新能源汽车、机器人和高精度数控机床等国家重点支持领域的发展对电机的效率、功率密度、响应速度和振动噪声等性能指标提出了更高的要求,促使电机向高精度、高功率密度、小型化、轻量化和机电一体化等方向发展,带来了电机内部发热量急剧增加、有效散热空间严重不足等问题,因此散热问题成为电机系统进一步向高功率密度方向发展的瓶颈。电机内部温升过高不仅会缩短电机内部绝缘材料的寿命,而且会降低电机的运行效率,使得发热量增加,造成电机温度进一步上升,形成恶性循环,严重影响电机寿命和电机运行的安全性。据统计,30%~40%的永磁电机失效是由电机温升过高引起的,因此,采用高效的散热系统抑制电机温升是电机向高效率、高稳定性和高可靠性方向发展的关键。
风冷、液冷和蒸发冷却散热系统是三种常用的电机散热系统。风冷散热系统凭借成本低、可靠性高和安装方便等优势在小功率电机散热领域得到了广泛应用。相较于风冷散热系统,液冷散热系统具有极高的散热效率,其散热效率可以达到前者的50倍,适用于电机发热量大、热流密度高的散热场合。然而液冷散热系统需要额外的循环液路与密封系统,增加了电机系统的成本和复杂性。目前,由我国自主研发的蒸发冷却散热技术在兆瓦级大容量发电机组的散热系统中得到了广泛应用,其主要原理是利用工质的气液相变循环实现对电机的高效冷却。蒸发冷却技术可以有效降低电机运行温升。
高效化是电机散热系统发展的重要方向,优化电机散热系统结构参数是提高电机冷却效率的常用手段。近年来,通过在电机关键发热部件与冷却壳体之间构建额外热路来提高电机散热效率的额外热路增强型电机散热方案得到了研究与应用。利用导热树脂、导热胶和导热陶瓷等导热绝缘材料在电机端部绕组与机壳之间构建额外热路是该散热方案的常用形式。此外,采用铝片、铜棒和热管等高热导率传热器件充当额外热路的增强型电机散热方案也逐渐得到了研究和应用。额外热路增强型电机散热方案是解决电机关键发热部件散热难题的有效手段,同时也提供了提高电机散热系统效率的新思路。
本文针对电机散热系统向高效化、高可靠性方向发展的趋势,介绍了当前电机散热系统的类型及其使用范围,分析了各类电机散热系统的优势及不足,总结了目前国内外在提高电机散热系统效率方面的研究进展,讨论了其在实际应用中所存在的问题。结合额外热路增强型电机散热方案和相变散热技术提出了以相变传热器件来提高电机散热效率的新方案,最后对电机散热系统的发展趋势进行了科学预测与展望。
电机作为多物理场、强耦合的能量转换系统,其能量转换效率并不是百分之百,在将电能转换为机械能的过程中会损失一部分能量,这些损失的能量绝大部分转换为热能引起电机发热。电机内部的损耗主要由绕组线圈的电阻、磁性材料的磁阻和电机各部件间的机械摩擦造成,主要包含绕组铜耗、定转子铁耗和机械损耗三部分。电机绕组、定子和机壳等关键部件的接触面之间存在绝缘漆、绝缘纸和空气等热导率极低的材料,增加了电机各部件间的接触热阻,极大地降低了电机关键部件的散热效率。永磁同步电机内部热路如图1所示,电机内部的关键发热部件与机壳之间的传热路径长、接触热阻大,电机工作过程中产生的热量不能及时传递至外部,引起电机内部温度升高。电机温升过高将严重威胁电机绝缘寿命、运行效率和可靠性。
图1 永磁同步电机内部热路示意图
Fig.1 Schematic diagram of internal thermal circuit
of permanent magnet synchronous motor
电机内部的绝缘漆和绝缘纸等绝缘材料的寿命与电机温度呈现指数变化规律:
式中,D为绝缘材料的寿命;A0为环境温度为0 ℃时绝缘材料的寿命;T为电机的实际工作温度;a为电机绝缘等级。
从式(1)中可以看出,电机的绝缘寿命会随着电机实际工作温度的上升而急剧下降。同时,电机温度升高将引起电机绕组阻值增加、电机内部磁性材料去磁等问题,增加电机损耗,降低电机工作效率,进一步引起电机发热量增加。电机绕组阻值随温度变化的规律如下:
式中,R为温度T时绕组的电阻;R0为温度T0时绕组的电阻;α0为电阻温度系数;T0为起始温度。
由式(2)可以看出,绕组的温度升高将引起绕组阻值变大,进一步增大电机铜耗。同时,定子铁芯、永磁体等磁性材料的性能也随着电机温度的上升而下降,增大电机的铁耗,降低电机的工作效率。此外,组成电机的各种金属材料的硬度、强度以及其他力学性能也会受到电机温升的影响而逐渐下降,威胁电机运行的安全。当电机工作在大转矩、高转速等极限工况时,电机的发热量将急剧增加,如果不能将电机内部的热量快速传递至外部,甚至会造成电机内部磁性材料永久性退磁、烧机等现象。
采用高效可靠的散热系统将电机运行过程中产生的热量快速传递至外部,避免热量在电机关键部件的积聚,保证电机始终工作在合适的温度,对电机的寿命、效率和运行安全性具有重要意义。
