[摘要]汽轮机作为火力发电系统中的核心设备,其经济性直接关系到整个发电系统的效能;火电行业发展新的趋势对于深度提升和长期保持汽轮机效率提出了新的要求。东汽积极推进汽轮机性能的提升工作,自主研发的第三代、第四代先进通流技术已经在300~1 000MW机组通流改造项目上得到成功验证;同时,在减小机组性能老化方面,东汽也采用了一系列先进的保效技术,取得了卓有成效的应用效果。
陈显辉1,孙 涛2,万忠海3,饶真炎1,刘 昊1
1.东方电气集团东方汽轮机有限公司;
2.国家电投集团江西电力有限公司;
3.国网江西省电力有限公司电力科学研究院
0 引言
伴随着我国经济社会的高速发展和国家节能减排政策的深入推进,提高燃煤发电机组的经济性一直是火力发电行业高质量健康发展的热点和主线[1-3]。当前,在“碳中和,碳达峰”的能源新形势下,大容量火电机组逐渐发展成为承担调峰任务的主体,电站汽轮机快速起动和深度调峰日渐成为常态[4-6]。汽轮机作为火力发电系统中的核心设备,其经济性直接关系到整个发电系统的效能[7];火电行业发展新的趋势对汽轮机的高效运行提出了新的要求——从关注机组高负荷的经济性到更加关注机组部分负荷的经济性,从关注机组新机投产时的经济性到更加关注机组全生命周期运行中的经济性。深度提升和长期保持汽轮机运行经济性对于改善电站发电效益,降低检修运维成本具有积极意义[8-11]。
汽轮机热耗随运行年数的增长而增加,被称为性能劣化,也称为性能老化。汽轮机性能老化具有热耗逐年递增,增加的幅度逐年减小的特点;而减小汽轮机热耗增加速率的措施称为机组保效技术。东汽积极推进汽轮机性能的提升工作,自主研发的第三代、第四代先进通流技术已经在300~1000MW机组通流改造项目上得到成功验证;同时,在减小机组性能老化方面,东汽也采用了一系列先进的保效技术,取得了卓有成效的应用效果。
1 汽轮机性能老化的主要原因
汽轮机性能老化不仅受设计和加工制造的影响,还和机组运行条件、运行方式等因素相关,主要影响因素包括汽轮机的结构设计、机组运行的汽水品质、运行方式等[12-17]。总体而言,汽轮机性能劣化主要有以下几方面的原因:
1.1 固体颗粒侵蚀
国内外研究表明,固体颗粒侵蚀(Solid Particle Erosion,SPE)一般发生在锅炉启动或长期低负荷运行情况下。特别在锅炉启动时,过热器管和再热器管道由于受热冲击,引起管道内侧氧化铁剥离从而形成固体颗粒。固体颗粒以高速度撞击靠近高压第1 级或调节级喷嘴后缘的压力(凹)面,由于隔板静叶的后缘区域相对较薄,因此可能会迅速损坏,从而导致机组效率降低[18]。
1.2 结构性变形引起的机组内漏
进汽采用插管形式将汽缸和阀门连接的机组以及一段抽汽采用插管的机组,在高温、高压的工作环境下,进汽和抽汽插管的密封可能失效,从而造成部分未经做功的蒸汽通过内、外缸之间的夹层直接漏至汽缸排汽端,引起汽缸温差异常,并导致缸效率下降;高中压汽缸工作温度高、工作压差大,随着机组长时间运行容易发生高温蠕变永久变形。高中压内缸变形是由高中压内缸内外壁温差大及相邻部位温度梯度大引起的,温差大会导致汽缸中分面内壁的径向应力、弯曲应力过大,从而导致中分面产生张口变形,造成部分蒸汽通过汽缸张口泄漏,引起机组效率降低[19]。
1.3 轴封、汽封磨损导致间隙变大
