摘要:由于动力总成的不同,电动车与传统车的振动噪声源也有较大差异。笔者对某电动车动力总成的振动噪声特性进行了试验研究。利用频谱分析、阶次分析等方法来识别动力总成的主要振动噪声源,分析加速和稳态工况下各激励源对动力总成振动噪声的贡献量。基于心理声学客观评价参数,分析了电动车动力总成声品质特性。研究结果为电动车动力总成振动噪声的优化设计提供了试验支持,并表明了进一步研究电动车声品质的必要性。
引言
声品质对整车质量认知度有很大影响,统计表明汽车的事态发展错误中有三分之一是与噪声、振动及舒适性(
noise,vibration and harshness,简称NVH
)有关,每年噪声相关方面的保修费用占据整车的20%左右。
传统车动力总成振动噪声特性的研究已有很多。胡国强等通过对柴油机进行燃烧噪声分析和噪声源识别,采取怠速噪声降噪措施,并对优化前后的结果进行声品质比较。卢丰翥等对柴油机进行怠速声品质试验研究发现,并不是噪声值越小声品质就越好。相龙洋等对手动变速器噪声源识别进行了试验研究。但是,对于电动车来说,内燃机被电机所取代使得动力总成振动噪声源发生很大变化。一方面,电机电磁激励会产生高频噪声;另一方面,由于人的双耳的构造以及掩蔽效应的存在,发动机的缺失会使电动车其他部件的噪声变得更为显著,很多情况下更为刺耳与令人不适(如逆变器噪声、齿轮传动系噪声)。
近些年,随着世界各国大力推广新能源汽车,国内外学者也开始研究电动车的振动噪声特性。严刚等对某纯电动汽车车内噪声试验研究,识别了不同工况下的噪声源。Islam等研究并分析了永磁同步电机的噪声和振动。研究表明,噪音和振动的根源是径向力引起的电磁振动。大多学者以噪声级为标准研究其噪声特性,并进行降噪的优化设计。但是,基于噪声级的研究存在局限性,顾客评价一辆车的好坏并不以噪声级水平为评价指标,而是以驾驶过程中的主观感受进行评价。因而,基于能够反映人的主观感受的心理声学客观评价参数
对电动车进行声品质的研究就尤为必要。
笔者以某集中驱动式电动车动力总成为研究对象,对其进行振动噪声整车试验研究,得到了箱体表面的振动噪声情况,确定了动力总成振动噪声的主要激励源。以几个典型的声理学客观评价参数为评价指标,对电动车动力总成声品质特性进行初探。
1 动力总成振动噪声测试
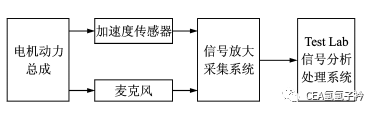
图1 振动噪声信号测试系统
考虑到试验现场整车运行的特点,为了较准确测量电动车动力总成的噪声,最大限度削弱其他噪声信号的影响,噪声测量时采用近声场测量方法,将麦克风置于与电机动力总成噪声源较近的测点测量声压;然后,再通过LMS SCADAS
Ⅲ
316W接口箱将信号输入PC机,由LMS Test Lab软件完成信号记录。
LMS Test Lab是一整套的振动噪声试验解决方案,是高速多通道数据采集与试验、分析、电子报告工具的结合,包括数据采集、数字信号处理、结构试验、旋转机械分析、声学和环境试验。
1.1 试验装置与测量仪器
本试验针对某集中驱动式纯电动车动力总成进行振动噪声测试。试验在半消声室内进行(图2)。3个声压传感器分别布置在电机端部、减速器处、差速器处3个位置,4个三向加速度传感器贴在动力总成表面不同位置。试验装置及传感器测点布置如图3所示。
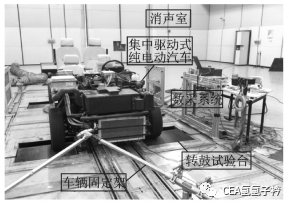
图2 试验现场
