夯实模具标准化基础,迈向智能化高效设计
夯实模具标准化基础,迈向智能化高效设计
■青岛维特信息科技有限公司 / 张祥富 经理
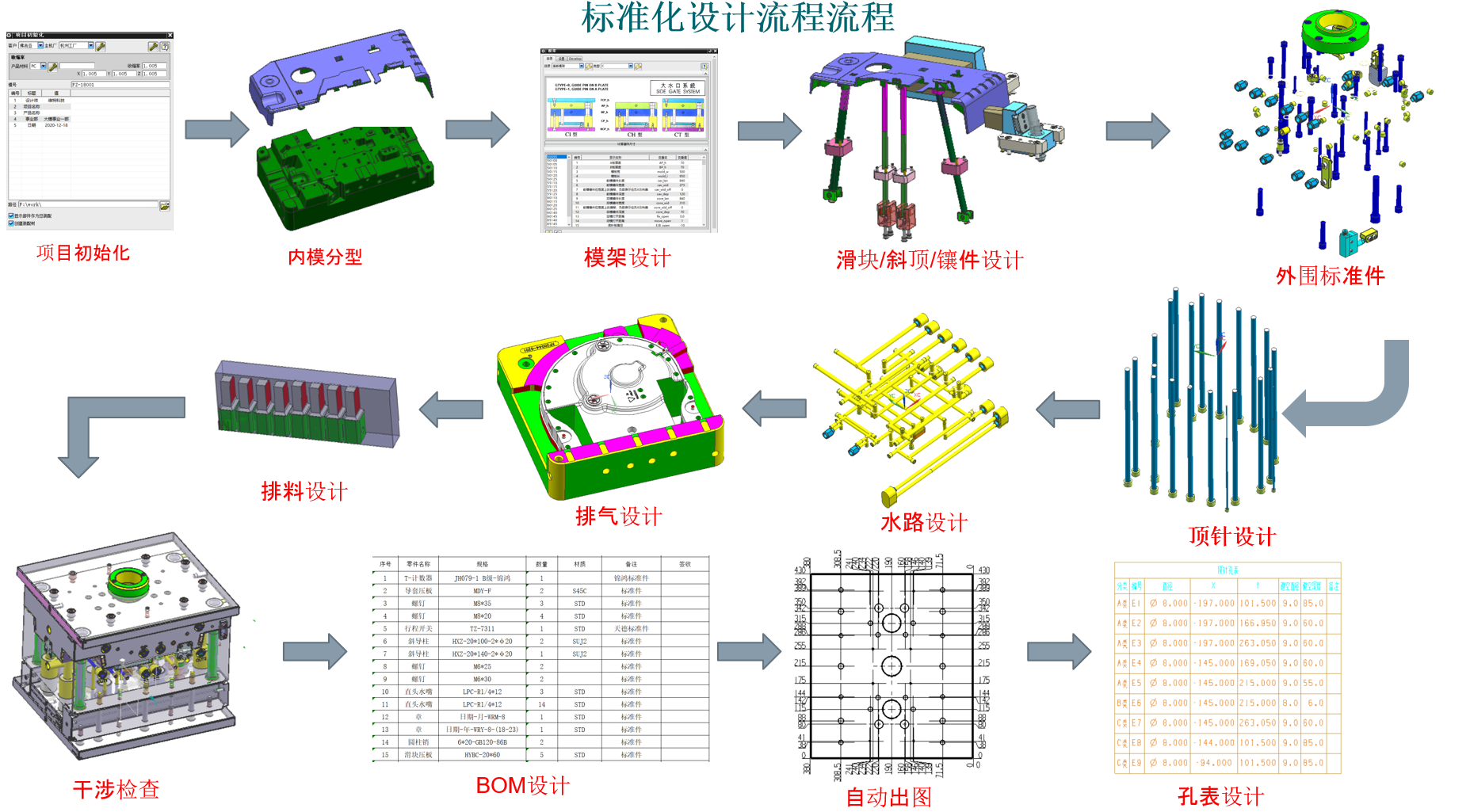
前言
模具设计是模具整个制造过程的源头,模具设计决定了模具制造的效率、质量、成本、加工工艺,同时也决定了射出生产的稳定性、效率和成本。所以模具设计非常关键,是模塑制造的核心技术,需要系统性规划,为后续智能制造做好基础。
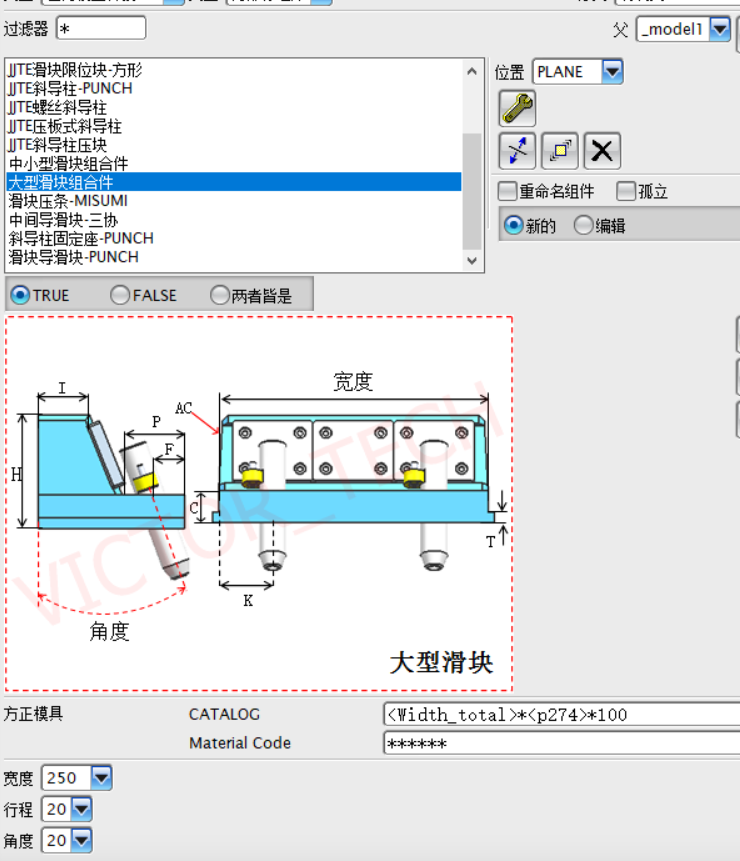
图1:3D 标准化设计平台,将已制定标准建立3D 库平台,实现标准统一
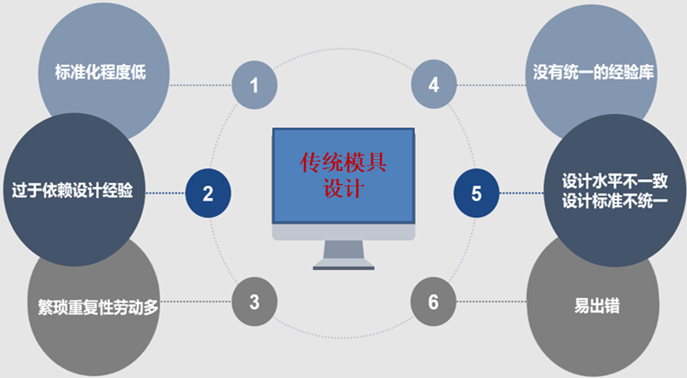
图2:模具设计面临的瓶颈
为了提升模具设计的效率、准确性、降低设计失误、降低模具设计对人员技术的要求,企业应当重点加强:
模具企业设计标准化和智能化设计理念,培训、辅导落地、执行;
梳理标准化体系包括:标准化零件、设计规范标准化、作业模式标准化;