随着运行时间的增加,以及启动和停机次数的增多,汽轮机各段轴封和通流内部汽封齿等位置动静之间可能发生接触和摩擦。一方面,引起轴封间隙有所增大,从而更多的高品位的蒸汽漏至系统其他部位,导致机组热耗升高、经济性下降;另一方面,在通流内部静叶根部汽封、动叶顶部汽封间隙会有所增大,导致相应部位的蒸汽泄漏量增加,引起通流效率下降[20]。
1.4 叶片水蚀影响
汽轮机中的水蚀是由蒸汽穿过饱和线后形成的液滴。在再热蒸汽汽轮机上,水蚀通常限于较长的末级动叶的顶端部分。水蚀造成两个主要的性能损失:动叶前缘的侵蚀和静止件的侵蚀和腐蚀。末级动叶的顶端区域的水蚀是由于从静叶及隔板侧壁形成的大的、缓慢移动的液滴进入动叶时的高切向速度引起的。动叶前缘的粗糙化导致摩擦和空气动力学损失的增加。由水份引起的性能劣化的第二个来源是在由碳钢制成的静止部件上发生的腐蚀现象。这些包括后面的LP隔板侧壁和LP内缸。这种现象使表面变粗糙,增加了蒸汽流道路径部件周围的摩擦损失和泄漏。
1.5 机组通流部分结垢
汽轮机通流部分结垢与电厂机组运行的汽水品质关系很大,不良的给水化学控制是汽轮机通流部分出现沉积物的主要来源。通流部分沉积物对汽轮机性能的影响取决于它们在汽轮机内的位置、它们在喷嘴和动叶上的位置、厚度以及由此产生的表面形态。通流部分沉积物可以改变喷嘴和动叶的基本轮廓形状,导致改变汽轮机内的焓降分布,较差的通流部分气动特性以及由于较粗糙的表面状况引起的增加的摩擦损失相关联的效率损失。当沉积物发生在汽轮机高压缸部分时,会减小汽轮机的通流能力。这是由于高压缸部分蒸汽压力高,动静叶片叶高相对较短,通流面积较小,沉积物附着在叶片表面,会极大地减少喷嘴和动叶通流面积,从而对汽轮机整体通流能力造成较大影响。
1.6 汽轮机受异物击打损坏
汽轮机蒸汽通道的异物损坏是由外来物质进入汽轮机造成的。典型的异物包括焊条,焊珠,焊接飞溅物,诸如小螺母和螺栓的松散碎屑以及可能从蒸汽系统或汽轮机本体中的上游部件松动的其它材料或部件。异物造成的损坏通常在喷嘴后缘和动叶前缘处发现。异物容易通过喷嘴,但是它不能加速到足以穿过动叶通道,导致异物在喷嘴和动叶之间来回弹射。这将一直持续,直到它破裂。汽轮机受异物击打损坏主要是与机组安装和运行等水平有较大关系;相对而言,此类问题占比较低。
2 东汽保效措施
近年来,随着通流技术的发展和进步,东汽积极推进火力发电设备经济性的提升和改善工作,以创新推动技术进步,自主研发的第三代、第四代先进通流技术已经在三河、德州、邹县、景德镇以及新昌等300~1000MW机组通流改造项目上得到成功验证。同时,东汽在减小机组性能老化方面也开展了大量工作,在机组长期保效上采用了一系列先进技术,成绩优异。
2.1 防固体颗粒侵蚀(SPE)措施
国内外研究表明,固体颗粒侵蚀一般发生在锅炉启动或长期低负荷运行情况下。特别在锅炉启动时,过热器管道由于受到热冲击,引起管子汽侧氧化铁剥离从而形成固体颗粒。东汽在防止固体颗粒冲蚀方面,通过合理选择高温部件材料、优化相关部件设计、采用相应的加工工艺等有效的措施,已投运机组大修开缸检查时,基本上未发生明显的固体颗粒侵蚀现象。
为了防止固体颗粒对机组的冲蚀,在机组部件结构优化方便采取了如下措施:
2.1.1.1 高压第1级采用斜面喷嘴型线(SPE 叶型)技术,应用大节距、少叶片只数喷嘴设计,有效防止固体颗粒冲蚀(见图1、图2)。
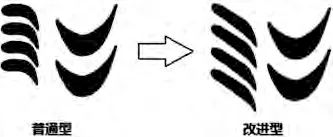