电机散热系统分类及相应电机照片如图2所示,电机散热系统主要包括风冷、液冷、蒸发冷却和额外热路增强型散热系统四大类,应用最广泛的是低成本、适用于小功率电机的风冷散热系统和高效率、适用于大功率电机的液冷散热系统。利用液体沸腾气化进行高效散热的蒸发冷却技术主要应用于兆瓦级发电机组的散热系统。近年来,利用导热绝缘材料或相变传热元件在电机关键发热部件与冷却壳体之间构建额外热路以强化电机散热的额外热路增强型电机散热方案逐渐得到了研究和应用。从技术角度看,任何一台电机都可以随意选取散热系统形式,关键是根据电机的工作环境、发热功率、可靠性、维护方便性和成本等因素选取合适的散热系统。甚至可以将风冷散热系统和水冷散热系统结合应用,王金松等将封闭式内通风散热系统和冷却水套结合应用于电机散热系统,电机内部产生的热量在轴端风扇的作用下进入通风管道,并与循环水套内的冷却水进行热交换,实现了良好的散热效果。
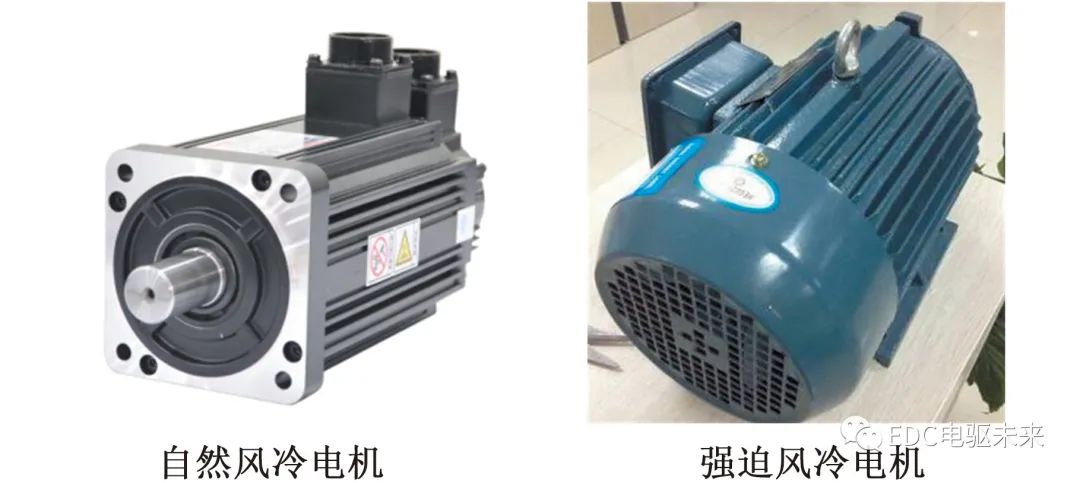
(a)风冷散热系统
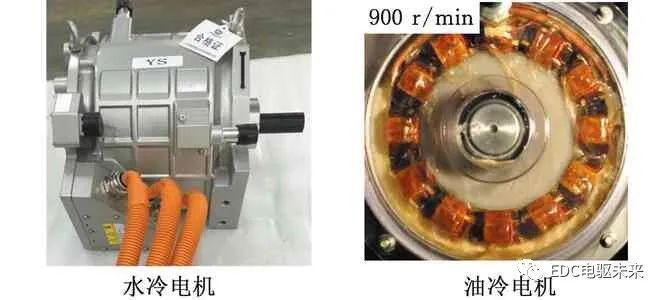
(b)液冷散热系统
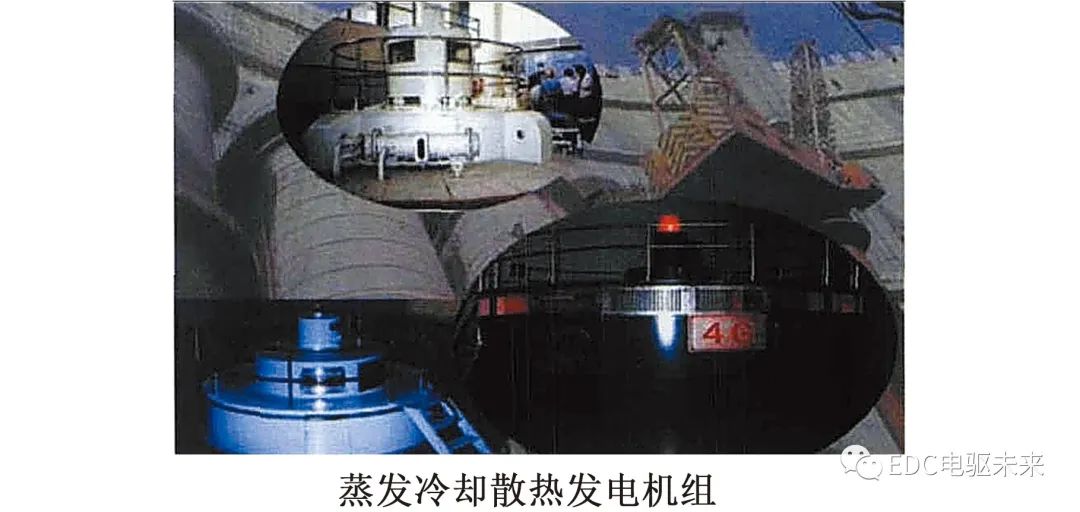
(c)蒸发冷却散热系统
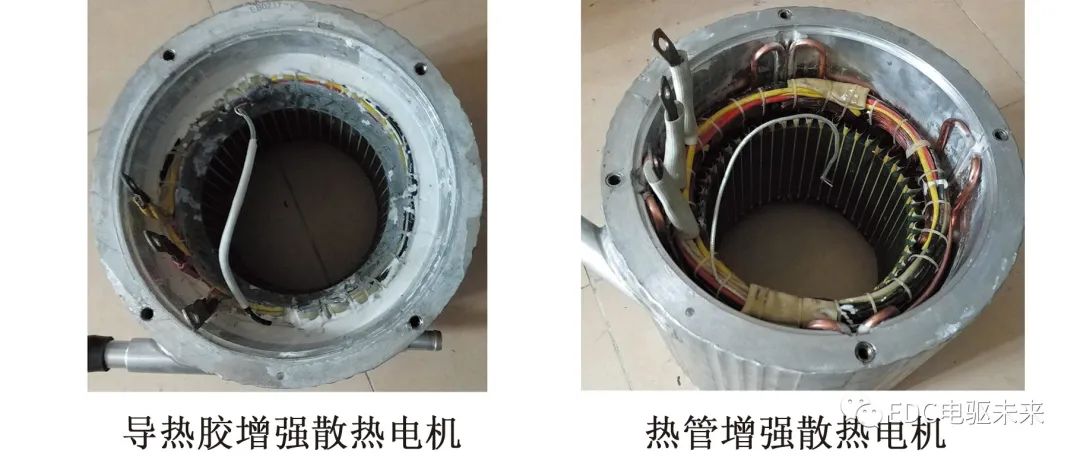
(d)额外热路增强型散热系统
图2 电机散热系统分类
Fig.2 Classification of motor cooling system
风冷散热系统通常在机壳表面设计翅片以增加换热面积、提高散热效率,具有制造工艺简单、成本低廉和可靠性高等优势,在小功率密度电机散热领域得到了广泛应用。风冷散热系统可以根据是否采用额外的增强空气流动的装置分为自然风冷和强迫风冷。自然风冷不需要额外的动力装置,仅仅通过机壳与周围空气的自然对流进行热交换。强迫风冷通常利用风扇系统加强电机与外部空气的热交换,额外的风扇系统提高了电机的散热效率,但也在一定程度上增加了电机系统的电力消耗和噪声。风冷散热系统的分类依据及分类情况如图3所示。
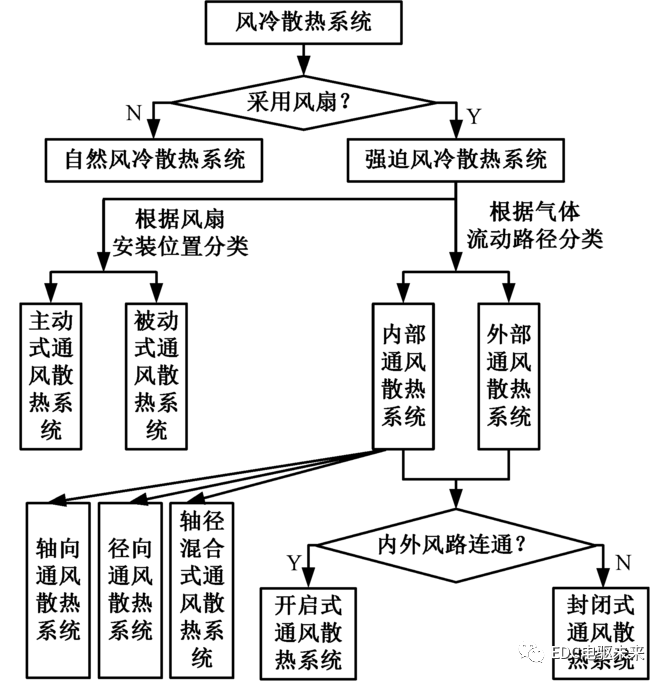
图3 风冷散热系统分类
Fig.3 Classification of air cooling systems
根据气流的流动路径可以将强迫风冷散热系统分为外部通风和内部通风两大类:外部通风散热系统通过风扇驱动冷却气流在机壳外表面流动,达到冷却电机的目的;内部通风散热系统利用风扇驱动气流从入风口进入,沿电机内部的气流通道对电机各部件进行冷却后再从出风口流出。根据冷却气流在电机内部流动路径可以将其分为轴向式、径向式和径轴混合通风三种形式。根据电机内部风路和外部风路是否连通,可以将强迫风冷散热系统分为开启式和封闭式系统。开启式强迫风冷散热系统的内外风路连通,外部空气可以进入电机内部直接进行热交换,具有较高的散热效率;但是空气中的灰尘容易进入电机,因此需要对电机进行定期清理。封闭式强迫风冷散热系统可以有效避免灰尘进入电机,依靠电机内部的同轴风扇驱动气流将热量传递至机壳,然后与外部环境进行热交换。此外,也可以根据风扇的安装位置分为被动式强迫风冷和主动式强迫风冷。被动式强迫风冷是将叶片安装在电机的转子或转轴上,叶片跟随电机转子同步旋转,产生气流以强化电机散热。被动式强迫风冷散热系统的冷却流量与电机转速成正相关关系,在低转速、高负载工况下易出现冷却风量不足的问题。主动式强迫风冷是在电机的外部设置独立的风扇系统对电机进行散热,冷却气流的流量和流速与电机工作状况无关,可以始终保持较高的冷却效率。
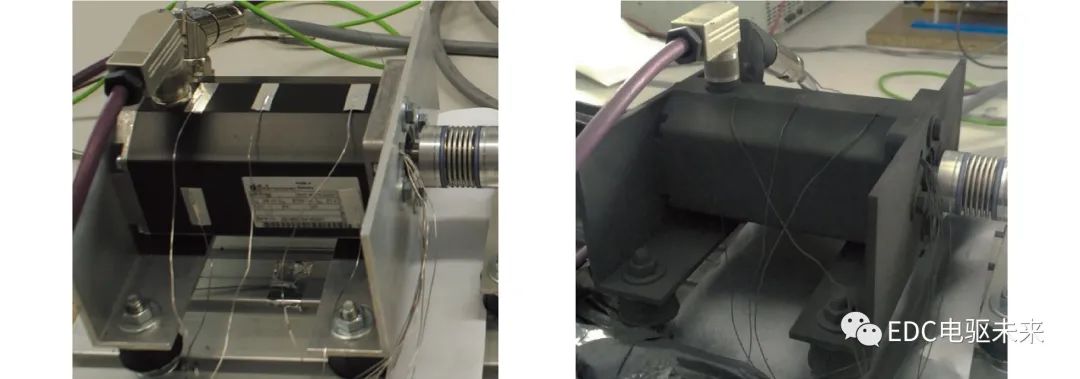
(a)原始电机(b)机壳表面涂覆
高辐射率石墨
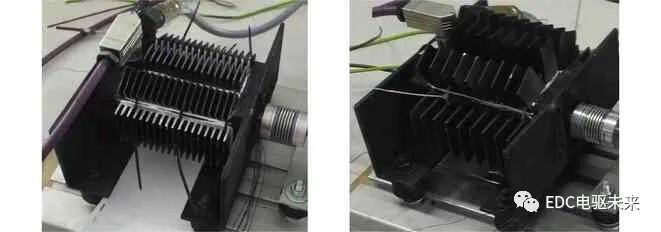
(c)机壳表面采用(d)机壳表面采用
小尺寸翅片大尺寸翅片
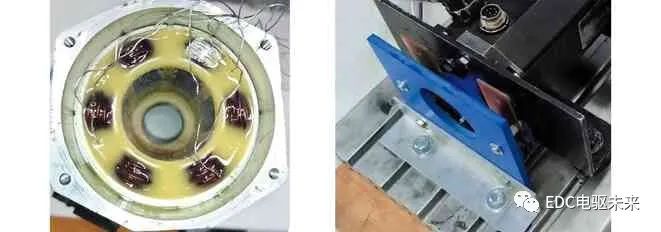
(e)端部绕组与机壳之间灌注导热胶
图4 自然风冷电机照片
Fig.4 Photos of natural air cooling motors
2.1.1 自然风冷散热系统
自然风冷散热系统结构简单、可靠性高,适用于电机发热量较小、电机可靠性要求较高、电机工作环境通风良好的散热场合。机壳表面的散热筋、散热翅片结构可以有效提高自然风冷散热系统的效率。JANG等采用有限元仿真法对比分析了机壳表面翅片结构对自然风冷散热系统冷却效率的影响,仿真结果表明在机壳表面添加翅片结构可使电机定子和转子的散热效率分别提高26.1%和16.4%。MELKA等研究了额定功率为430W的永磁无刷直流电机的自然风冷散热系统,采用在机壳表面涂覆高辐射率材料、机壳表面设置不同规格的翅片和填充导热材料三种方法来提高散热系统的效率,机壳样品如图4所示,测试结果表明,相对于原始电机,四种散热方案可以分别降低绕组温度约4 ℃、9 ℃、16 ℃和18 ℃。当同时采用大尺寸散热翅片和填充导热材料时,绕组稳定温度可以降低约30 ℃。MELKA等建立了永磁无刷直流电机的CFD模型用以研究电机关键发热部件的散热情况及气体在电机周围的流动情况,并测试了电机在多个工况下的温升性能,电机内部温度的仿真结果与测试结果之间的误差不超过9 ℃,电机外部温度仿真结果的误差为2 ℃。CHIU等采用FLUENT软件仿真了翅片结构参数对开关磁阻电机温升性能的影响,并设置机壳表面自然对流传热系数为10 W/(m2·K)。仿真结果表明,当翅片面积相同时,电机绕组最高温度随着翅片数量的增加而升高;当翅片高度相同时,电机温度随翅片数量的增加而降低,电机温度分布云图见图5。