将企业标准化技术通过系统软件的方式固化,人人按标准设计,保证标准化执行落地;
通过智能系统完成企业技术的积累和沉淀,避免人员流动造成对企业技术能力的影响;
通过建立大量的标准库、标准模块并开发大量的快捷集成设计方式,大幅提升设计效率;
通过智能化设计系统完成大部分重复和繁琐的工作,解放设计师将主要精力用在模具和核心技术上如:分型、结构合理性、工艺优化等与产品相关的技术。
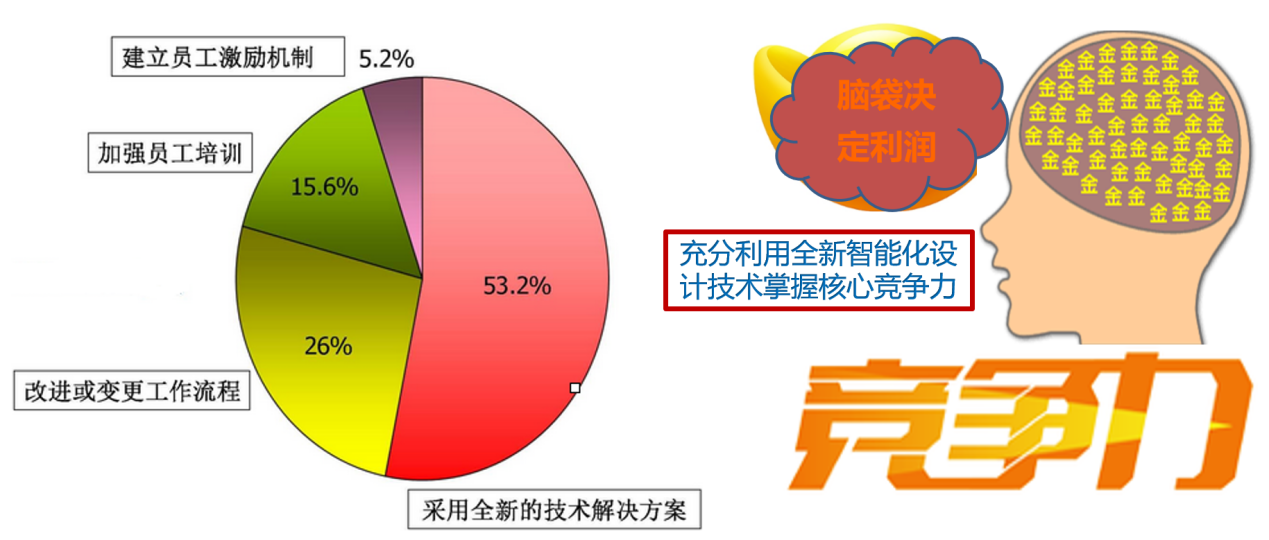
图3:如何保持模具企业的核心竞争力──创新
模具企业竞争激烈,交期、成本、质量压力大,传统模具设计已经不能满足市场需要,需要全面系统性变革,利用先进软件技术执行标准化并融入丰富的专家经验变革模具设计模式:
平台化智能设计,协同设计。
建立标准化专家技术库、知识库、标准化设计,降低设计人员技术要求。
系统规划标准化零件库、结构设计模块化,提升标准执行统一性和准确性。
通过标准快捷设计系统,大量减少工程师繁琐、重复性的操作,释放设计师时间和精力,专注于产品成型及核心技术工艺。
标准化整体优势