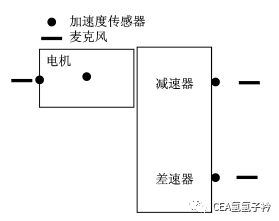
图3 传感器布置
1.2 试验过程
本次试验模拟了车辆的典型工况。为了能够测试动力总成的整体噪声水平并系统分析其振动噪声特性,进行了两种不同的试验:a.稳态试验,分别测试了电动车在不同转速下的振动噪声水平;b.瞬态
试验,分别测试了车速从0~80km/h匀加速过程中的振动噪声水平随转速变化过程。
2 试验数据分析
2.1 匀速工况
2.1.1 动力总成振动测试结果分析
图4为车速50km/h、电机转矩为12N·m时,动力总成箱体表面加速度频域图。从图中观测到边频谱现象,即某些阶次响应频率两侧存在数值相近的较为密集的频率成分,这说明该阶次频率在时域上较为集中分布在一定的区间范围内。
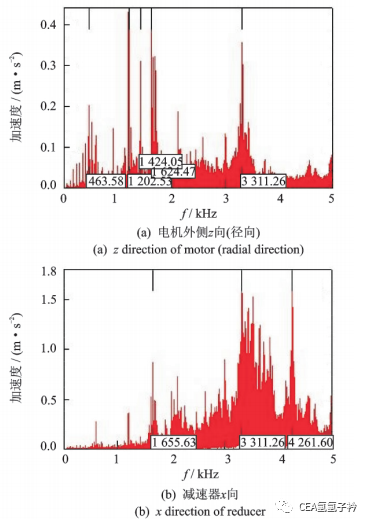
图4 动力总成表面振动加速度频谱图
图4(a)表示电机壳体外侧振动情况,从图中可以看出振动加速度在1200,1420,1650Hz等频率处存在峰值,分别对应电机6,7,8倍电流频率。图4(b)中,减速器轴承座处在3300和4260Hz附近有明显峰值,分别对应输入级齿轮啮合频率的2倍频和3倍频。值得注意,在3300Hz处,整个动力总成表面振动明显,因此可能与系统某一阶模态有关。综上分析,动力总成的动响应受到电磁激励、齿轮动态啮合力等多源激励以及系统固有特性的综合作用。
2.1.2 动力总成噪声测试结果分析
研究匀速行驶工况下车内噪声特点和识别主要噪声源对优化整车NVH性能有重要作用。测试10~80km/h时动力总成噪声水平,如图5所示。
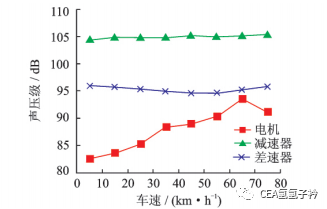
从图5中可以看出,减速器轴承座处声压水平明显较高,随着车速的增加,减速器和差速器轴承座处的声压级基本不变;相反,电机端部的声压级波动较大。在试验过程中,随着车速的提高,高频噪声增大,尽管电机的噪声级水平不高,但是由于波动较大,会使人感到烦躁。因此,研究匀速行驶工况下车内噪声特点和识别主要噪声源对优化整车NVH性能有重要作用。
试验发现车速以50,60,70km/h匀速行驶时,动力总成表面3个测量点噪声分布规律相似。其中减速器轴承座处测量点噪声最大。电动车匀速行驶时减速器测量点噪声特点如图6所示。由图可知,减速器处噪声能量主要分布在1600~3500r/min。不同车速下,在480与944Hz处均存在由控制器引起的峰值噪声。图6(a)中出现较多峰值,其中1203,1698,3323,4082Hz分别为电机6倍、8倍、16倍和20倍的电流频率,这些峰值都有频率窄,峰值高的特点,因此对噪声影响贡献量较大;1540,2985,4209Hz分别是输入级齿轮啮合频率的1,2,3倍频。如果能采取相应的措施,将这些峰值降低,动力总成噪声将得到大幅的改善。图6(b)中,车速为60km/h时,减速器轴承座处有几个明显的峰值。其中:1097,2057和2563Hz分别为电机4倍、8倍和10倍的电流频率;4018Hz为齿轮啮合频率的2倍频。图6(c)中,在70km/h时,1181Hz对应电机4倍电流频率。2437Hz既对应电机的8倍电流频率,又对应输出级齿轮啮合频率的3倍频,因此具有较大峰值;4462Hz对应输入级齿轮啮合频率2倍频,4863Hz对应输出级齿轮啮合频率6倍频。
2.2 急加速工况