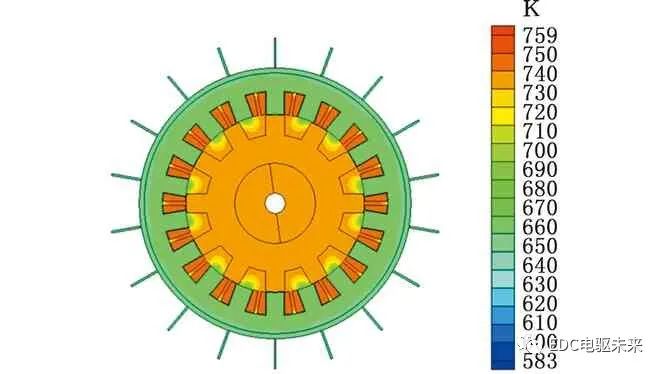
(a)18个翅片
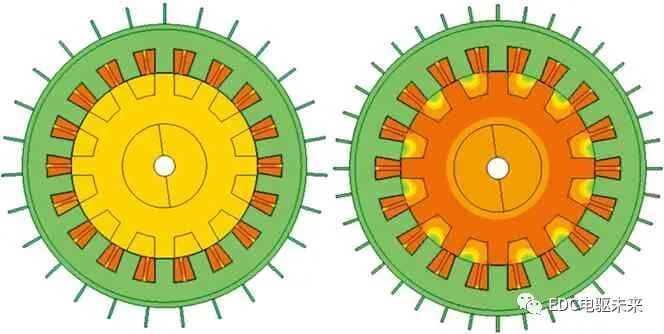
(b)27个翅片 (c)36个翅片
图5 采用不同翅片结构的电机温度分布云图
Fig.5 The temperature distribution of the motors with
different fin structures
2.1.2 强迫风冷散热系统
自然风冷散热系统的效率与机壳表面翅片面积、翅片高度和机壳表面的辐射率正相关,这些因素对强迫风冷散热系统的效率也同样具有增强作用。利用有限元仿真软件,GALLONI等分析了叶片形状、数量和长宽比等参数对电机散热效率的影响,并根据分析结果开发了能够用于电机强迫风冷散热系统耦合热分析的数学模型。
NAKAHAMA等提出了适用于开启式风冷散热系统车用电机的定子铁心内部及外部双冷却通路的强化散热方案。KIM等建立了开启式风冷散热感应电机的热网络模型,该模型计算得到的定子、绕组温度误差不超过2 ℃。GRAB OWSKI等对额定功率为7.5 kW的封闭式外通风散热电机的温升性能进行了有限元仿真,仿真结果与测试结果之间的误差不超过10%。NODA等设计了一款采用开启式强迫风冷散热系统的车用电机,如图6所示,由于外部空气直接进入电机内部进行冷却,因此每三年需要拆卸电机进行清理,并且高转速工况下的电机噪声较大。开启式散热系统的散热效率较封闭式散热系统高,但是噪声较大、需要定期清理的不足限制了开启式风冷散热系统电机的进一步发展。封闭式风冷散热系统具有相互独立的内部风道与外部风道,可以有效阻止污染物进入电机内部,逐渐取代开启式散热系统得到了应用与发展。
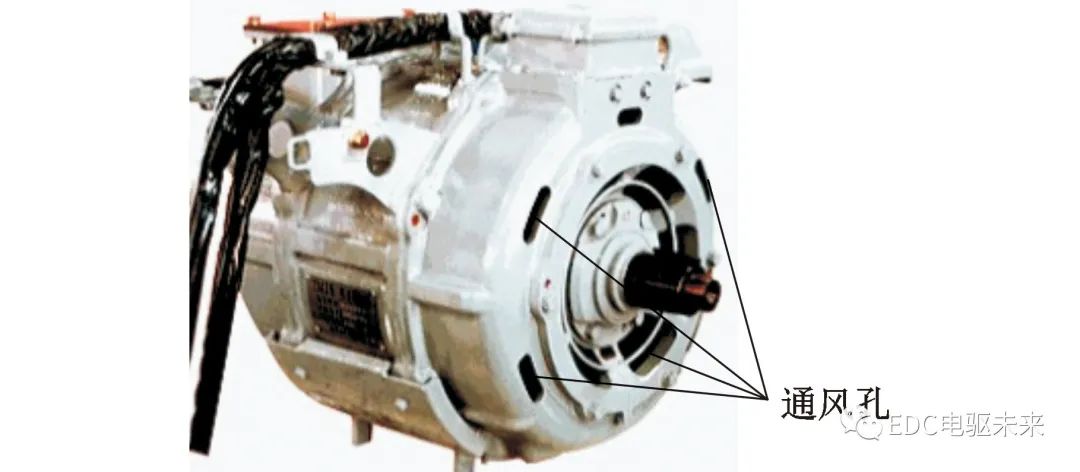
图6 具有开启式风冷散热系统的车用电机
Fig.6 Motor with an open air cooling system
内部通风散热系统的冷却气流可以与电机内部的发热部件直接接触,其散热效率高于外部通风散热系统。YOON等对比了内通风散热系统和外通风散热系统对电机绕组温升的影响,实验结果表明内通风散热系统可以有效降低电机绕组稳定温度约10 ℃,在电机满载工况下提高电机效率约0.25%,在电机1.25倍过载工况下提高电机效率约0.5%。图7为采用封闭式内部通风散热系统电机的截面图,如图中箭头所示,电机轴端的扇叶驱动气流在电机定、转子间隙及转子通风道中流动,并通过机壳表面的散热翅片与外界进行热交换,冷却后的气流进入电机内部进行下一个循环。
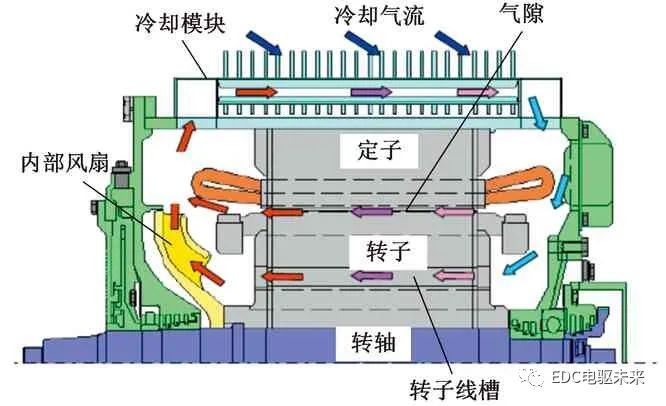
图7 采用封闭式内部通风散热系统的电机截面图
Fig.7 Sectional view of the motor with closed internal
ventilation cooling system
风冷散热系统也可以满足大功率电机的散热需求,但是往往需要采用多个风扇并复合大体积的翅片式散热器。WEN等建立了额定功率为800 kW的高压异步电机的外部扇区和冷却区CFD模型,研究了外部风机的流程特性和效率曲线,确定了外部风扇的最佳运行点,在此基础上探讨了冷却器结构对流体流动的影响,并通过优化冷却器结构提高了冷却效率。CHANG等建立了适用于额定功率2350 kW的电机强迫风冷散热系统,该散热系统主要包括一个离心风扇、两个轴端风扇和一个具有637支冷却管的热交换器,通过调整散热系统的结构参数、设计具有导向叶片的高效热交换器和优化两个轴端风扇距离等方法来提高该风冷散热系统的效率,成功降低电机温升约6 ℃。XU等研究了额定功率为2500 kW的高压电机的强制风冷散热系统,该散热系统同时采用外部通风和内部通风,研究了扇叶偏转角和出口角对风扇系统散热效率的影响,通过优化扇叶倾角提高外部风扇冷却效率约1.16%,增大出口流量0.08 m3/s。
空气是风冷散热系统最常用的冷却介质,此外,还可以采用氢气和氦气对电机进行冷却。XU等采用氦气对高温气冷堆的鼓风机驱动电机进行冷却,电机额定功率为4500 kW,仿真结果表明氦气的初始温度显著影响电机的温升。氦气和氢气的热导率是空气的6~7倍,因此相同的气体温度和流速情况下,氦气、氢气冷却的散热效率可以达到空气的1.3~1.5倍。同时,氢气和氦气的密度只有空气的1/14~1/7,因此采用氢气、氦气代替空气可以显著减小冷却系统的通风损耗和风摩损耗。然而,氢气和氦气高昂的价格、复杂的储存供应系统限制了氢气、氦气冷却系统的大规模应用。此外,氢气冷却系统需要氢气纯度不小于96%和安全可靠的密封防爆系统,这进一步限制了氢气冷却系统的应用。因此,氢气、氦气冷却系统多应用于大功率发电机、高温反应堆等特殊场合。