图1 普通喷嘴及斜面型线喷嘴示意图
图2 调节级动叶实物图
设计合理的动静叶轴向间隙,可使动叶反射的固体颗粒不能打在静叶背弧上,彻底切断多重反射的途径。GE、日立等公司均进行了轴向间隙与颗粒冲击力关系的试验研究。其结果表明:在常规间隙的基础上,动静叶轴向间隙增大1 mm,冲击力可降低65%;增大2 mm,冲击力可降低90%。因此,优化机组动静设计间隙,可有效防止固体颗粒侵蚀,实现再热第1级的无老化设计,提高持久效率(见图3)。
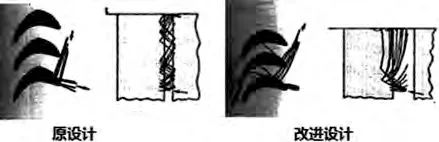
图3 改进前及改进后固体颗粒轨迹
新型永久性滤网能够有效防止大颗粒固粒进入通流部分,避免大固体颗粒对通流部分静叶和动叶的侵蚀破坏,保持通流持久高效(见图4)。
图4 新型永久性滤网
对于高压第一级和再热第一级,除过优化高温部件结构外,还合理的选取高温部件材料,并采用相应的加工工艺等有效措施来防止固体颗粒冲蚀。
采用Cr-C 保护涂层技术(见图5),有效减小高压第1级和再热第1级的固体颗粒侵蚀,提高持久效率。
图5 采用Cr-C保护涂层技术高压第一级喷嘴
高压第1级和再热第1级动静叶采用耐固体颗粒侵蚀能力强的含铌钢材料。静叶、动叶采用Cr-Mo-V-Nb-N钢。
为防止可能加剧的固体颗粒侵蚀,除汽机采取防护措施外,建议整机系统及运行也采取适当的措施:
1)建议采用两级串联旁路,机组启动前,通过旁路系统可带走固体颗粒,减少再热系统氧化物进入汽轮机通流。
2)机组安装及大修时需对锅炉蒸汽发生器、再热器及主要管道和主蒸汽管道、再热蒸汽管道进行必要的清洗去除残留物。
3)保证必要的锅炉启动时间,减少热应力冲击引起的氧化物。氧化物的产生,主要是在锅炉的启动、停炉和负荷骤变过程中,管子温度变化幅度较大,由于母材和氧化膜的热膨胀能力不同,会导致氧化膜开裂脱落,且氧化膜的厚度越厚,脱落所需应力越小。过快的启动速率,是其产生氧化物较多的一个重要原因。因此,在高再热参数的机组中,需合理设计启动时间,避免过快启动,引起氧化膜脱落。过热系统和再热系统管材内表面可采用喷丸或镀Cr处理工艺,减小汽侧氧化物的形成。
2.2 消除机组结构性内漏
在对运行的机组进行调查之后,关于用户所反映机组经济性下降的问题,东汽分析认为:长期运行后的机组结构性内漏是重要原因之一。东汽通过对机组结构性内漏的原因进行分析,确定了解决这类问题的思路和办法,并在改造和新机组中应用,从而解决机组经济性下降的问题:
现对高中压内缸两端隔热板处增加相应的汽封结构以减少蒸汽流动,这样可以达到减少高中压内缸内外壁温差的效果,如图6所示:
图6 设计间隙由5 mm优化为2 mm
高压内、外缸间定位槽增加盘根密封,阻止高压侧蒸汽通过定位槽泄漏至中压部分,见图7。
图7 高压内、外缸肩胛处密封
制造、安装精度对机组经济性的影响已经越来越受到重视。如图8 所示,在高、中压进汽管处,东汽采用叠片式密封,其主要特点在于:金属密封叠环具有接触部位少、在极小的间隙内形成多重迷宫密封;设计间隙小,密封环与进汽管间隙小;进汽管管件表层堆焊司太立合金,具有持久、耐磨特性。
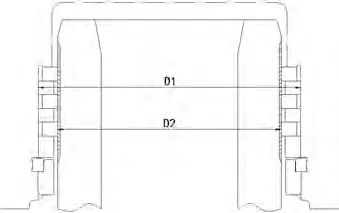
图8 进汽管密封结构
根据电厂大修反馈的情况,进汽管密封结构主要存在的问题在于:
