轴向柱塞泵作为液压系统的核心元件之一,具有工作压力高、功率密度大、噪声低、容积效率高、变量方便等特点而被广泛应用于中高压、大功率液压系统中。对于轴向变量柱塞泵而言,由于配油盘固定在后盖上,使得柱塞泵的容积效率只在某一工况下达到最优,其他工况均通过配油盘卸荷槽设计来包容,而传统的三角槽结构在重载小流量工况下由于容积效率低,容积效率带来的流量损失导致泵输出流量变化率非常大,使得主机执行机构速度与负载不匹配, 尤其出现负载大范围变动或晃动时,就会导致执行机构速度出现明显爬行现象,严重时甚至发生安全事故,因此改善轴向柱塞泵在重载小流量工况时的容积效率问题具有重要意义。
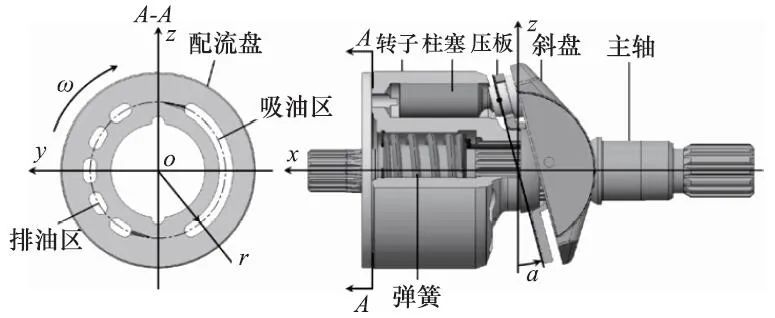
如图1所示,某型号轴向柱塞泵心脏部件主要由配油盘、转子、柱塞、滑履、压板、斜盘、主轴等零部件组成。当主轴带动转子转动时,转子与柱塞同步转动,由于斜盘存在偏角,柱塞在转子柱塞孔内作直线往复运动。在吸油区,柱塞在中心弹簧的作用下,不断伸出,柱塞腔容积不断增大,柱塞腔与配流盘的吸油窗沟通,吸入油液,直至上死点为止;在排油区,柱塞在斜盘表面的作用下,不断向柱塞腔内伸进,使柱塞腔容积不断减小,柱塞腔与配流盘的排油窗沟通,排出油液,直至下死点为止。缸体每旋转一周,柱塞完成一次吸油-排油动作,如此往复,便连续地吸油-排油,沿转子径向均布的多颗柱塞叠加后,便形成了连续的油液流动。
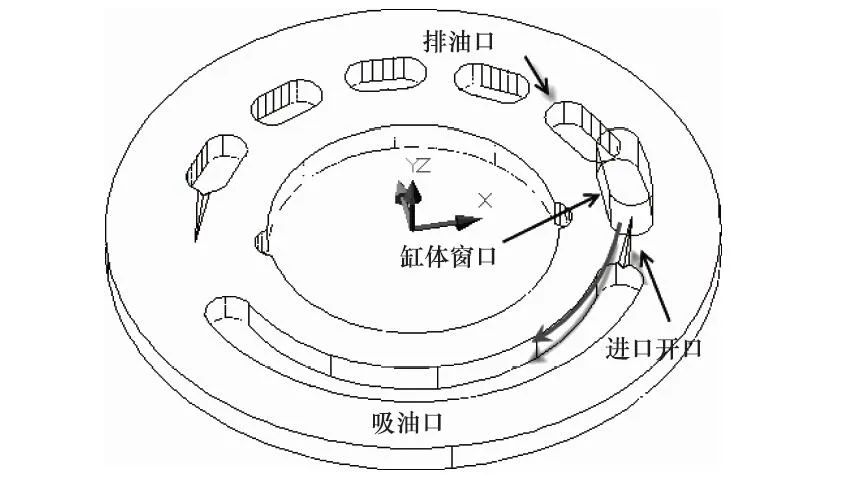