自然风冷散热系统的传热系数只有2~25 W/(m2·K),而强制风冷散热系统的传热系数可达20~300 W/(m2·K)。风扇系统虽然在一定程度上增加了系统的噪声和能耗,但是可以显著提高电机的冷却效率,提高磁性材料的利用率。因此,相对于采用自然风冷散热系统的电机,采用强制风冷散热系统的电机往往具有较小的质量和较高的功率密度。
内部通风散热系统的冷却气流与电机发热部件直接接触,其冷却效率显著高于外部通风散热系统。同时,封闭式散热系统可以有效避免污染物进入电机内部,降低电机维护成本。封闭式内通风散热系统兼具散热效率高和维护成本低的优势,逐渐取代开启式散热系统而得到了广泛的应用。值得注意的是,采用自然风冷散热系统和封闭式外通风散热系统的电机内部不存在高速流动的冷却气流,电机内部热交换效率极低,因此在电机内部关键发热部件与机壳之间构建高效热路是提高电机散热效率的关键。近年来,逐渐出现了在电机机壳与端部绕组之间灌封导热材料的方案。导热材料的热导率是空气热导率的几十倍至几千倍,可以显著改善端部绕组的散热环境,抑制绕组温升,提高电机散热效率和运行稳定性。
风冷散热系统具有结构简单、成本低廉、安装维护方便和可靠性高等优势,然而较低的散热效率决定了风冷散热系统只能应用于功率密度偏低的电机。风冷散热系统的冷却效率主要由翅片结构参数、气体通道分布位置、气体流量、冷却介质和机壳表面热辐射率等因素决定。氢气、氦气取代空气作为风冷散热系统的冷却介质,可以有效提高散热效率、降低通风损耗,然而氢气易燃易爆、氦气价格昂贵的不足限制了其在风冷散热系统中的大规模应用,因此,空气依然是当前风冷散热系统最常用的冷却介质。
液冷散热系统是在电机机壳内部或电机内部设置密封的循环流道,并采用循环装置驱动冷却介质在流道内循环流动进行换热的电机冷却系统。常用冷却介质的物理特性如表1所示,根据冷却介质可以将液冷散热系统分为水冷散热系统和油冷散热系统两类。水冷散热系统主要是在机壳内部设置循环流道,流道结构主要有圆周型、螺旋型和轴向型三种,还有少部分的复合型流道结构,其结构如图8所示。圆周型冷却流道的散热能力较强,螺旋型冷却流道的压力损耗较小,而轴向型冷却流道的轴向温度梯度小,适合轴向长度较长的电机。此外,也可以在定子铁芯上设计循环水路,对定子进行高效冷却,在铁芯轭部集成冷却水管的散热结构如图9所示。水介质具有无污染、成本低、质量热容和热导率较高等优势,因此得到了广泛的应用。为了克服水介质凝固点较高、沸点较低的不足,在实际使用中往往采用水-乙二醇混合溶液以降低凝固点,提高水冷散热系统的环境适应性。此外,水冷散热系统在长期循环过程中容易产生水垢并腐蚀机壳,因此在实际应用中还需要添加抗腐蚀和抗泡沫等添加剂。
表1 冷却介质常温常压下的物理特性
Tab.1 Properties of cooling medium under normal temperature and pressure
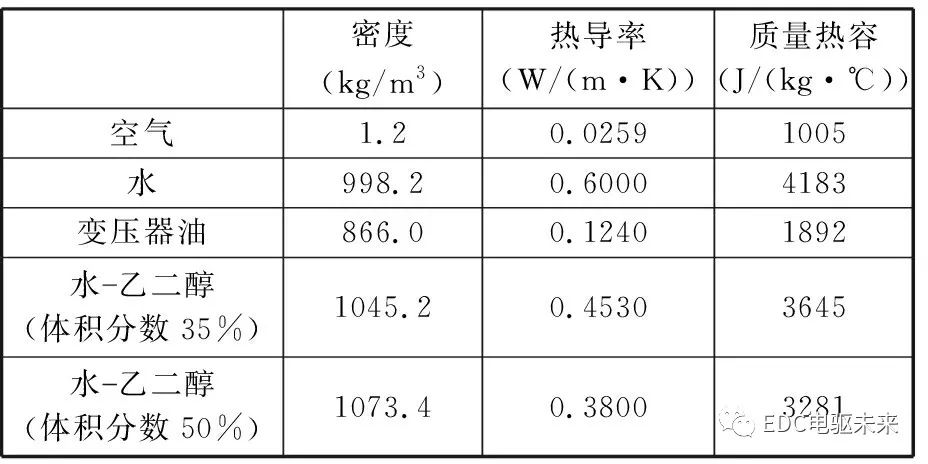
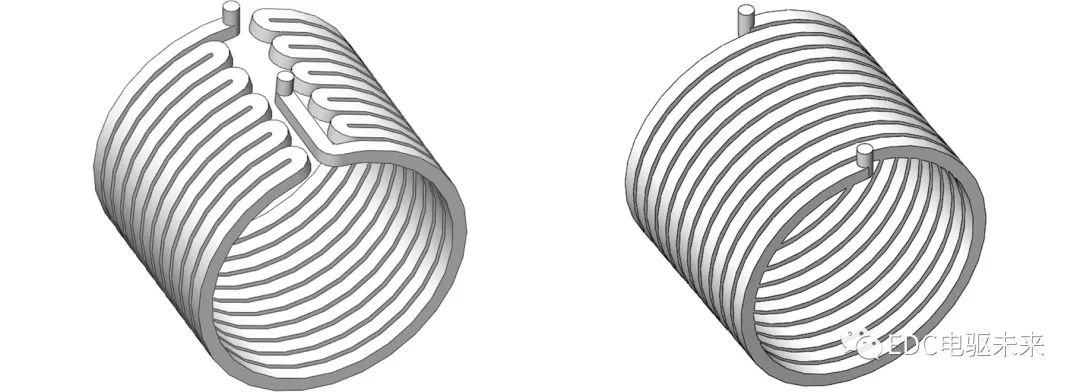
(a)圆周型循环水道 (b)螺旋型循环水道
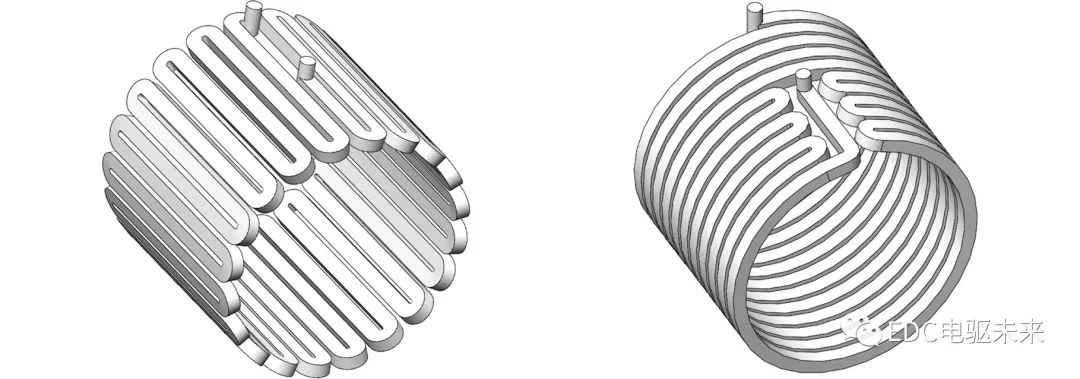
(c)轴向型循环水道 (d)复合型循环水道
图8 水冷电机流道结构
Fig.8 Flow channels for water cooling motors
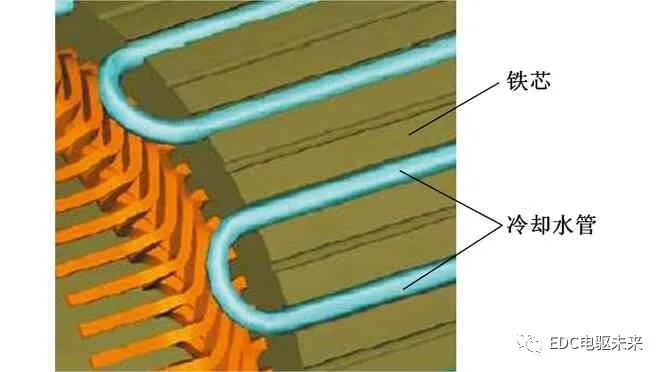
图9 定子铁芯集成循环水路结构图
Fig.9 Stator integrated with circulating
water channels
油介质具有良好的绝缘特性,可以在电机内部流动,与电机绕组、定子等发热部件直接进行热交换,也可以在机壳内部的流道中循环流动。这两种油冷方式分别是直接油冷和间接油冷。直接油冷又可以分为浸油式和喷油式两种。浸油式油冷是将电机的定转子都浸没在冷却油中,具有良好冷却效果的同时可以降低电机工作噪声,但是油的黏度较大,增加了电机转子旋转时的能量损失;喷油式油冷通过将冷却油喷淋到机壳内表面及定子端部实现对电机的高效散热。直接油冷特别是喷油式油冷的冷却介质与电机内部的发热部件直接接触,可显著降低电机绕组、定子等高发热部件的散热热阻,具有极高的散热效率,因此多用于高功率密度电机。油冷系统需要严格的过滤系统对油介质进行过滤,以避免油中的杂质对电机内部的绝缘层造成破坏。油冷散热系统的成本昂贵,因此其应用规模不如水冷散热系统广泛。
2.2.1 水冷散热系统
水冷散热系统的流道结构是影响其冷却效率的关键因素,研究人员通过优化流道结构参数提高了水冷散热系统的冷却效率。通过增加流道数量、在冷却流道中添加扰流结构和增加冷却水流量等方式可以有效提高冷却效率,但同时也导致压力损失明显增大。因此,在实际应用中需要综合考虑水道换热能力和压力损失以设计合适的水道结构。
