基于纯电动汽车安全及续驶里程需求,轻量化设计被摆在突出的位置, 而单纯追求车身轻量化可能会降低汽车的碰撞安全性。
而先进高强度钢热成型技术在汽车领域的应用,可以很好的解决汽车轻量化后仍能保持良好的防碰撞性能的问题, 而且成形后的零件具有基本无回弹、精度高、成形质量好等优点 。
目前热成型冲压件在车身的应用主要集中在A柱、B柱、C柱、门防撞板、前后防撞梁、中通道、纵梁、门槛、仪表板横梁等, 其中以B柱应用最为广泛 。
热成型首先是在加热炉中 将板料加热至再结晶温度以上(一般在900℃以上)一段时间 , 使其微观晶体组织由铁素体完全转化为奥氏体; 然后将完全奥氏体化的板料在几秒内迅速转移到成形设备中进行冲压成形,冲压成形后继续保压一段时间(15s左右 ) 使零件形状尺寸趋于稳定;在成形与保压过程中,为了提高材料的强度,利用模具(需布置冷却水道)与板料之间的温度差对板料淬火处理 , 使板料以超过27℃/s的速度冷却, 以获得在室温下具有均匀马氏体组织的超高强度钢。
(1)得到的是超高强度的车身零件,其屈服强度可达1000Mpa,抗拉强度1600-20Mpa ;
(2)其超高强度可带来零件厚度和重量的减小,满足车身轻量化的需求;
(3)具有良好的成形性,不易起皱和破裂,基本没有回弹,尺寸稳定性比较好 。
目前国内在用的热冲压用钢板主要由宝钢供货, 主要有两种类型:热轧BR1500HS和冷轧BH1500HS。其力学性能如表1所示。
B柱位于车身前门和后门之间,属于典型的汽车结构件。B柱作为车身中重要的承力构件,不仅要起到支撑车顶盖重量的作用,要保证在经受一定的撞击下车门仍然能够打开。
同时,作为前车门锁扣、后车门铰链以及前排安全带的安装部件,B柱还必须拥有足够的强度和刚度。目前整车所谓热成型“B柱”也即B柱加强板的热成型,B柱加强板总成一般由B柱加强板,B柱上、下部加强板,及车门铰链加强板组成,B柱内板总成由B柱内板和安全带固定点加强板组成。
B柱耐撞性能关键取决于B柱加强板、B柱上部加强板的断面尺寸、材料强度、材料厚度等因素,B柱内板作为车身最内侧板件,主要提供其他零部件的安装支撑功能,同时在加强板耐撞性能不足的情况下,可以起到弥补作用 。