如图2所示,配流盘分为排油区、吸油区和过渡区,其中过渡区采用三角槽结构,且在三角槽尖端还存在着一个节流小孔。在配流盘过渡区,柱塞从上死点向下死点运动,在离开上死点时,柱塞腔与高压侧三角槽接通,高压油通过三角槽流入柱塞腔推动柱塞,使腔内压力逐渐上升,避免压力突变。同理,在低压区的三角槽沟通缸体柱塞腔,高压油接通低压区开始泄压,也可避免压力突变。
以柱塞从低压区向高压区转换为例,柱塞腔压力可按节流压差方程建立:
p
(
θ)
=
p
d
-
ρ/2(
q
/Cd
A
(
θ)
2)(1)
由式(1)可知,流通面积
A
(
θ)
随着转子窗口的转动而不断发生变化,相同结构下,压力越高,柱塞腔与出口腔压差也就越大,所产生的倒灌与回流现象就越严重,容积效率也就越低。
2.1 仿真模型搭建
为模拟轴向柱塞泵配流盘处的流量变化情况,根据某型轴向柱塞泵设计参数(见表1),建立如下AMESim单柱塞仿真模型:
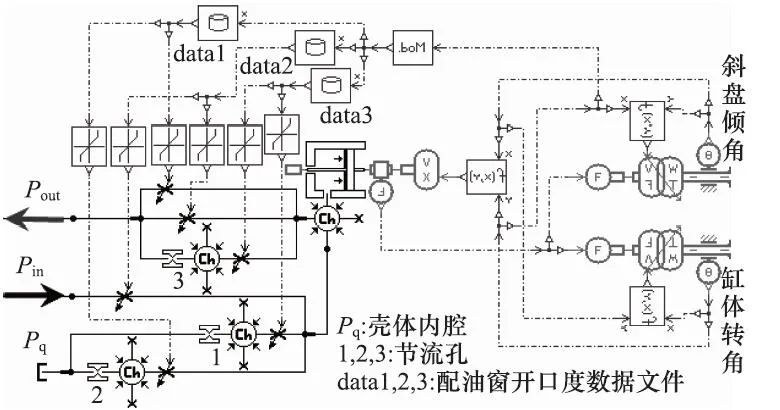
如图3所示,AMESim模型中采用等效节流孔的方法模拟转子与配流盘的过流面积,为探究不同卸荷槽结构对柱塞泵容积效率的影响,可变节流孔1、2、3分别受3个数据文件控制,代表着转子油窗经过配油盘各处油窗时接通进出油口的关系。
表1 某型号轴向柱塞泵主要参数
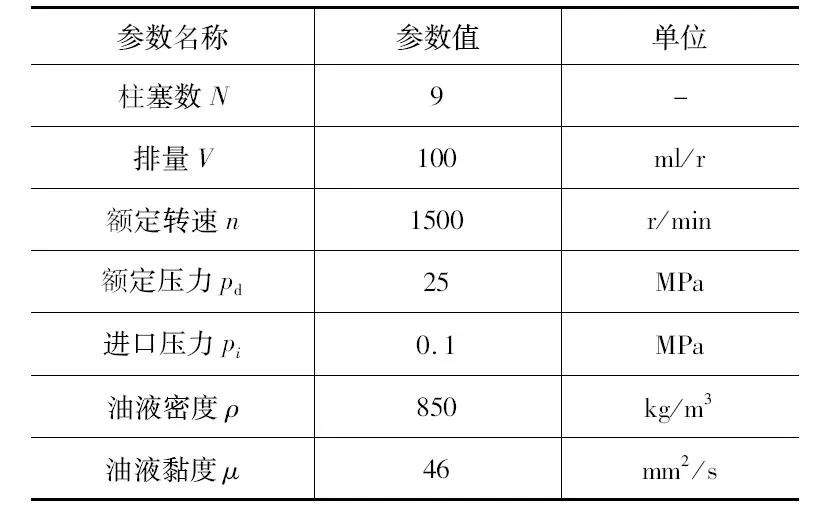
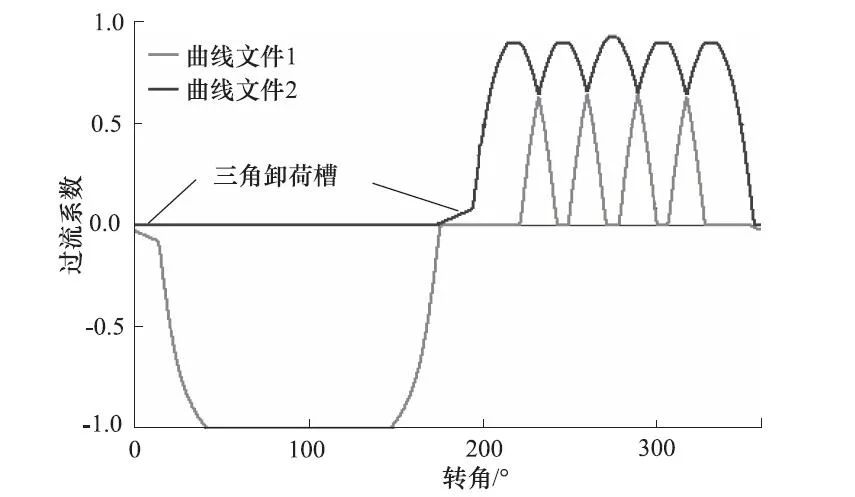
如图4所示,开度值-1表示缸体油窗完全进入吸油区,其通流水力直径为缸体油窗水力直径的1倍;开度值为0.9表示油窗完全进入排油区,由于配油盘加强筋的遮挡,其通流水力直径只能为0.9倍的缸体油窗水力直径值。