设计前期零件标准化的完善,采购成本降低,设计效率提升,模具周期缩短,不断增强企业整体竞争力。同时设计标准化后,编程和制造部门也可以进行相应的加工标准化,实现更加高效统一的生成节拍。
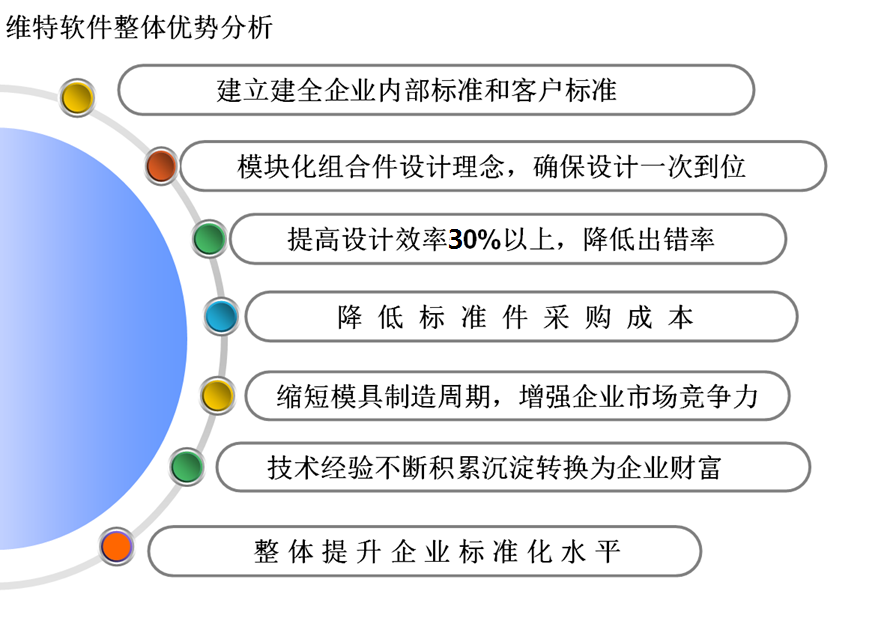
图4:标准化整体优
模具行业标准化发展趋势
随着模具行业信息化、数据化、自动化、智能化、工业互联网的发展模具设计向智能化转型升级是必然趋势。模具设计是模具制造的源头,标准化、数据化、协同化、智能化模具设计必须要系统性规划。
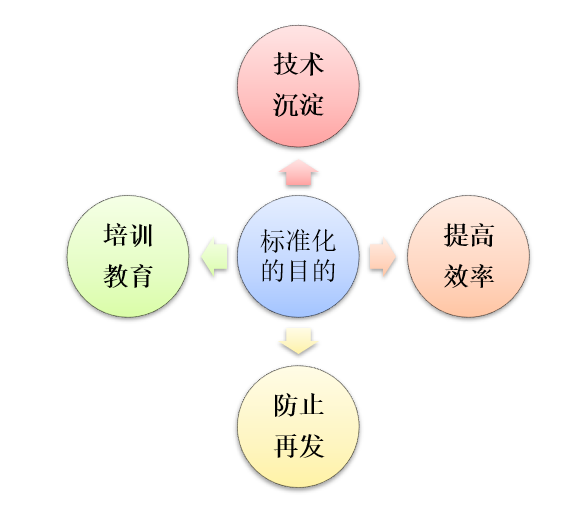
图5:标准化的目的在于提高效率、技术沉淀、培训教育,以及防止再发
标准化也是企业管理和技术沉淀的最好方式,模具行业的转型升级设计是关键,是模具智能制造的源头。标准化无疑是模具制造过程中推动信息化和自动化的源头,一步跨不到信息化、自动化、智能化,很重要的基础就是前端的标准化,决定了能否顺利推动模具企业整体信息化、自动化、智能化成功的关键。
模具企业标准化搭建包括