2.2.1 阶次跟踪分析
旋转运动机械的升降速过程的振动噪声信号为非平稳信号,不满足傅里叶变换对信号的平稳性要求,若直接用传统傅里叶变换进行频谱分析,则会产生“频率模糊”现象。阶次跟踪是用于分析旋转运动部件故障的重要方法,用等角度间隔采样将非平稳信号转化为不受其影响的平稳信号,结合传统频谱分析对系统进行振动和噪声信号的分析。
研究旋转部件时,定义参考轴转频为基频(1阶),其他轴或部件频率为参考轴频率的倍数,称为阶次。阶次与频率、参考轴转速间转化公式分别为

表1 齿轮参数
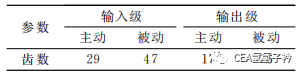
电机转轴为参考轴,其转动阶次为Oref=1ord。因此输入级齿轮啮合阶次为Og1=29ord。中间轴转动阶次为参考轴阶次乘以传动比,即Oa1=1×29/47=0.62ord;输出级齿轮啮合阶次为Og2=0.62×17=10.54ord。
对于整数槽绕组永磁同步电动机产生的电磁激振力的阶次可以表示为

其中:p为电机极对数,k=1,2,3,…。
2.2.2 动力总成振动测试结果分析
在图7(a)电机外侧径向振动阶次图中,第20,24,28阶均与电磁激励有关,电流谐波引起15阶和38阶,齿轮啮合激励引起第55阶和57阶;图7(b)减速器轴承座处y向振动阶次图中,第55,57阶与齿轮啮合频率有关,而第28阶则与电磁激励有关。
因此,电磁激励与齿轮啮合激励对动力总成振动特性均有影响。
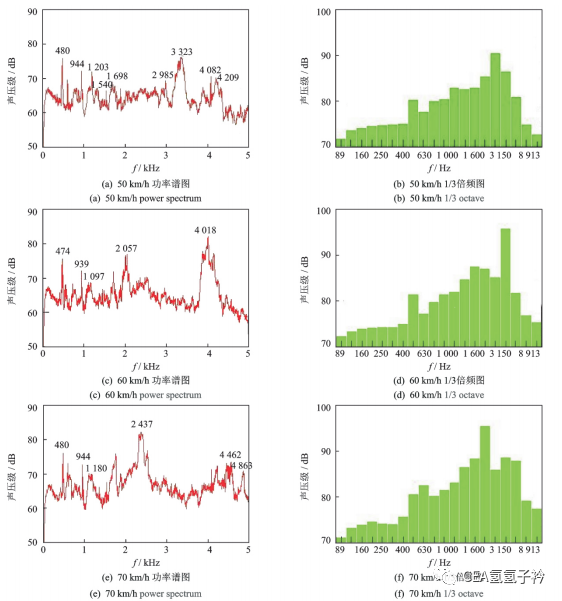
图6 减速器表面噪声特点
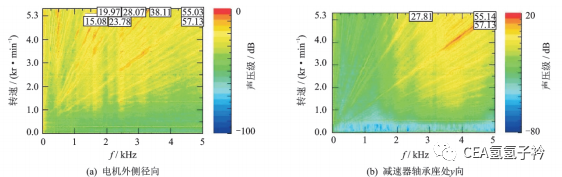
图7 动力总成表面振动阶次图
2.2.3 动力总成噪声测试结果分析
图8为电机端部声压阶次图,结合图7(a)可以看出,部分振动阶次在声场中也得到体现:既有电磁激励产生的第20,28阶次,也有齿轮啮合激励产生的55阶次。
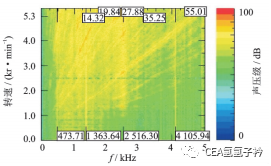
图8 电机端部噪声阶次图
图9中最上方粗线为总体噪声级水平,其他各曲线为各特征阶次对应的噪声分量。由图9可知,在低转速920r/min以下,55阶次对系统总体噪声的贡献很大。在中等转速2000~3000r/min时,各阶噪声对总体噪声水平的贡献相差不大。在高转
速3300~5000r/min时,第20阶对总体噪声的贡
献较大。
由此可以看出,电机端部的噪声主要是由电磁激励引起的。
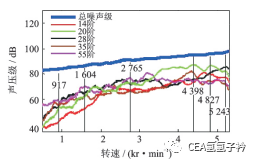
由图9看出,20阶和35阶在4389r/min出现峰值,此转速分别对应图中1363和2516Hz。28阶在5243r/min出现峰值,此转速对应图中的频率2516Hz。55阶在1604r/min和2765r/min出现峰值,此两转速分别对应图中的频率1363和2516Hz。从图中可以看出,1363Hz和2516Hz对应的振动加速度幅值在整个转速范围内都较高,因此,这两个频率应为动力总成系统的某两阶模态
频率。
图10为减速器轴承座处的噪声阶次图,结合图7(b)可以看出,部分振动阶次在声场中也得到体现:既有电磁激励产生的第20阶次,也有齿轮啮合激励产生的55和57阶次,还有二者共同作用产生
的28阶
次。
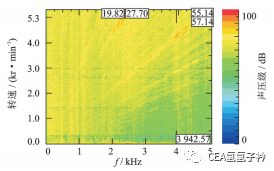