根据以上仿真模型,可以得到最大摆角下柱塞腔流量变化曲线:
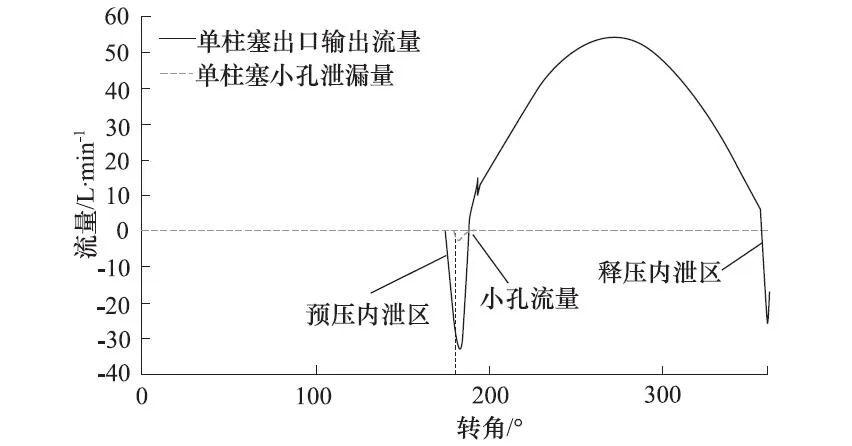
如图5所示,正值表示高压油输出至出口,负值表示出口油液倒流至柱塞腔内或低压进口(当柱塞腔内压力高于进口时则再泄至进口);180°和360°位置的三角槽因提前接通,在180°前有一段负流量区,说明高压油液在柱塞未经过下死点前就向吸油腔内灌油,导致出口高压油液在180°位置三角槽内泄至柱塞腔内,柱塞腔内高压油又经360°位置的三角槽泄漏至进口低压区;形成了出口高压接连通过180°和360°三角槽直接内泄至进口的原因,这也是其容积效率低根源,尖端节流小孔的作用是将出口高压油液注入到还未开始预压的柱塞腔内以辅助其内压力的建立,降低柱塞位移挤压油液时导致压力跃升过快,引起柱塞腔内压力超调。
将9个柱塞并联后即可得到泵出口流量变化曲线如下所示:
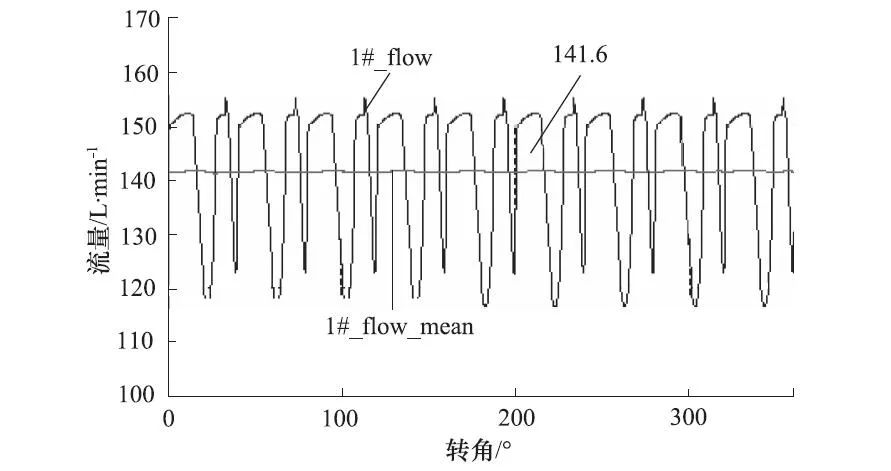
如图6所示,出口流量呈周期性变化,其变化幅值为转速与柱塞数的乘积;瞬时流量出现两次回落,分别由油液倒灌和内泄引起,其平均值为141.6 L/min,即不考虑外泄时,某型号轴向柱塞泵处于最大摆角时,其容积效率只有94.4%。
在原有仿真模型的基础上,通过调整相关结构,对配流盘卸荷槽进行优化设计,其结构如下所示:
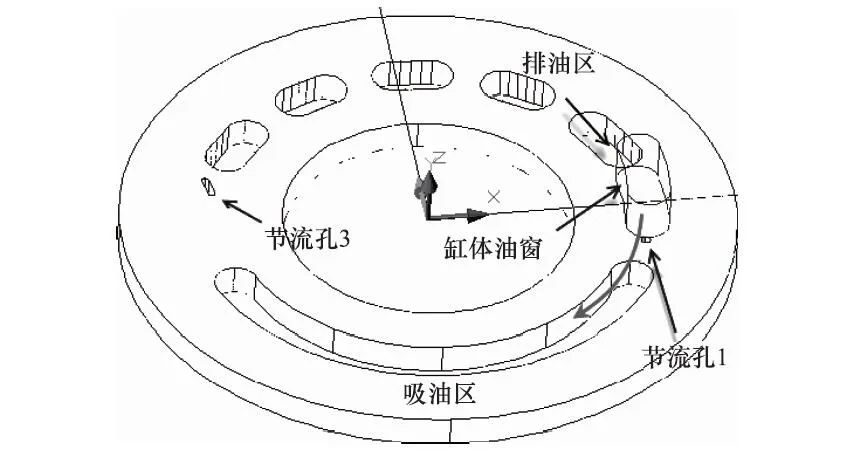
如图7所示,优化后的配流盘在过渡区采用不同直径的节流孔,以实现柱塞腔的预泄压与预升压过程,其中,节流孔1与壳体内腔沟通,节流孔3与出口腔沟通。优化后的配流盘过流面积与转角的关系如下:
