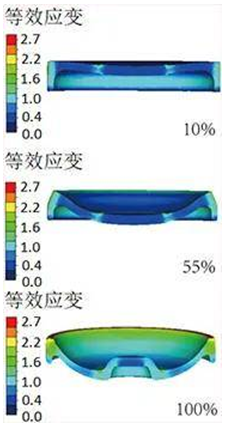
图5 终锻过程等效应变分布
工艺参数优化
采用
Simufact,可以进行工艺参数优化研究,比如,模具温度,胚料温度,锻成型时上模下压速度,摩擦系数等。
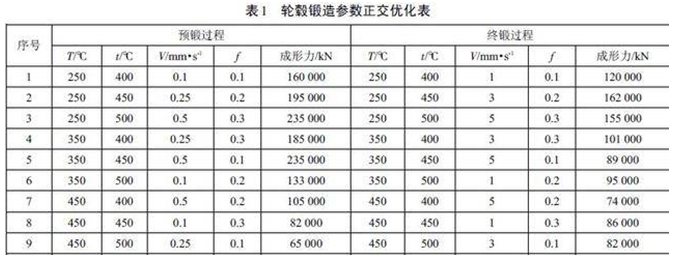
经分析得出,预锻过程中影响程度主次关系为模具温度
T>上模下压速度
V>坯料温度
t>摩擦因数
f。终锻过程中,影响程度最大的为模具温度
T,上模下压速度
V、摩擦因数
f、坯料温度
t影响程度相近。预锻坯料温度最佳为
500℃,但
6061铝合金超过
550℃会有过烧的危险,因此通过对坯料温度
K值的比较分析,坯料温度选择
400℃;终锻时,最优摩擦因数为
0.1,但是锻压过程始终在较高的温度下,材料软化,摩擦因数会增大,最后选择的摩擦因数为
0.2。综上所述,根据平均值
K,结合实际预锻工艺参数:模具温度
450℃、坯料温度
400℃、下压速度
0.1mm/s、摩擦因数
0.2;终锻工艺参数:模具温度
450℃、坯料温度
400℃、下压速度
1mm/s、摩擦因数
0.2,对上述
2组参数进行模拟,结果显示,终锻时最大成形力为
66000kN,符合生产要求,相对于优化前的
80000kN,下降了
20%。
文章来源:SH赫普
技术邻APP
工程师必备