1)密封间隙偏大主要原因在于加工制造,有效措施是加大产品质量的监控力度,密封环与进汽管是配车,在东汽总装、现场安装时对每圈均检查间隙,必须保证满足设计要求;
2)经过多台超、超超临界机组运行实践,司太立合金堆焊是成熟可靠的,但仍有必要提高司太立合金焊接的工艺和探伤检查,保证焊接的质量可靠性。
另外,针对安装精度对机组的经济性影响,除图纸要求外,设计部门已经对机组的主机证明书进行了整顿,对机组的安装提出了严格要求,以保证机组的安装满足设计的要求。
原机组高压喷嘴室采用独立装配式结构,存在进汽插管与进汽室的密封问题;低压内缸采用独立的进汽室结构,采用螺栓把合,进汽结构设计、制造、安装不好极易产生漏汽,从而影响机组保效。
改造机组的高压内缸经过优化,喷嘴室与内缸铸为一体,进汽插管一端用螺栓把接在高压内缸上,另一端与外缸采用密封圈密封,减少一个漏点,有利于提高高压缸效率。进汽插管与外缸的密封经过优化,采用多金属密封圈组成,利用不同金属的冷热态线胀系数差保证密封效果,允许管道与汽缸之间的存在相对位移同时,保证漏汽量为零。同时,改造机组的低压内缸经过优化,新方案取消了原来单独的低压进汽室,将进汽部分结构整体焊接到低压缸上,这样就避免了原来因装配而带来的蒸汽泄漏的问题。
原机组高压进汽处为独立喷嘴室,中压侧设有BDV接口及中压一级叶轮冷却接口。如图9所示:
图9 纵剖面图
优化后设计为整体式内缸,取消独立喷嘴室,减少漏点;优化进汽型线,减少效率损失;同时该结构整体应交较小,减小机组长期运行后的汽缸变形。中压侧取消BDV 接口及叶轮冷却接口,减少漏汽及蒸汽耗损,提升机组经济性。优化后内缸如图10 所示:
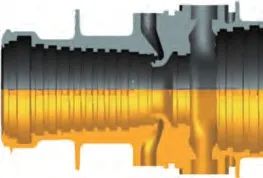
图10 优化后高中压内缸示意图
通过对改造部件进行结构优化,对重要部件进行有限元分析,增加其强度与刚度,降低机组运行时部件的应力水平。机组长期运行后,汽缸不易变形,各密封面处不张口,减少内漏。图11 为汽缸在稳态运行时的Mises应力分布云图。
图11 应力云图
高压内缸在稳态运行时,汽缸整体的应力水平较低,中分面汽密性也满足要求。图12 为中分面接触压力分布云图。
图12 中分面接触压力分布图
低压缸结构重新设计,新方案取消了原来单独的低压进汽室,将进汽部分结构整体焊接到低压缸上,这样就避免了原来因装配而带来的蒸汽泄漏的问题。如图13所示,新方案取消了中分面整体法兰结构,而将中分面法兰分散,使中分面螺栓只提供密封功能,不受轴向力;中分面法兰分散还可避免原来因法兰为整板而产生的热应力及变形的情况,因此新方案降低了因中分面变形而产生蒸汽泄漏的概率。新方案低压内缸采用斜置式支撑结构,并采用加强筋增加轴向刚度。新方案的结构具有一定的自密封性,在蒸汽压力下,其受力特点可使中分面被压的更紧,辅助中分面密封。
图13 低压缸结构优化设计
2.3 优化汽封配置
对已投运机组来说,漏气损失是影响机组效率的主要因素。从保证机组经济性而言,要求汽封漏汽量越少越好,也即汽封间隙越小越好;从保证机组运行安全而言,要求在各种状态下,汽封不和转子发生摩擦,或发生摩擦但对转子磨损小。因此,对汽封要求是:泄漏量小,而且对转子产生的附加作用力和损伤也要小。