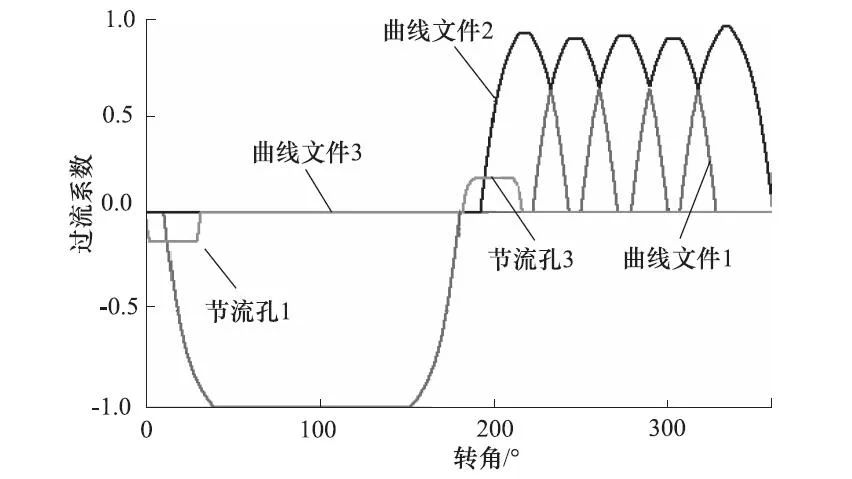
如图8所示,对于优化后的配流盘,在0°和180°两处位置,均不存在同时连通吸排油腔,且在180°至181.44°之间分离,完全不接通;这保证了柱塞腔内的压力油不能进入吸油区,对容积效率的损失主要集中在180°位置上,节流孔3连通泵出口和柱塞腔内时,高压油液倒灌入建压较低的柱塞腔内。而在0°位置时,柱塞已回到上死点,不能对外排油,故节流孔1不能引起高压油向吸油口的灌油,仅仅是柱塞腔内残留压力的释放孔。

如图9所示,对于优化后的配油盘,节流孔3的作用与优化前的配油盘三角槽尖端的节流孔作用相同,但其开启角度在180°之后,故出口高压油注入到柱塞腔内的压力油液并不能在预压区进入吸油区;在360°时柱塞输出流量无损失,这与优化前的配油盘不同;整个过程中出口高压油虽然回灌至柱塞腔内,但无压力油泄漏至进口吸油区。因此,在此特定工况点上除满足油液的体积压缩损失外,油液基本没有因配油盘的配油功能而产生损失。流经节流孔1的总流量在360°(或0°)位置之后出现负流量,表明过上死点后柱塞腔内压力油通过向壳体内腔进行压力释放来降压,并迅速进入吸油状态(流量为正值)。
由于节流孔1是接通壳体内腔的,所以节流孔1的作用是在柱塞进入上死点后,将储存的高压油液经过该节流孔1进行压力释放,在释放完毕后,当柱塞腔内进口压力较低时则通过该节流孔1吸入壳体内腔内的油液以防吸空。
当斜盘处于最大摆角时,优化后的泵出口流量变化曲线如下:
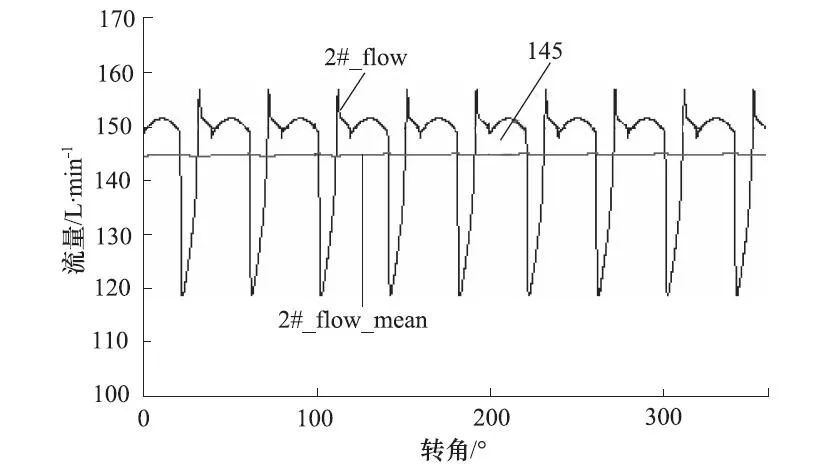