现某纯电动轿车B柱原方案为普通高强钢,B柱本体材料采用B410LA,屈服强度在410Mpa左右,强度较低 ,于是在其内部上 、下各焊接一块尺寸较大的加强板,用以保证B柱强度,如图1所示。
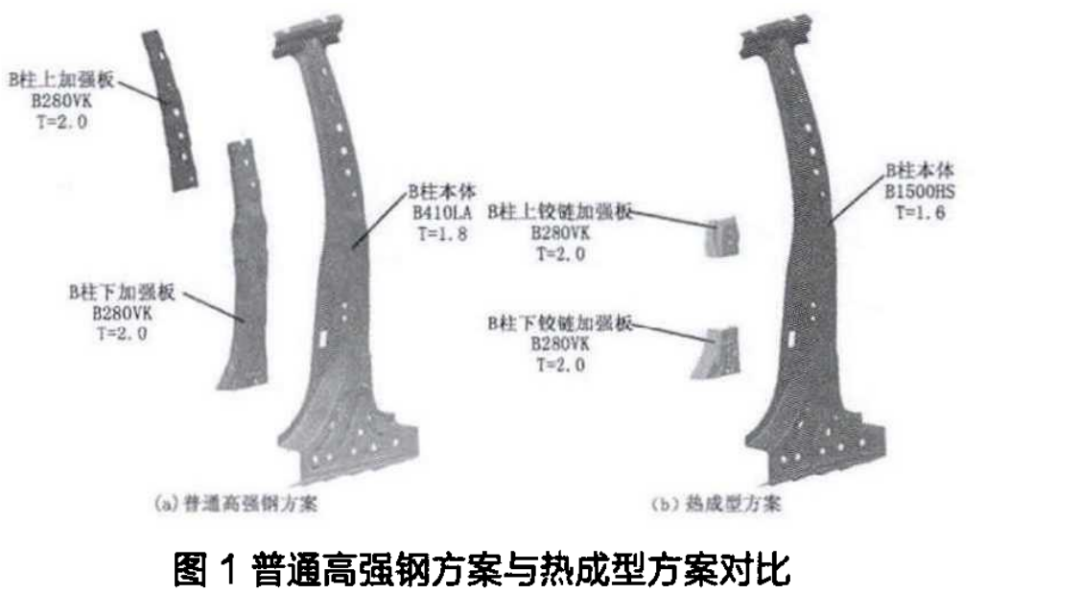
现热成型方案B柱本体材料采用B1500HS,并在上下铰链安装处增加两尺寸较小加强板,用于加强铰链安装处刚度以保证门安装刚度及防止门下垂。如图1(b)所示。
普通高强钢方案与热成型方案的B柱质量对比如表2所示。
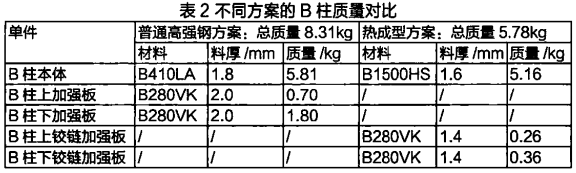
由表2可看出,热成型方案中B柱本体料厚减小,B柱内部上、下加强板尺寸及料厚均进行了缩减,采用热成型方案后单侧B柱减重2.53kg,两侧合计减重5.06kg,减重效果比较明显。
两种不同方案扭转工况下的白车身Z向变形图,如图2。
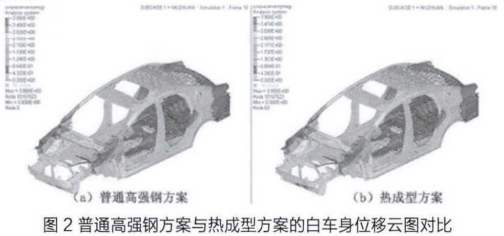
由图示数据可计算出两种方案的白车身扭转刚度,普通高强钢方案为9368.5 N·m/deg,热成型方案为93.2.3 N·m/deg,下降0.71%,略微下降,两方案基本持平。
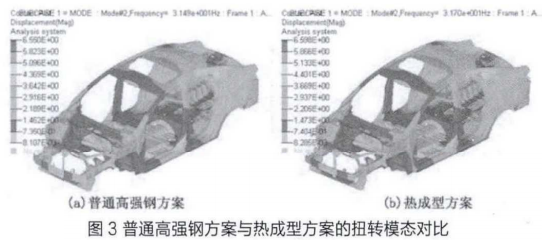
由图示数据可得出两种方案的白车身扭转模态,普通高强钢方案的一阶扭转模态为31.49Hz,热成型方案为31.70Hz,提高0.67%,略微提升,两方案基本持平。
对于侧碰而言,B柱显得尤其重要,特别是对于门槛较低的车,侧碰时门槛与壁障几乎没有重叠区域,门槛仅可以把少量撞击力通过座椅横粱传递到另外一侧,其余完全靠B柱承担载荷。
B柱的侵入量是定量评价侧面结构耐撞性的主要因素,侵入量越小越好。现对相同边界条件下两种方案侧碰过程中的B柱、前门、后门的侵入速度和侵入量进行仿真分析,其中B柱对应不同点的绝对侵入速度和相对侵入量,如表3所示。
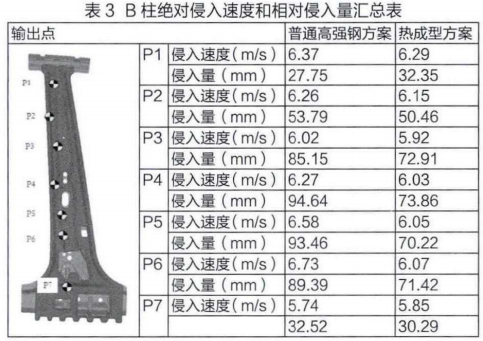
分析结果显示,热成型方案相对普通高强钢方案B柱对应不同点的侵入速度和侵入量均有不同程度的降低,满足要求。
文章来源:冲压与模具工艺