连杆作为机械传动中的重要基础零件,起着连接与传动作用,使用中零件性能直接影响零件使用寿命、传动效率等。对机器零部件性能的要求,主要是较好的综合力学性能,这也就要求在较高的韧性和延展性的前提下,有较高的强度,包括屈服强度、抗拉强度、屈强比、疲劳极限等。
零件用42CrMo 材料,按含碳量分为中碳钢,也可称为调质钢,由于在碳钢的基础上加入合金元素,成为合金调质钢,又称中碳合金钢。对碳钢材料来说,大型零件淬透性很差,加入合金元素,提高钢的淬透性,强化铁素体,细化晶粒与形成合金碳化物等,使钢具有更好的性能,而合金元素只有通过淬火或者调质状态才发挥作用,在退火状态下其机械性能与碳钢并没有什么显著区别。
孔精加工方式多采用铰孔及镗孔两种,铰孔的主要方法又可分为手工铰孔及机床铰孔,镗孔现可通过数控机床镗孔加工实现,两类加工方式虽不一致,但都是在粗加工或者半精加工孔后,刀具(铰刀或镗刀)在工件孔壁上去除微量残余金属层,来提高孔的尺寸精度、降低孔内壁表面粗糙度,从而达到孔精加工要求。
金属材料热处理方式
金属材料热处理过程
中碳合金钢的调质处理一般是切削成形后,为使之获得所要求的综合性能而进行的热处理,通常包括淬火和高温回火,也称为调质处理,调质处理一般安排在粗加工之后,精加工之前。