如图10所示,优化后的配流盘结构在消除了内泄所引起的流量回落的同时还减小了油液倒灌所引起的流量回落,使得优化后的柱塞泵输出的平均流量约为145L/min,容积效率约96.7%,比原有结构提高了2.3%左右。
以改进前的配流盘为1#配流盘,改进后的配流盘为2#配流盘,则不同摆角下1#与2#配流盘的容积效率如下:
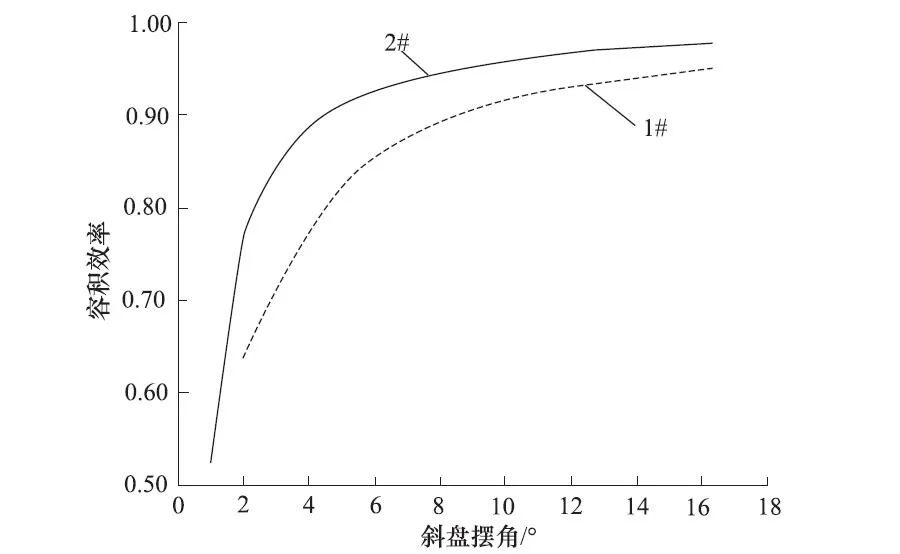
如图11所示,在不同摆角下,优化后的2#配流盘均比改进前1#配流盘的容积效率高,且在斜盘摆角处于小角度时,容积效率的提升效果更明显。
为验证仿真结果的正确性,对某型轴向柱塞泵进行容积效率试验。为了避免控制阀对斜盘控制角度因压力跃升引起的控制角度偏差,保证泵本身容积效率试验的有效性,通过大小排量的机械限位螺钉来抵死斜盘,避免斜盘角度在测试中的变化,机械限位示意图如下:
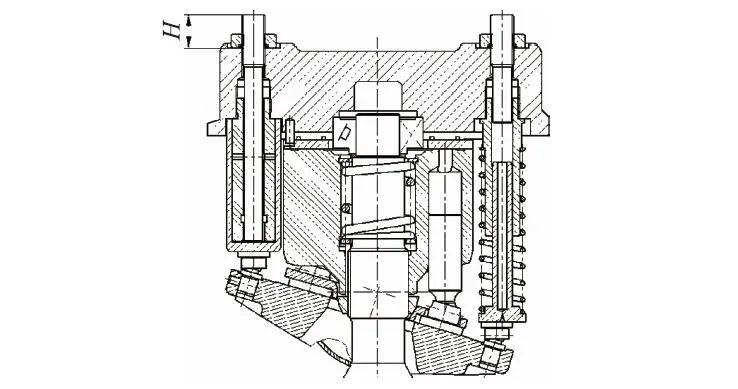
如图12所示,每次斜盘角度的调整均通过调节限位螺钉至指定的H值,根据H值可获得对应的斜盘角度,这样就能通过一系列的值得到整个斜盘倾角变化时配油盘的容积效率曲线。
由于内泄所导致的容积效率损失不能通过回油量来体现,故在试验时采用空载流量与加载流量的比值来计算容积效率,试验中主机转速为1500r/min,加载时出口压力为25MPa,则不同摆角下1#配流盘与2#配流盘的容积效率实验数据如下:
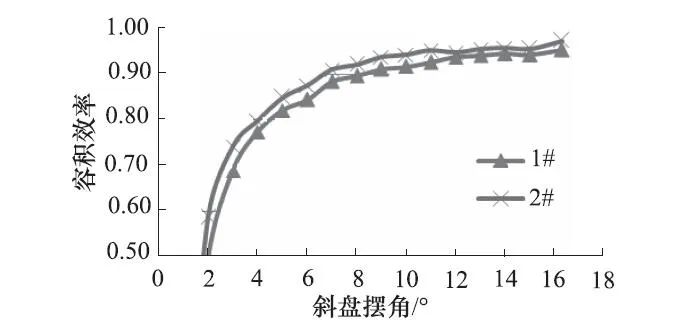
如图13所示,不同摆角下,改进后的2#配流盘容积效率均比1#配流盘高,其容积效率高出1#配流盘2.2%~10.5%,且摆角越小提升效果越明显,试验结果与仿真曲线基本吻合。