吴柏禧根据水道压降、换热能力和水道均温性三项指标对圆周形冷却水道的结构进行了综合性优化,最终确定冷却流道的最优层数为3层,最优截面尺寸为宽8 mm、高11.2 mm。万珍平等分析了螺旋形流道结构参数对换热能力和压力损失的影响,结果表明增加流道螺旋圈数可以提高散热能力,但会导致压力损失明显增大;增加流道截面尺寸可以减小压力损失,但是对散热能力的影响较小。杨学威等采用传统铝型材挤压工艺制作了散热能力不低于8 kW、压力损失不超过15 kPa的轴向型冷却流道。BORGES等采用CFD仿真和红外摄像技术从22个水冷电机流道结构方案中筛选了3个最优模型进行加工,显著地缩短开发时间和降低成本,并进一步采用红外摄像技术验证了电机的温度分布。ZHENG等通过优化水道数量、水流速度和水道分布结构使电机稳定温度降低了13 ℃。郝嘉欣等在水冷电机冷却流道内增加了扰流片,并采用有限元分析法研究了扰流片厚度、高度和倾斜角度等尺寸参数对散热效果的影响,结果表明扰流片结构可以降低绕组温度约3 ℃,扰流片与冷却液流动方向夹角为30°、行间距8 mm、列间距5 mm的叉排方式为最优方案。范作智等设计了逆向双水道冷却结构,通过在电机流道内部设计折流筋,将传统流道的水路分割成两条方向相反的并行水路,如图10所示,有效缩短了冷却液流动的距离,解决了电机冷却液循环过程中温度梯度大的问题。
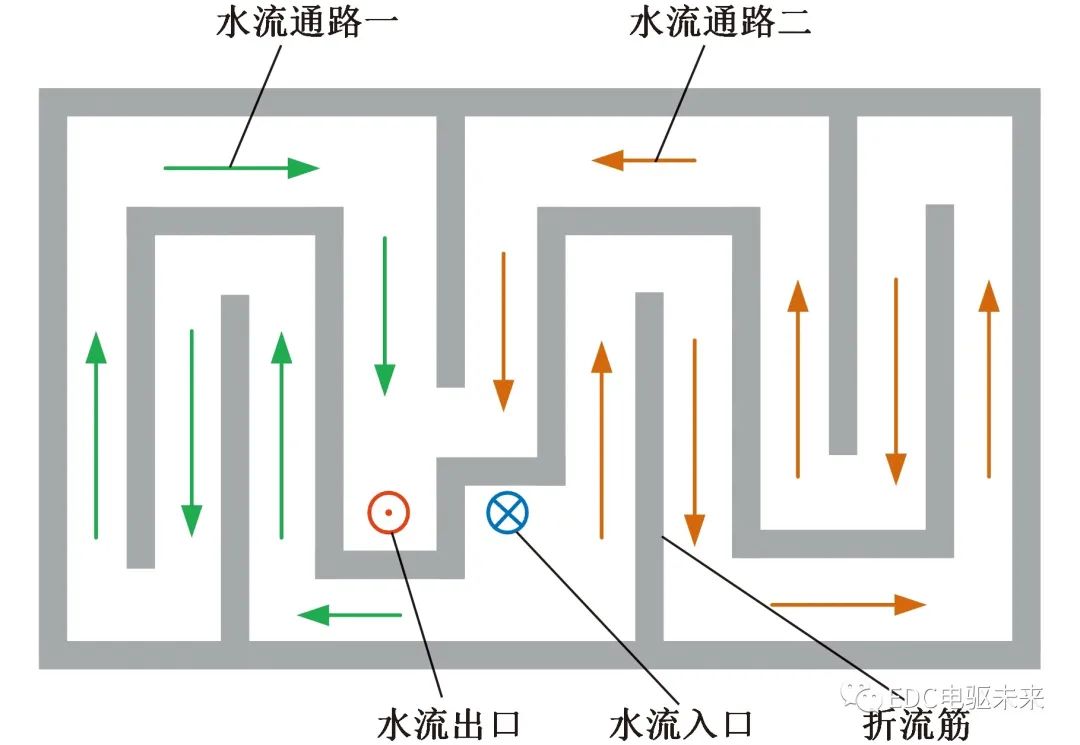
图10 逆向双水道冷却结构
Fig.10 Reversed double cooling channels structure
2.2.2 油冷散热系统
间接油冷散热系统与水冷散热系统类似,都是利用冷却介质在冷却流道内的循环流动带走热量。LASKARIS等设计了一款采用间接油冷散热系统的汽车牵引电机,冷却油在机壳内部的流道中循环流动散热,该散热系统可以带走5 kW的热量,当电机短时间工作在过载工况时,可以通过加快冷却油流动速度的方式带走25 kW的热量。LEE等采用转子间接油冷散热方案提高了电机的功率密度,如图11所示,冷却油在电机端盖、机壳和中空轴形成的流道中循环,直接对电机转子进行冷却。与机壳内部冷却方案相比,该方案可以有效降低电机绕组温度约38%。
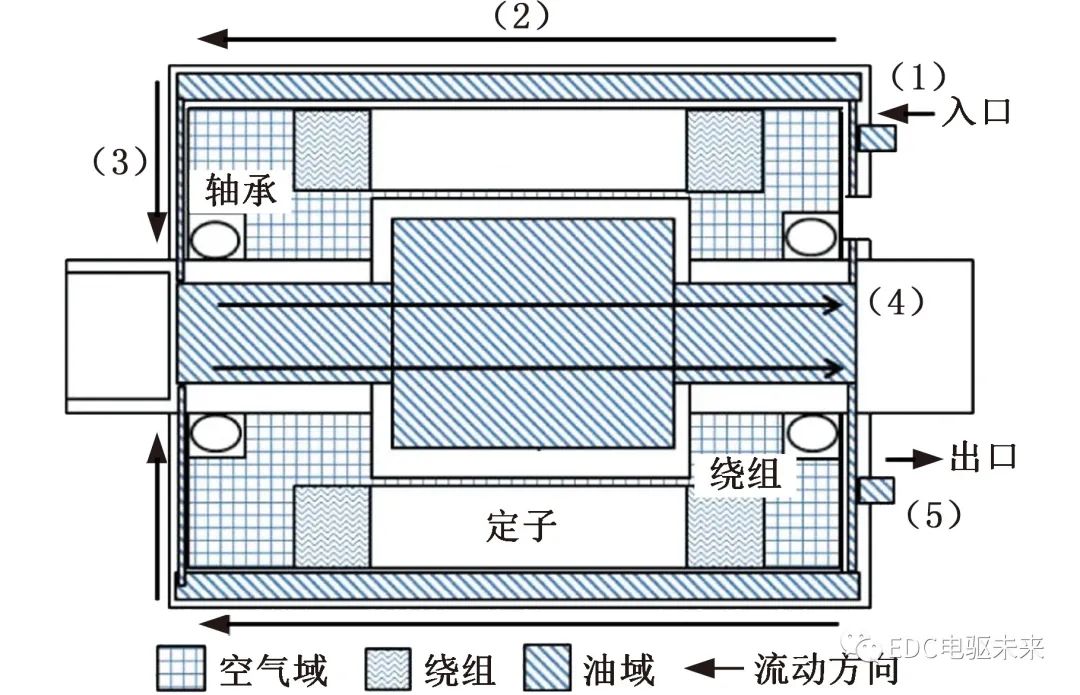
(a)冷却油循环路径
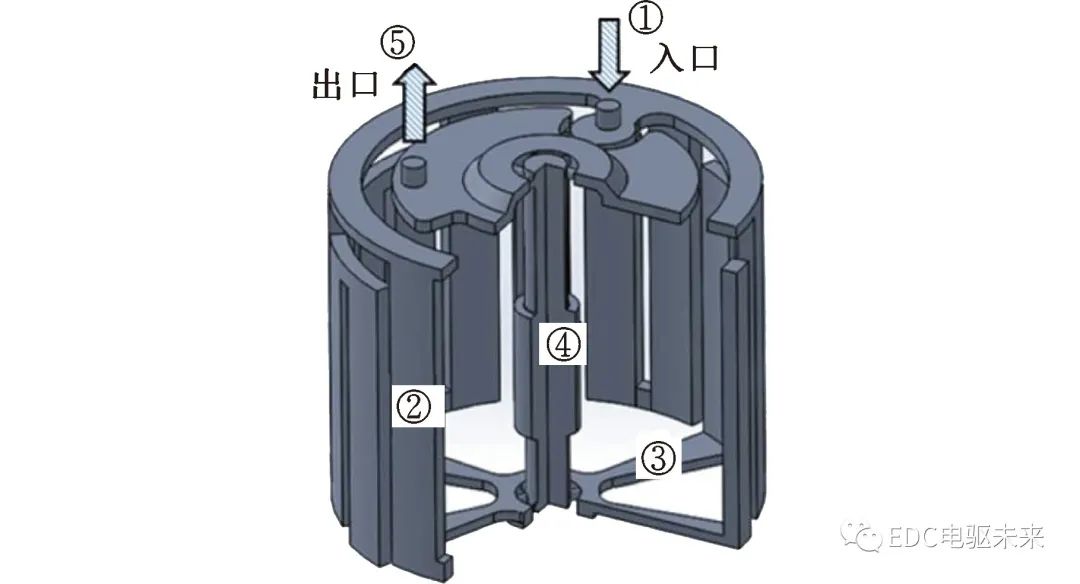
(b)冷却通道三维模型
图11 电机间接油冷散热系统
Fig.11 Indirect oil cooling system of motor
直接油冷散热系统的冷却油与电机内部发热部件直接接触,具有极高的散热效率,是解决高功率密度电机散热难题的有效方案。PONOMAREV等采用CFD法和热网格法分析了采用直接油冷散热系统电机的温升性能,建立了电机热仿真1/18模型,极大提高了有限元分析的效率。HUANG等采用CFD仿真法对比了间接油冷和直接油冷的散热效率。间接油冷即冷却油在机壳内部通道中循环流动;直接油冷是通过调整电机机壳结构,使冷却油直接接触定子的冷却方案,其结构如图12所示。仿真结果表明,如果冷却油驱动系统的功率保持不变,则直接油冷散热方案可以降低定子轭部的平均温度,提高电机的功率密度。
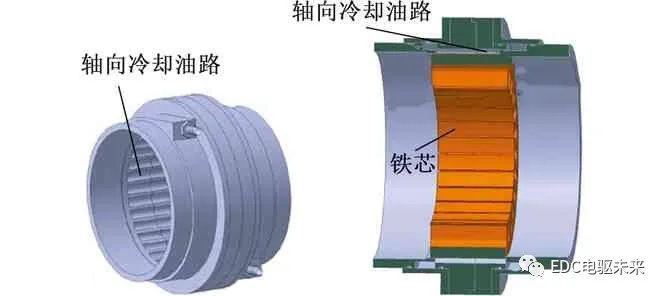
图12 直接油冷式电机机壳及其截面示意图
Fig.12 Casing of the direct oil cooling motor and its
sectional view
以额定功率35 kW的轮毂电机为研究对象,对比分析了喷油式油冷、浸油式油冷、浸油式循环油冷和间接油冷散热方案的冷却效率,研究结果表明,当电机转速为4400 r/min时,喷油式油冷的平均传热系数可达5270 W/(m2·K),有效降低绕组温升11.6%~25%。DAVIN等实验研究了冷却油喷射模式对电机冷却效率的影响,研究结果表明当冷却油在绕组顶部滴注时,冷却油在绕组端部流过时具有较高的流速,对绕组端部的冷却效果最好。
液冷散热系统,特别是直接油冷散热系统具有较高的散热效率,能够解决高功率密度电机发热严重的问题,在车用驱动电机散热领域得到了广泛应用。液冷散热系统需要额外的冷却系统装置,在一定程度上降低了电机系统的可靠性,增加了系统成本。水冷散热系统存在锈蚀、堵塞和渗漏等隐患,一旦发生泄漏将直接危及电机的安全,因此需要对水冷散热系统的循环管路进行高可靠性的密封以确保电机系统运行的安全性与可靠性。相比于水介质,油介质具有绝缘特性好、介电常数高、凝固点低和沸点高等优势,可以提高电机系统对外界环境的适应性,避免气蚀、水垢等腐蚀危害。然而油介质的质量热容和热导率都远小于水介质,因此间接油冷散热系统的效率低于水冷散热系统,而直接油冷散热系统的冷却油与电机发热部件直接接触,其散热效率远高于水冷散热系统。
通过以上研究可以发现:高效化是电机散热系统的长期发展趋势;通过优化循环水道结构、调整水道截面形状和增加扰流结构等方式可以在一定程度上提高水冷散热系统的效率;在电机高发热部件与机壳之间搭建额外热路、缩短冷却介质与电机关键发热部件之间的传热路径是提高水冷散热系统效率的有效方案与新方向。