管理流程、作业标准、工艺标准、技术标准、零件标准、公差标准、模块化、设计标准化等。
标准化的积累也是后续进行模具自动化技术和管理的基础工作,积累到一定程度就很容易实现自动化和系统化升级。
一流企业永远是在做标准,能成为行业标准的制定者,一定是行业的引领者。优秀的模具企业都非常重视内部标准化体系建设。
标准化、信息化、自动化、智能化是行业发展方向和趋势,而标准化是关键基础,作为所有数据输出的源头,设计标准化的程度提升会大大缩短设计周期、降低采购成本,同时也可以带动后续加工部门的标准化程度。
模具行业竞争越来越激烈,如何确保短周期、低成本,通过搭建起企业标准化设计平台,实现信息技术与生产管理高度融合,能够显著增强模具企业研发的设计能力进而缩短研发周期,降低研发成本,降低设计准入门坎;同时也是企业对外实力展示的一个窗口,可以站在更高的平台与同行竞争,确保自身优势。
模具企业标准化带来的好处
智能模具设计的源头标准化,是后续加工工艺、编程、加工等标准化的基础;
让模具开发和制造有序进行;
谁做都一样,降低人为因素影响;
模具开发效率提升,模具质量稳定有保障;
模具成本降低。
模具企业标准化的未来
运用技术将标准固化;
利用大数据分析标准化,降低经验的影响;
共享标准化,从而形成行业标准;
标准化会同精益制造相结合,大数据分析将充分发挥作用,让标准更准。
应用案例
案例一:自动滑块设计
设计人员把滑块头部设计完成后,后端自动匹配成组生成,组合标准件(耐磨板、压条、斜导柱、导滑)全部匹配到公司标准,确保所有设计人员对于标准执行的统一,整个滑块生成不到1分钟,在标准化基础上极大提升了设计自动化效率。
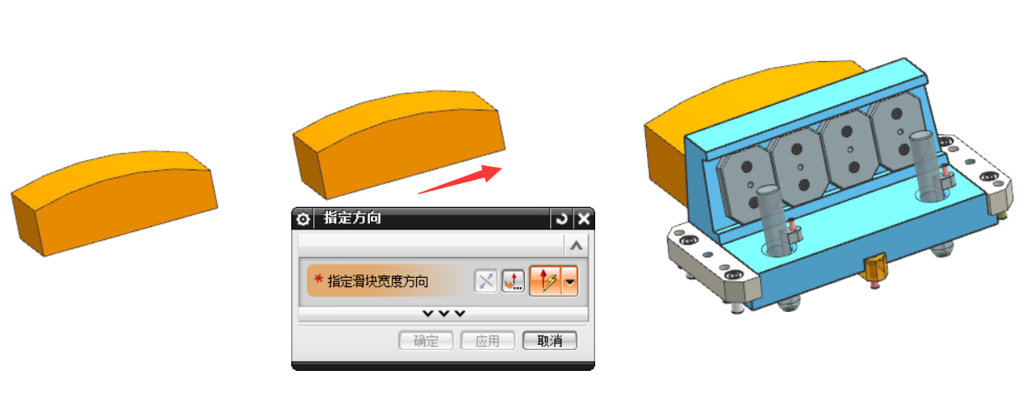
图6:应用案例──自动滑块设计
案例二:自动斜顶设计
设计人员把斜顶头部设计完成后,后端自动匹配成组生成,自动定位匹配到模架对应位置上,组合标准件(滑座、导滑块)全部匹配到公司标准,包括假体符合要求,确保所有设计人员对于标准执行的统一,实现批量操作,批量生成,在标准化基础上极大提升了设计自动化效率。■
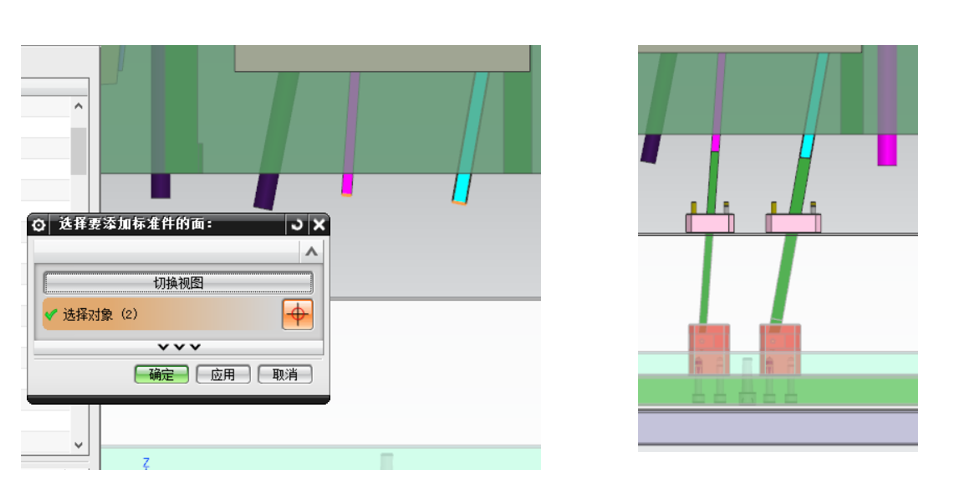
图7:应用案例──自动斜顶设计
未经同意,请勿转载