淬火处理:在一般淬火时,工件淬火使之获得完全马氏体组织,与材料的淬透性及尺寸有关,42CrMo 材料淬透性甚好,且零件薄更容易淬透。
回火处理:调质处理中的回火,目的是调整工件淬火后的显微组织,获得所需要的综合性能,如降低其硬度和强度,借以提高其韧性和塑性;同时也消除因淬火而产生的内应力。回火一般在高温下进行,但须避开产生回火脆性的温度范围。回火保温后,也应使之快速冷却通过产生回火脆性的温度区,必要时可采用油冷或水冷的方式。回火温度和时间的选择,以达到所要求的性能为准。高温回火热处理温度简图见图1。
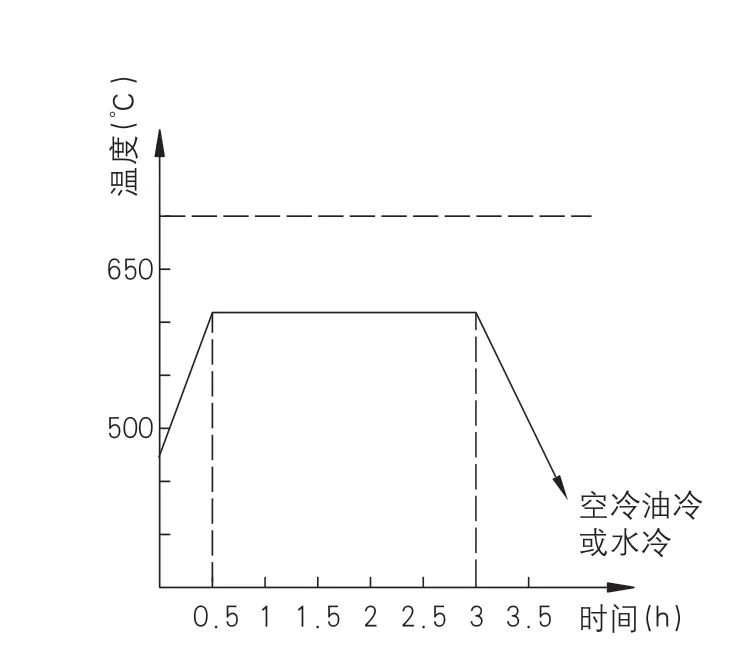
图1 高温回火热处理温度示意图
金属材料热处理变形问题
某零件100(图2)为细长形零件,零件技术要求:材料为42CrMo;热处理为淬透,淬火+高温回火,表面和核心硬度 33 ~38HRC。
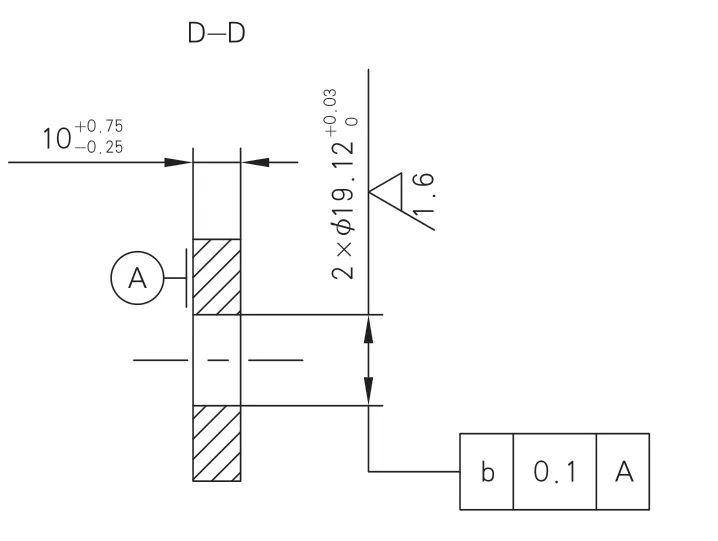
图2 某零件尺寸图
零件属于细长薄零件,热处理前零件平面状态见图3,高温回火会导致零件变形,具体如图4 所示,在厚度、宽度方向均会发生扭弯,板料严重变形成麻花状。
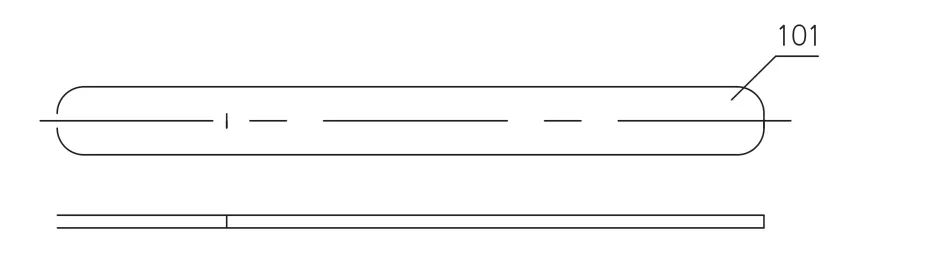
图3 某零件热处理前示意图