蒸发冷却散热系统利用低沸点冷却介质的相变循环实现对电机的高效冷却。当低沸点、高绝缘系数的冷却介质与电机内的发热部件接触时,冷却介质吸收大量的热量并发生气化,气态的冷却介质在冷凝器遇冷转化为液态,利用冷却介质的气液相变循环实现电机的高效散热。根据冷却介质沸腾温度的高低,可以将蒸发冷却分为低温制冷式蒸发冷却和常温制冷式蒸发冷却;根据冷却系统的结构可以将蒸发冷却分为管内冷却和浸没式冷却;还可以根据冷却介质的循环系统是否采用驱动泵,将蒸发冷却分为自循环蒸发冷却和强迫循环蒸发冷却两大类。
张学礼验证了蒸发冷却散热系统的效率显著高于油冷和水外冷,并研究了冷却介质液面高度对冷却效果的影响。蔡静将全封闭无泵自循环蒸发冷却系统应用于立式电机,证明了回液管为非满液位时,冷却介质的循环动力由回液管内液柱高度产生的静压差和循环介质具有的压头两部分组成。刘长红等建立了自循环蒸发冷却电机的热网络模型,并对比验证了模型的准确性。国建鸿等对采用强迫循环蒸发冷却系统的300 MW汽轮发电机的绕组温升性能进行研究,采用分相模型计算了两相流动的阻力,提出了通过流量调节控制蒸发点位置、防止两相流动阻力过大引起气阻的方法。温志伟等首次提出了铁芯浸润式冷却与绕组强迫循环冷却相结合的蒸发冷却电机散热方案,分析了负荷变化对电机温度场的影响。研究结果表明蒸发冷却方式与强迫循环内冷方式结合可以有效抑制电机温升,提高了电机长期运行的稳定性。侯哲分析了电流密度、冷却介质流量和电机转速对冷却效果的影响,并指出冷却介质流动不畅产生的局部缺液现象是导致绕组产生温差的主要原因。
我国自主研发的蒸发冷却散热系统具有冷却效率高、能耗低和可靠性高等优势,在兆瓦级汽轮发电机组设备中得到了广泛应用。目前蒸发冷却技术仍存在新型冷却介质选择、气液两相流的流动特性和传热计算方面的问题。从保护环境的角度出发,传统氟利昂类介质不能继续使用,新型具有良好物理、化学特性和绝缘特性的冷却介质还有待开发。气液两相流的传热问题缺乏成熟的理论,还未形成完备的设计计算方法。此外,蒸发冷却系统的结构复杂,目前还未出现千瓦级电机设备采用蒸发冷却技术的应用案例。开发环境友好型冷却介质、完善两相流传热计算理论以及系统结构简单化、小型化是蒸发冷却技术的发展方向。
额外热路增强型散热系统是在电机原有风冷、液冷散热系统的基础上建立额外高效热路以提高电机散热效率的增强型电机散热方案。受电机内部绝缘漆、绝缘纸和空气等低热导率材料的限制,电机内部的关键发热部件,特别是端部绕组产生的热量往往不能快速传递至冷却壳体,造成热量在电机关键部件大量积聚,形成局部高温区。在电机关键发热部件与冷却壳体之间构建额外热路可以将热量快速传递至机壳,解决电机内部高发热部件的散热难题。
导热树脂、导热胶和导热陶瓷等具有高热导率和良好绝缘特性的材料是常用的构建电机额外热路的材料,其物理性能参数如表2所示。此外,还可以在定子槽或定子铁芯内部设置额外的导热路径以提高电机的散热效率。
表2 常用导热绝缘填充材料的物理性能参数对比
Tab.2 Comparison of physical properties of potting materials
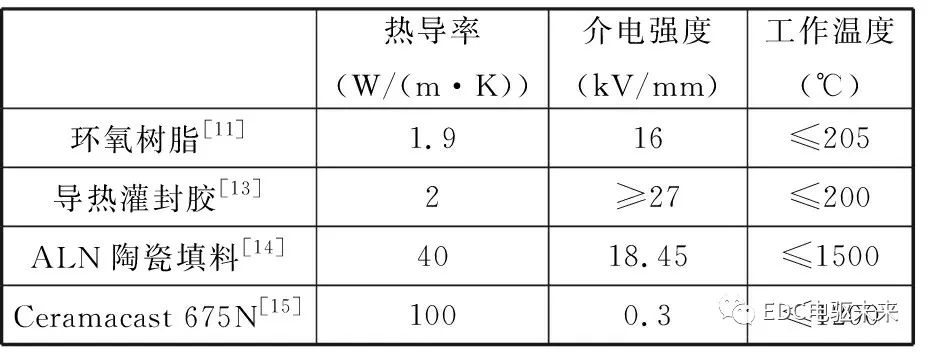
SUN等提出了采用导热灌封胶强化散热的水冷电机散热系统,在电机端部绕组与机壳之间的缝隙中灌封导热材料,该导热灌封胶由液态灌封,加热固化后保持固体状态,具有良好的导热性能和绝缘特性。在电机端部绕组与机壳之间增加高效热路,可有效降低电机绕组稳定温度约27.3 ℃。导热陶瓷材料具有较高的热导率,但是昂贵的成本限制了导热陶瓷材料在实际生产中的应用。目前,大多采用导热树脂和导热胶材料提高电机的散热效率。
GALEA等在水冷电机的定子槽内嵌装具有高热导率的热路并建立了电机热路模型,如图13所示,定子槽内的热路结构可以根据定子槽型进行调整。研究结果表明,在同等工作状态下,该方案可以有效降低绕组温度约40%。
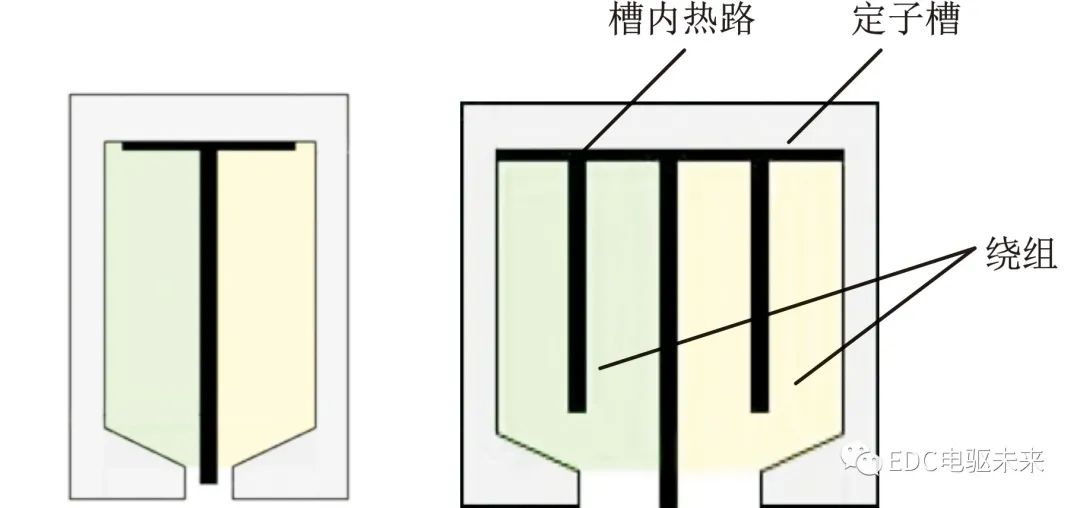
图13 针对不同槽型设计的槽内热路散热方案
Fig.13 Cooling schemes of internal thermal circuit
for different slot designs
POLIKARPOVA等在轴向磁通永磁同步电机的定子与机壳之间安装了导热铜棒,同时在电机绕组端部与机壳之间灌封了导热陶瓷材料,如图14所示,采用有限元仿真与实验测试相结合的方法验证了散热方案的有效性,结果表明该方案可以降低绕组温升13~17 ℃。
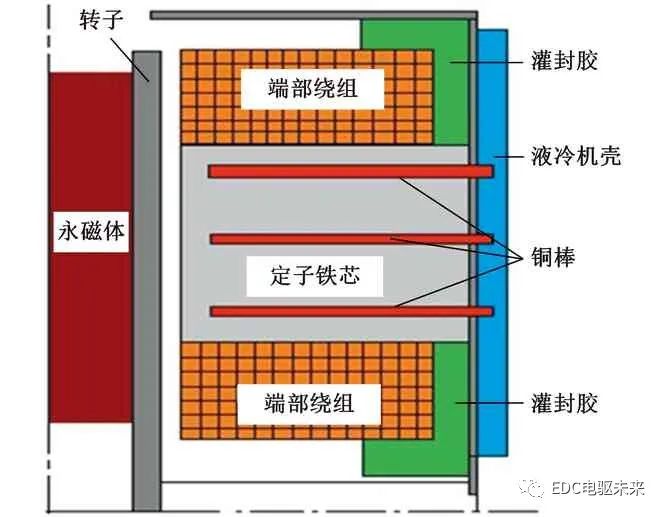
图14 采用导热胶和铜棒增强散热的水冷电机
Fig.14 Potting material and copper bars enhanced
water cooling motor