从汽轮机的实际运行情况分析,影响汽轮机组效率的主要原因(只考虑汽轮机本体)有两个方面:一是由于受机组当时设计制造水平的限制;二是汽轮机在安装、检修过程中,为保证机组的安全运行,采用传统疏齿式汽封,并且人为地放大汽封间隙,增加了漏汽损失。错齿汽封是近年来东汽大量采用的一种新型汽封形式,目前该种汽封已广泛应用于机组轴封,以及反动式机组叶顶汽封位置,错齿汽封主要结构如图14 所示,采用填丝材料将汽封片镶嵌于转子及汽封圈上,相比传统汽封形式,错齿汽封主要具有以下优点:
图14 汽封优化设计
1)取消转子城墙齿,在相同长度范围内,能够设置更多的有效齿,增加密封性,减少轴封漏汽,提高机组经济性。
2)汽流经过错齿汽封齿,将会产生漩涡,使蒸汽能量耗散,增加密封性,减少轴封漏汽,提高机组经济性。
东汽在自建汽封试验台上能进行各种典型密封结构的全尺寸试验,运用高精度的测试系统得到准确可靠的试验结果,真实、精确的反映了汽封的密封性能。东汽具有多种汽封的使用经验,可根据用户需求采用不同类型的汽封,在特殊部位采用特殊汽封,如刷式汽封、封严汽封、蜂窝汽封、布莱登汽封等(见图15)。
图15 东汽常用的汽封结构
2.4 低压叶片防水蚀措施
为确保机组安全运行,东汽在设计时采取了完善的防水蚀及抗应力腐蚀措施来确保机组长期安全、经济地运行。采用的主要措施有:
2.4.1 被动措施
大水滴撞击动叶过程中,被动采用各种表面抗蚀技术,来提高金属的抗侵蚀性能。主要手段为对叶片易受水滴撞击的部位进行处理,包括对动叶叶顶部进行淬硬处理(如火焰淬硬、电火花强化、喷丸、等离子喷涂、表面氮化等,见图16),动叶顶部堆焊司太立合金选用高合金叶片钢等。
图16 自动化高频淬火设备
2)通过静动间轴向间隙的设计,使水滴碎化,降低水滴半径,减小对动叶进口的冲击;
3)末级动叶叶身进行喷丸表面处理,提高其抗水蚀特性;
4)末级动叶对靠近动叶顶部进口区域进行高频淬火工艺处理,大幅提高其抗水蚀特性。
根据水相演变过程中的形态及运动特性,主动采取各种除湿技术。除湿装置和措施主要有:中间再热、水分离/加热器、隔板外环开设疏水孔/槽、加大静叶栅与动叶栅的轴向距离、空心导叶除湿等(见图17)。
图17 低压次末级隔板去湿结构示意图
该方法主要利用水滴的径向运动特性使水滴进入疏水孔、汇集到低压缸下部疏水管后排出。
由于末级蒸汽湿度大,末级隔板出汽边外沿装有去湿环(见图18),汽流中的小水滴在离心力的作用下落入去湿环中,绕过末级动叶,直接进入排汽口,去湿环可以有效地减轻末级动叶的水蚀现象。
图18 末级动叶优化设计
通过以上措施,可使得末几级动叶水蚀处于较低水平,不会对叶片安全可靠性造成影响。该系列技术成熟可靠,已在东汽机组中大范围运用。
3 典型机组保效效果
近年来,东汽加强对汽轮机性能老化的研究并应用工程实践,委托国内权威机构进行缸效率和热耗测试。从已掌握的亚临界和超临界汽轮机试验数据来看,保效性能优良。
3.1 北方临河热电厂亚临界300 MW机组
表1 北方临河热电厂亚临界300MW机组试验数据
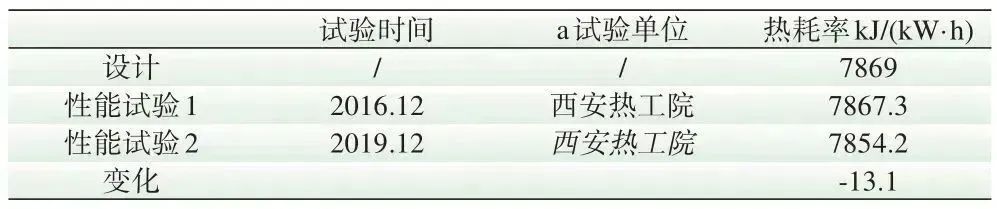
在没有老化修正的情况下,北方临河电厂机组运行3年后,热耗率没有升高,保效性能优异。
3.2 德州老化试验
针对亚临界700 MW 机组,从老化试验情况来看,德州改造机组运行10个月后老化系数仅为0.18%左右,低于ASME规程的0.31%,保效性能良好。
3.3 景德镇、邹县老化试验