本文针对某型号轴向柱塞泵在重载小流量工况下容积效率低的问题,运用AMESim软件搭建轴向柱塞泵配流副原理模型并对配流盘卸荷槽进行优化设计,最后通过试验验证了优化设计的有效性,主要结论如下:
(1)原结构的配流盘卸荷槽由于存在油液内泄和倒灌,使得其容积效率较低;
(2)优化后的配流盘卸荷槽结构在消除油液内泄所引起的流量回落的同时还减小了油液倒灌所引起的流量回落,从而提高轴向柱塞泵的容积效率;
(3)出口压力为25MPa,不同摆角下,改进后的2#配流盘容积效率均比1#配流盘高,其容积效率高出1#配流盘2.2%~10.5%,且摆角越小提升效果越明显。
参考文献
[1]
李玉琳.液压元件与系统[M].北京:北京航空航天大学出版社,1991.
[2] 雷天觉.新编液压工程手册[M].北京:机械工业出版社,1990.
[3] 刘雨,张兴越,王晋芝.基于AMESim的柱塞泵LR控制特性研究[J].液压气动与密封,2020,(4):32-35.
[4] 杨智炜,徐兵,张斌.基于虚拟样机技术的轴向柱塞泵特性仿真[J].液压气动与密封,2006,(3): 33-36.
[5] 宋月超.柱塞泵流量脉动测试方法和大范围工况降噪结构优化的研究[D].杭州:浙江大学,2013.
[6] 甘海.轴向柱塞泵配流副流场仿真及三角减振槽参数特性分析[D].哈尔滨:哈尔滨工业大学,2014.
[7] 王晋芝,刘雨,杨华,等.液压操作手柄控制系统优化设计[J].液压气动与密封,2020,(11):51-55.
[8] 那成烈.三角槽节流口面积的计算[J].甘肃工业大学学报,1993,19(2):45-48.