近年来,相变热管理技术得到了飞速发展,在大功率LED、绝缘栅双极型晶体管(IGBT)、笔记本电脑和智能手机等高热流密度电子器件中得到了广泛应用。相变热管理技术主要包括相变储热技术和相变传热技术两大类。相变储热技术利用相变材料的相变潜热储存大量的热量,可以达到缓解温度冲击、抑制温升的作用,石蜡是常用的相变储热材料。相变传热技术利用工质的气液相变循环实现高效传热的技术。热管是常用的相变传热器件之一,主要包括壳体、吸液芯和工质三部分,其工作原理如图15所示。热管的壳体是密封结构并进行了抽真空处理,吸液芯附着在壳体内壁,工质在蒸发段遇热气化并吸收大量的热量,导致蒸发段气体压力上升并驱动工质气体向冷凝段移动;蒸汽在冷凝段遇冷液化并释放热量,冷凝后的液态工质在吸液芯的驱动下回到蒸发段。
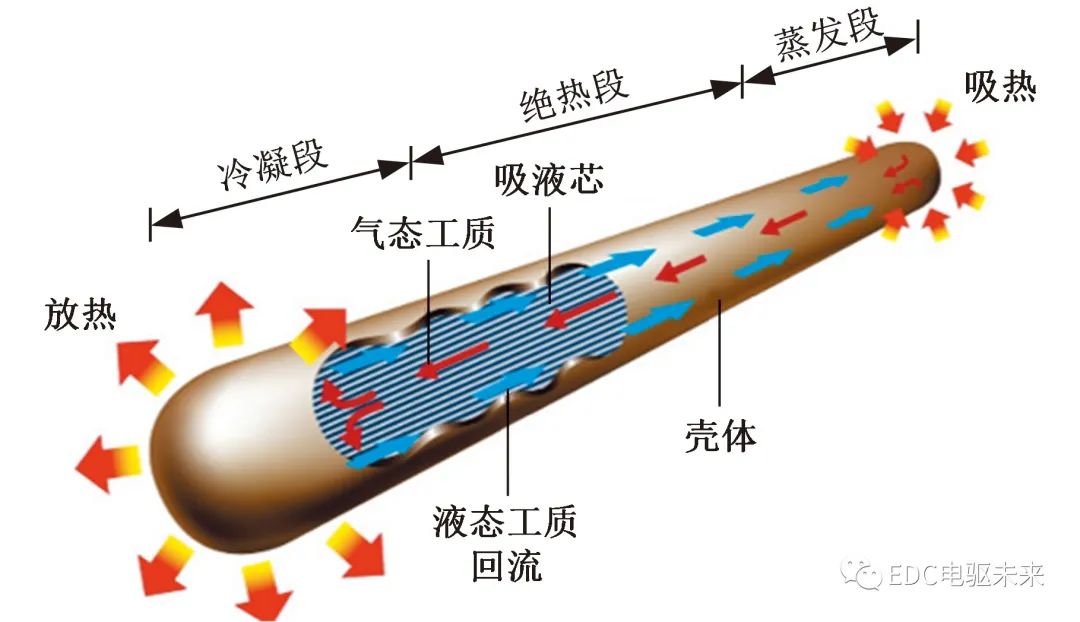
图15 热管工作原理
Fig.15 Working principle of heat pipe
将相变热管理技术应用于电机散热系统,在电机高发热部件与冷却壳体之间搭建额外相变热路,可以有效延长电机稳定运行时长、抑制电机温升,实现电机高效散热。
BELLETTRE等提出了采用相变材料抑制绕组端部温升的散热优化方案,并采用热仿真模型和试验证实了采用低熔点、高相变潜热的相变材料可以显著抑制端部绕组的温升,并以此为依据确定镓和石蜡(P116)分别是抑制端部绕组温升的最佳金属和非金属相变材料。WANG等在电机机壳内部引入石蜡以缓解电机的温升冲击,如图16所示,将电机机壳加工为中空结构并灌注石蜡,并采用前后端盖进行密封以避免液态石蜡泄漏。有限元仿真及实验测试证明,当电机工作在连续模式时,机壳内部的石蜡可以有效延长电机的运行时间约32.7%;当电机工作在周期模式时,机壳内部的石蜡可以降低电机的峰值温度约7.82 ℃。
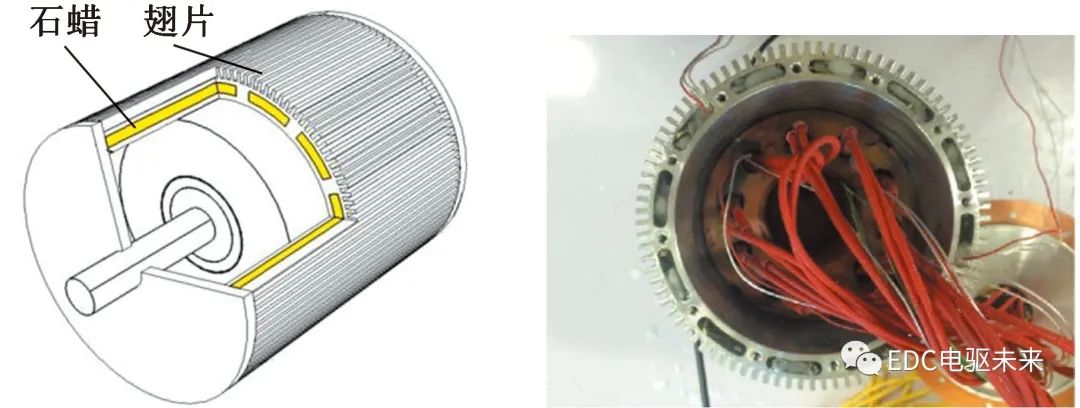
图16 风冷电机机壳内部灌注石蜡示意图及照片
Fig.16 Schematic diagram and photo of paraffin
encapsulated in the casing of air cooling motor
PUTRA等在风冷电机的机壳上安装了8支L形热管,将热管的蒸发段套在楔形块内,楔形块嵌装在电机相邻两个翅片内,热管的冷凝段安装了热沉,并利用电机端部的风扇对热管进行冷却,测试结果表明机壳外部安装的热管可以有效降低电机表面温度约33.8 ℃。HASSETT等提出了在电机定子内部嵌装热管以强化电机散热的方案,FEDOSEYEV等提出了在电机转轴内部嵌装热管优化电机转子散热的方案,其方案示意图见图17。
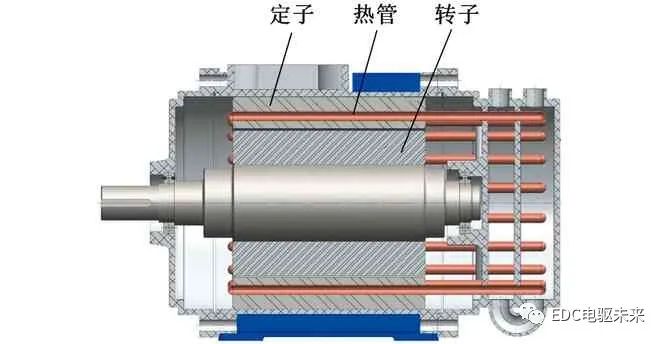
(a)定子嵌装热管散热方案
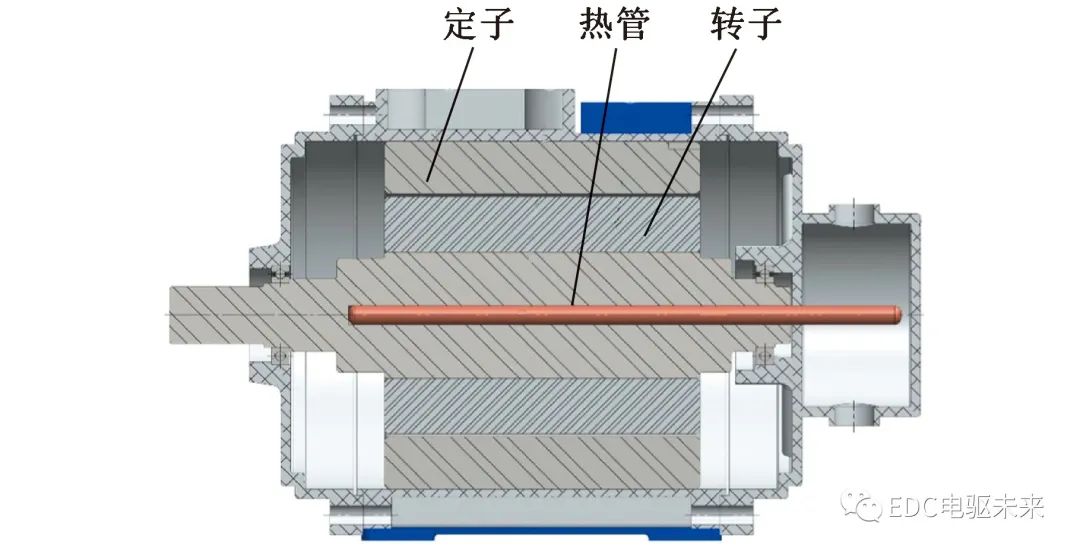
(b)转子嵌装热管散热方案
图17 定子和转子嵌装热管散热方案
Fig.17 Heat dissipation scheme of heat pipes
embedded in stator or in rotor
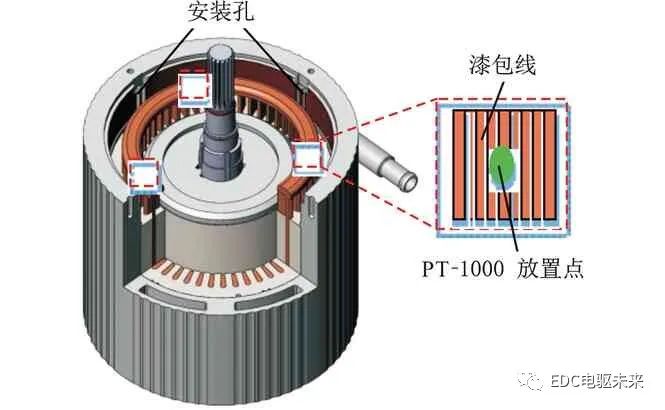
(a)水冷电机模型图
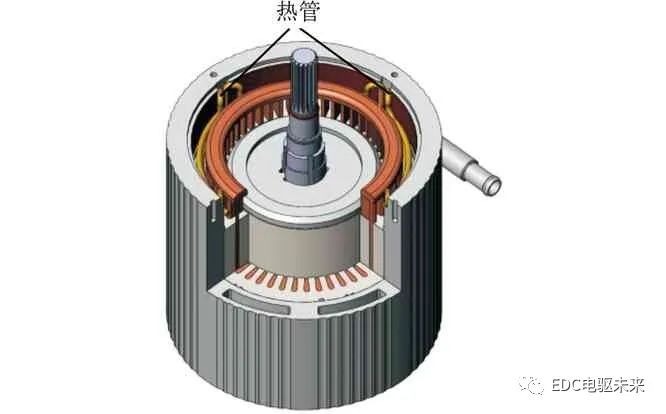
(b)热管强化散热的水冷电机
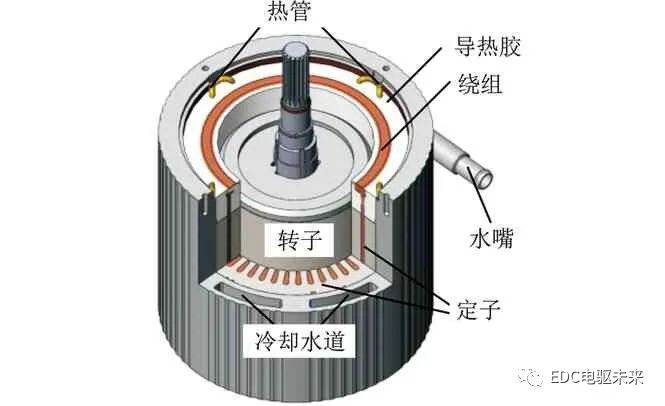
(c)热管和导热胶强化散热的水冷电机
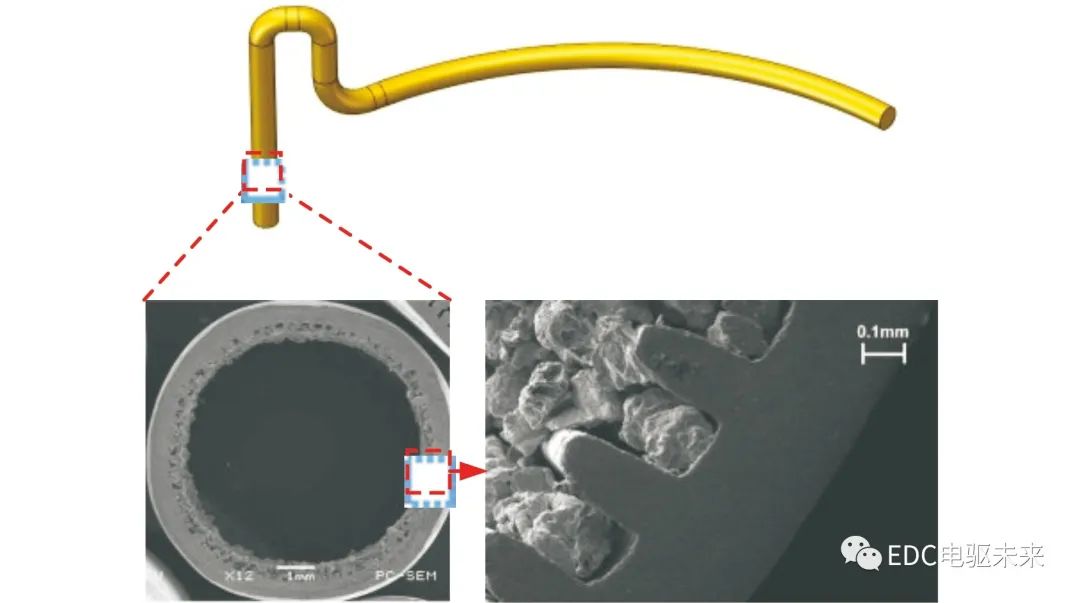
(d)热管截面电镜图
图18 基于3D热管的水冷电机散热方案
Fig.18 Cooling system of water cooling motor
with 3D heat pipes
SUN等针对新能源汽车用永磁同步电机绕组发热量大、散热环境恶劣和温升过高的问题,开发了基于3D相变热管的水冷电机散热方案。如图18所示,将3D热管的蒸发段通过绝缘纸与电机端部绕组绑接在一起,冷凝段嵌装在水冷机壳中;并提出了采用导热灌封材料固定相变热管的优化方案。测试了电机在多个转速、转矩和冷却条件下的温升性能,结果表明采用3D热管优化电机端部绕组散热的方案可以有效降低绕组温升约10 ℃;采用导热灌封胶优化的热管散热方案可以降低绕组温升22.9 ℃,延长电机在峰值工况下的稳定运行时长约50.6 s。因风冷电机机壳中部与定子铁芯直接接触,而机壳的热导率和风冷系统的散热效率相对较低,造成热量在机壳中部大量聚集,故机壳中部温度明显高于两端温度。针对该问题,FANG等提出了在机壳内部嵌装热管的优化方案,如图19所示,沿机壳圆周方向均匀嵌装24支热管,利用热管极高的热导率将机壳中部的热量快速传递至机壳两端,避免机壳中部温度过高,提高机壳的均温性,有效降低电机额定工况下的绕组温度22.3%,分别延长电机在高速和高转矩工况下的运行时长28.6%和21.4%。
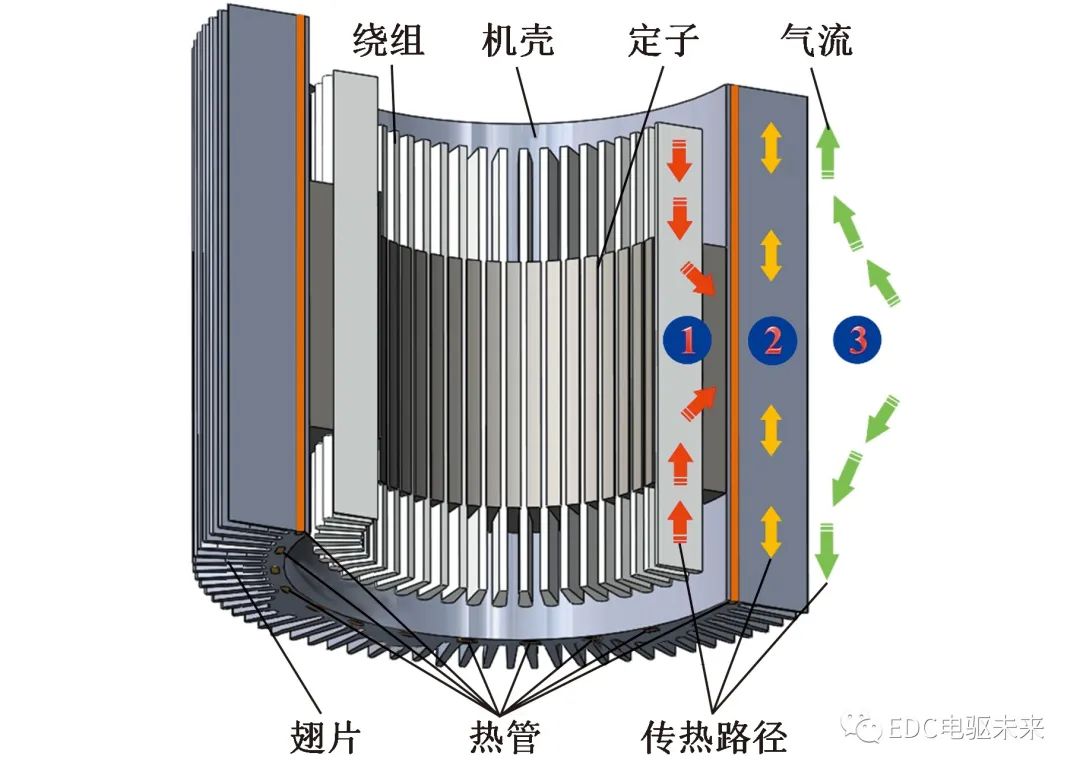