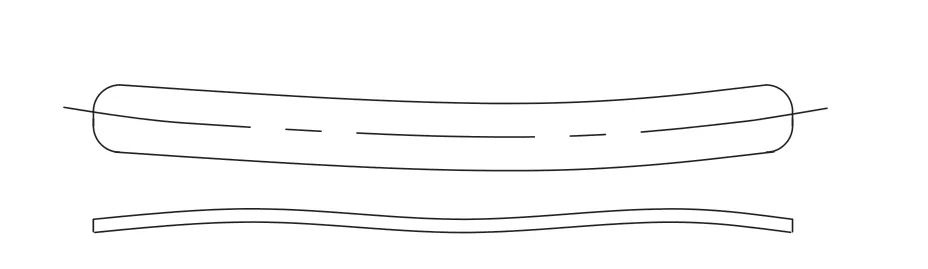
图4 某零件热处理后示意图
若零件扭曲严重,校平后零件的平面度与直线度与热处理前相差过大,难以恢复热处理前零件平面状态,只有通过在加工热处理工序前增加更多余量的方式来加工,以满足图纸尺寸公差要求,严重影响生产效率。因此,可在热处理工序中进行人为干预控制零件外形状态,以减小零件高温过程中变形。
为防止零件变形,可通过在零件上增加压块或者用螺纹紧固来压紧零件,减小变形。在零件上增加压块,压块过厚重,热传导减慢,影响零件加热升温至高温回火温度;若螺栓连接紧固,单次使用方便快捷,但是重复使用在高温回火过程螺纹会拉长变形,热处理次数增多后螺栓上螺纹会与螺纹孔内螺纹融合,无法实现较高利用率。
为满足实际生产加工要求,需设计一种零件专用工装夹具压紧零件,保证零件在满足热处理要求同时,也确保零件在高温条件下变形小,减少后续校直工序工作量,提高零件合格率及生产效率,且工装能重复使用。
防热处理变形夹具研究
为实现上述目的,设计了一套热处理工装(图5),主要包括零件座,挡板,吊耳,楔块(图6)。
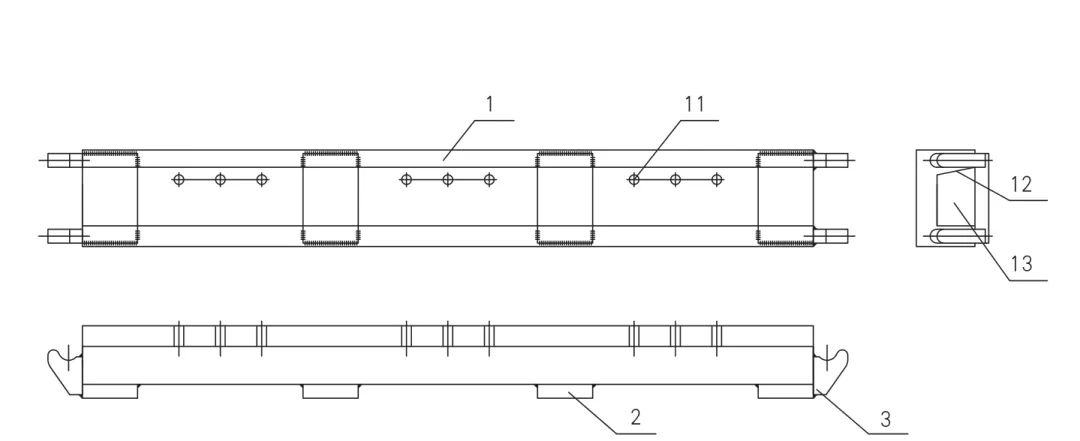
图5 热处理工装部件示意图
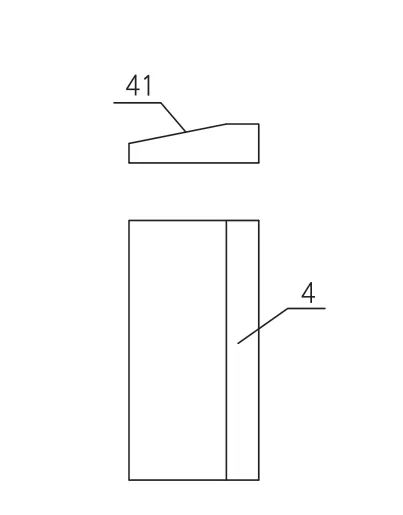