图10 减速器轴承座处声压阶次图
图11中最上方粗线为总体噪声级水平。其他各曲线为各特征阶次对应的噪声分量。由该图可知,在高转速1387~2034r/min时,第20和28阶对总体噪声的贡献较大。在转速2034~4300r/min时,第55和57阶噪声对总体噪声水平的贡献较大。在转速5000r/min以上时,第20和28阶是总体噪声的主要贡献。
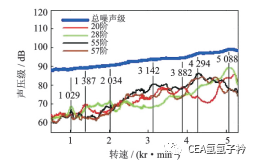
图11 减速器噪声阶次转速跟踪图
由图11可以看出,55阶在4294r/min处出现峰值,此转速分别对应图中3943Hz。28阶在5088r/min出现峰值,此转速从图9中也可以反映出来。值得注意的是,在3800r/min以上,尽管第20和28阶次对系统总噪声级贡献并不明显,但是由于其波动较大,使人感到烦躁。因此,在以噪声级水平为目标值进行NVH研究并不完全适用。
3 声品质
汽车作为商品最终是面向市场的,顾客对汽车的主观感受是决定一辆车好坏的最终标准。发动机的掩蔽效应缺失,电机的高频噪声,高转速带来的齿轮啸叫问题,汽车品牌音质以及人们对电动车舒适环境的高期望值,给电动车NVH的研究带来了新的挑战。仅仅以声压级作为NVH的衡量标准不再满足汽车的发展要求,尽管某些工况下电动车的总体噪声水平低于传统车,但是,听起来会很不舒服。因此,心理声学就应运而生,心理声学是研究听觉的心理反应。
由于人的主观感受没有统一标准,不易测量。因此,国际上许多专家学者提出用心理声学客观参数来反映人的主观感受。响度、尖锐度是影响声品质偏好型的两个主要心理声学参数。其中,响度是反映人耳对声音强弱的主观感受程度,它考虑了特征频带分布和人耳掩蔽效应对声音的影响。尖锐度描述了高频成分在声音频谱中所占的比例,它反映了声音信号的刺耳程度。
图12为动力总成表面的响度情况,从图中可以看出3个测量点的趋势基本一致,随着车速的升高,响度逐渐增大,人耳也感觉声音越来越响。图13为动力总成表面尖锐度情况,从图中可知,动力总成表
面的尖锐度分部极不均匀。
电机端部尖锐度随着车速升高先快速下降再缓慢升高;
减速器处尖锐度整体趋势则先随转速升高而缓慢下降再快速升高,并在转速为4300r/min(车速65km/h)左右时出现峰值,随后又有所下降;
减速器处尖锐度随着转速升高先快速下降随后逐渐升高;
3个测量点的尖锐度均在转速为1700r/min(车速26km/h)左右时有最小值并相差不大。
由此可知,此时动力总成表面尖锐度分布最均匀,而且人耳感觉最不刺耳。
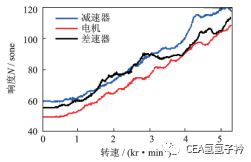
图12 响度
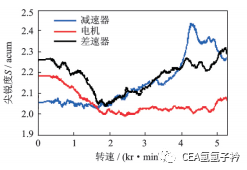
图13 尖锐度
4 结论
1)综合利用频谱分析、阶次分析等方法来识别动力总成的主要振动噪声源。电机电磁激励产生的电流倍频和减速器齿轮的1,2,3倍啮合频率对系统的振动噪声影响较大。
2)试验发现,尽管电机端的总体噪声水平较减速器与差速器低,但是波动较大,听起来感到不舒服。这说明声音的烦躁度与声压级没有关系,而是与声压级的变化率有关。
3)以心理声学客观评价参数为标准,对动力总成声品质特性进行了初步研究。研究发现,动力总成表面响度分布较一致;尖锐度分布不均匀,车速为26km/h时,有最小值。
文章来源:CEA氢氢子衿