图19 风冷电机机壳内部嵌装热管强化散热方案
Fig.19 Air-cooling motor with heat pipes embedded in
the casing to enhance heat dissipation
额外热路增强型散热方案,特别是采用相变元件构建额外热路的散热方案是目前电机散热系统高效化发展的新思路。相变传热元件具有热导率极高、价格低廉和无需外部动力等优点,可以将电机发热部件积聚的热量快速传递至冷却介质,提高电机散热效率。目前,关于相变强化电机散热方案的研究大多是研究其对电机温升性能的影响,缺乏其对电机磁场分布、效率及可靠性等方面的系统性研究。
系统性研究相变强化散热方案对电机运行情况的影响,实现其产业化应用对抑制电机温升、提高电机功率密度具有重要意义。
风冷、液冷、蒸发冷却和额外热路增强型散热系统具有各自的优势和应用场景,根据电机的发热功率、生产成本和安装空间等要素,选取合适的散热方案是提高电机功率密度、运行效率、可靠性和极端环境适应能力的关键。总体来说,随着电机向高功率密度、高集成化和高可靠性方向发展,电机散热系统也逐渐向高效化、高可靠性和轻量化等方向发展。
风冷散热系统具有结构简单、可靠性高和成本低廉的优势,主要应用于发热量小、对可靠性要求较高的小功率电机。液冷散热系统是中到大功率电机最常用的散热方式,具有较高的散热效率,然而液冷散热系统需要附加额外的冷却液循环系统,增加了电机系统的成本,降低了系统整体的可靠性。蒸发冷却散热系统是解决兆瓦级大功率发电机组散热的有效手段,然而其复杂的系统组成限制了其在千瓦级电机散热领域的应用。优化蒸发冷却系统的系统结构、提高其集成化程度是蒸发冷却散热系统的主要发展方向。
对于提高风冷和液冷散热系统的冷却效率,已有研究人员进行了大量的探索与优化,采用相变材料或器件提高风冷和液冷散热系统的冷却效率是电机散热领域的新思路。利用相变器件极高的热导率,将电机主要发热部件的热量快速传递至机壳,避免热量在电机关键部件的积聚,是实现电机高效散热的有效手段和新方向。目前,针对额外热路增强型散热方案的研究大都集中在其对电机温升的抑制效果,仅对该方案的散热效果进行了验证,缺乏从电机设计阶段开始的系统性设计与研究。值得注意的是,电机的温度场与电磁场密切相关,采用额外热路增强型散热方案的电机温升显著降低,其电磁效率必定有所提高。同时,额外热路增强型散热方案出色的降温效果理论上可以使电机在一定的过载工况下长期稳定运行,提高电机的功率密度。因此,系统性研究额外热路增强型散热方案对电机温升抑制、磁场分布以及运行效率的影响,验证并提高其可靠性和集成化程度是其发展的主要方向。
高效化是电机散热系统的主要发展方向,额外热路增强型散热方案是实现电机散热系统向高效化发展的新方向。立足于电机设计阶段,开发高可靠性的额外热路集成式散热方案不仅可以提高电机的散热效率、抑制温升,还可以提高电机系统的集成化程度,实现电机向高功率密度、高集成化和高可靠性方向发展。
高效可靠的散热系统是抑制电机温升、提高电机运行效率和功率密度、提高电机运行稳定性和延长电机寿命的重要基础。风冷、液冷、蒸发冷却和额外热路增强型散热系统在各自的应用领域发挥着重要的作用并取得了显著的降温效果,针对电机的应用场景、发热功率和生产成本等因素选取恰当的散热系统是实现电机高效散热的关键。目前,电机散热系统正随着电机逐渐向高效化、高可靠性和高集成化方向发展。结合当前电机散热系统的研究现状和发展趋势,今后可以针对以下几个方面开展研究。
(1)研究风冷散热系统翅片尺寸结构、翅片分布位置和风速等因素与散热效率之间的关系,建立并完善翅片结构参数与散热效率、生产成本之间的关系模型。风冷散热系统在小功率电机散热领域具有不可替代的地位,提高其散热效率、降低其生产成本具有重要意义。建立并完善翅片结构参数与散热效率、生产成本之间的关系模型,进一步推动风冷散热系统向高散热效率、低生产成本方向发展。
(2)建立液冷散热系统流道几何参数与散热效率、水道压降之间的理论模型。流道几何参数是影响散热效率和水道压降的关键因素,目前主要通过有限元仿真法研究其对散热效率和水道压降的影响,缺乏完善的理论模型。
(3)建立完善的气液两相流传热模型,提高蒸发冷却技术在电机系统中的集成化程度。蒸发冷却技术具有极高的散热效率,在兆瓦级发电机组散热系统中得到了广泛应用,目前关于蒸发冷却技术气液两相流的传热理论还有待完善;同时,蒸发冷却技术的系统组成相对庞大、复杂,应推动蒸发冷却技术向小型化、集成化方向发展,提高蒸发冷却系统与电机系统的集成化程度,从而实现蒸发冷却技术在千瓦级电机散热系统中的应用。
(4)系统性研究额外热路,特别是相变器件对电机散热系统冷却效率的影响。采用导热绝缘材料、相变传热器件在电机发热部件与散热系统之间构建高效热路是提高电机散热效率的新方向。在电机设计阶段充分考虑额外热路对电机温升的抑制效果,调整电机电磁方案以提高电机功率密度,优化电机结构以提高导热胶、相变器件与电机的集成化程度,提高相变强化散热系统的可靠性,从而推动相变强化电机散热系统的产业化应用。