图6 楔块的结构示意图
其特征在于,零件座为整料一体数铣加工,呈U形;挡板有四块,焊接在零件座上;吊耳焊接于零件座两端面;挡板中间有三段隔断空处,方便打入楔块;零件座上设有通孔,在热处理完成后能用棒料穿过通孔将楔块反向打出,方便拆装;斜面与楔块的斜面斜角一致,两者通过面接触,使楔紧力更大;整体工装(图7)左右两端贯通,呈方形管状,保证整个夹具在热处理期间实现更好更快的热传导,达到所需要的热处理温度。
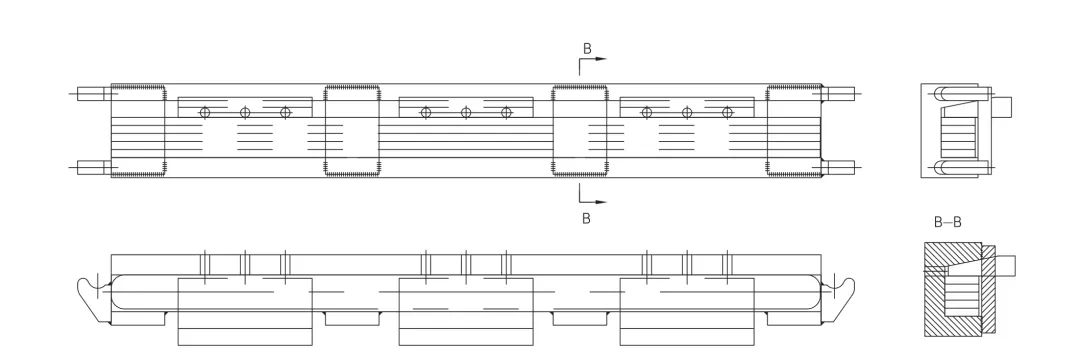
图7 热处理工装的总装图
防变形夹具使用步骤
具体使用步骤如下:将零件100 依次叠加装入零件座的内腔中,再将楔块打入零件与零件座之间,使得斜面与斜面楔紧,然后利用零件座端面的两个吊耳将工装与夹具吊起放入热处理炉中进行高温回火,高温回火结束冷却至室温,将棒料穿过零件座中间部分的通孔中反向打出楔块,使之与零件100 和零件座脱离配合,再取出零件。
整个工装并不是封闭型,在热处理高温回火阶段使零件在减少变形的前提下能更好地升温加热至热处理所需要的温度。
零件加工工艺研究
零件加工难点分析
零件的加工难点集中在两处,热处理高温变形校平问题及两孔表面粗糙度问题。
零件热处理后由于机械性能及硬度的变化,对后续孔精加工产生影响,需根据热处理要求相应调整工艺方案,以满足零件尺寸公差要求及使用要求。现通过数控与钳工加工方式对比,寻求最适合车间实际生产所需求的工艺方案。
铰孔工艺方案
⑴方案一。方式:数控铣钻镗孔至尺寸要求。内容:在数控机床钻孔至
φ16mm,并保证孔中心距,铣孔至
φ18.5mm,镗孔至
φ(9.12+0.030)mm。结果:零件孔位及孔表面粗糙度及形位公差均能满足图纸要求,孔径尺寸偶尔出现超差情况。
⑵方案二。方式:钳工利用钻孔工装扩钻铰孔。内容:钻孔至
φ16.5mm,扩孔至
φ18.9mm 再铰孔
φ(19.12+0.030)mm。结果:零件孔形位公差均能满足图纸要求,出现零件铰孔后尺寸偏小,反复铰孔均不能满足零件孔径公差,大部分孔表面粗糙度集中在Ra1.6 ~Ra3.2μm 范围内,孔内有划痕状凹槽。
⑶方案三。方式:钳工利用钻孔工装扩钻粗精铰孔。内容:钻孔至
φ16.5mm,扩孔至
φ18.8mm,粗铰孔至
φ19mmH7,最后精铰孔
φ(19.12+0.030)mm。结果:零件孔位、孔径、孔表面粗糙度及形位公差均能满足图纸要求,零件合格率高,效率中等。
⑷方案四。方式:数控加工孔后钳工铰孔。内容:数控钻孔至
φ16mm,铣孔至
φ19mm,钳工铰孔
φ(19.12+0.030)mm。结果:零件孔位、孔径、孔表面粗糙度及形位公差均能满足图纸要求,合格率高,效率高。
⑸方案五。方式:数控加工孔后钳工铰孔。内容:数控U 钻钻孔至
φ19mm,钳工铰孔
φ(19.12+0.030)mm。结果:零件孔位、孔径、孔表面粗糙度及形位公差均能满足图纸要求,批产零件合格率高,加工效率高。
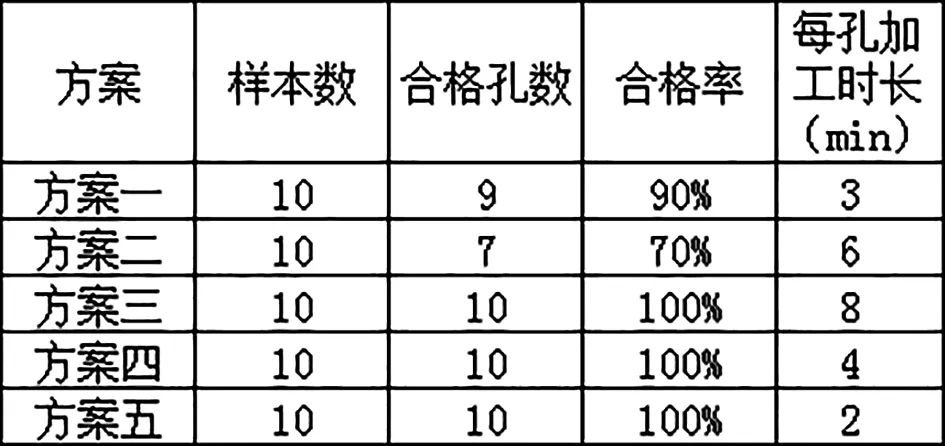
图8 各方案数据统计
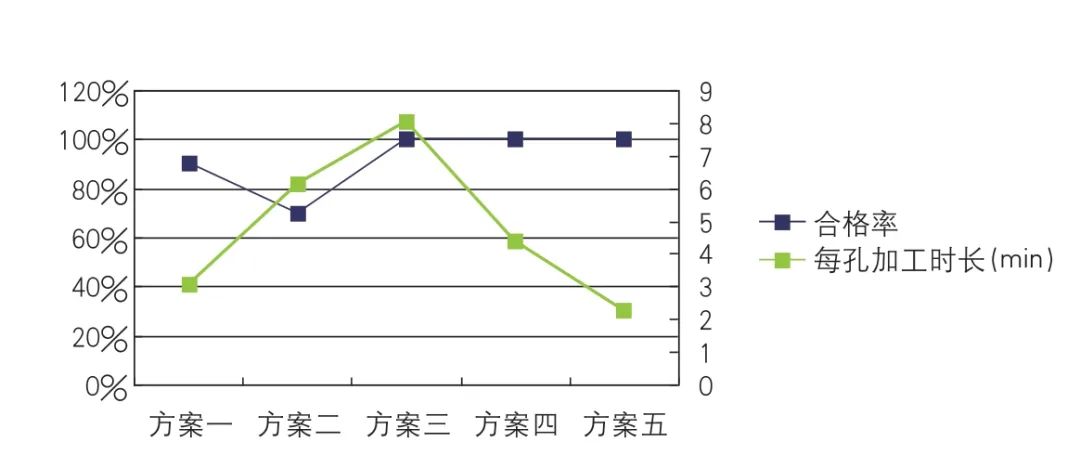
图9 各方案合格率及加工时长折线图
由于各车间实际情况差异大,数控机床、钻床及钳工人数不一,可根据实际情况调整选择不同工艺,以选出更适合当下加工的最优方案,保证批产零件合格率的前提下提高实际生产效率。
结论
零件结构虽简单,但在生产过程中会涉及多方面问题:机械性能、热处理方式、铰孔方法等,需要在实际加工过程中不断实践以攻克加工难点。机械加工学习过程漫长而任重道远,吾辈需上下而求索。
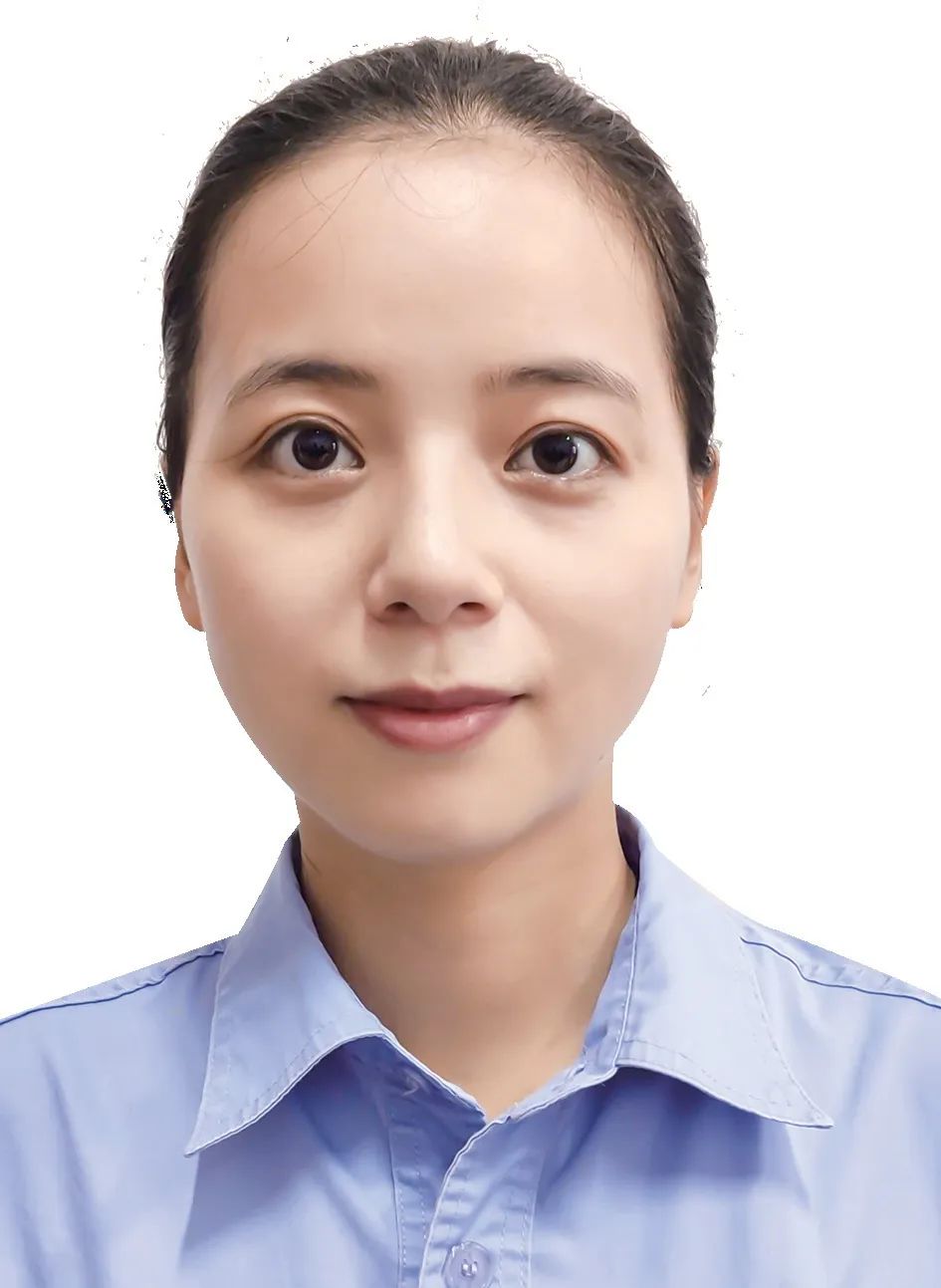
曹小燕助理工程师,主要从事零件图纸施工,工艺流程及工艺指令编写,相关工装夹具设计,数控及线切割编程。
——文章选自《锻造与冲压》2022年第15期