针对超超临界机组,从老化试验情况来看,景德镇改造机组运行18 个月后老化系数仅为0.327%左右,低于ASME 规程的0.567%;而邹县改造机组运行23 个月后老化系数仅为0.464%左右,低于ASME 规程的0.615%,保效性能良好(见图19)。
图19 部分机组老化系数
4 结语
火电行业整体发电小时数和平均负荷率的下滑促使汽轮机提效和保效技术研究不断深入。东汽立足自主研发与国际合作相结合的技术路线,建立以“理论优化→厂内试验验证→改造机组工业验证→新机组应用”为特点的研制体系。实践显示,东汽第三代和第四代通过应用以上种种新技术,可以保证各项经济指标在安装调试完成后能达到机组设计值,使新建机组能长期安全连续高效运行;对于现役机组,采用新结构、新技术进行通流改造可以大幅降低老机组热耗,也是减小性能老化速率的最有效手段。
参考文献:
[1]顾煜炯,徐婧,李倩倩,等.燃煤发电机组深度调峰能力模糊综合评估方法[J].热力发电,2017,46(2):15-21.
[2]杨志平,李柯润,王宁玲,等.大数据背景下燃煤发电机组调峰经济性分析[J].中国电机工程学报,2019,39(16):4808-4818.
[3]刘入维,肖平,钟犁,等.700℃超超临界燃煤发电技术研究现状[J].热力发电,2017,46(9):1-7.
[4]刘志强,赵毅,潘荔.中外火电节能减排效率分析与比较[J].热力发电,2021,50(3):9-18.
[5]王宁玲,张勇,杨勇平,等.600MW 火电机组节能降耗分析与优化措施[J].中国电力,2009,42(9):55-57.
[6] 解春林.火力发电机组深度调峰下汽轮机系统特性研究[D].北京:华北电力大学,2013.
[7]付昶,王伟锋,朱立彤.汽轮机通流能力分析及试验研究[J].热力发电,2013,42(1):48-51.
[8]吴瑞康,华敏,秦攀,等.燃煤机组深度调峰对汽轮机设备的影响[J].热力发电,2018,47(5):89-94.
[9]张国柱,张钧泰,李亚维,等.燃煤发电机组深度调峰运行的能耗特性分析[J].电力建设,2017,38(10):56-61.
[10]侯玉婷,李晓博,刘畅,等.火电机组灵活性改造形势及技术应用[J].热力发电,2018,47(5):8-12.
[11]张晓鲁,张勇,李振中.高效宽负荷率超超临界机组关键技术研发与工程方案[J].动力工程学报,2017,37(3):173-178.
[12]朱中杰,闫森,周惠莲.超临界600MW等级汽轮机整体通流改造结构特点[J].热力透平,2015,44(2):83-85.
[13]马超.进口亚临界600 MW 汽轮机通流部分改造及效果分析[J].能源工程,2016,36(2):80-83.
[14] 张昊,雷少博,付康民,等.1000MW超超临界汽轮机通流部分改造效果分析及研究[J].轮机技术,2021,63(4):315-317.
[15]张继红,杜文斌,赵杰,等.600MW等级超临界汽轮机通流改造综述[J].热力发电,2019,48(2):1-8.
[16]章良利,李敏,周晓蒙,等.深度调峰下燃煤机组运行方式对能耗的影响[J].中国电力,2017,50(7):85-89.
[17]周丽丽.超超临界机组宽负荷运行建模仿真与系统优化[D].南京:东南大学,2021.
[18]史进渊.基于设计寿命的汽轮机检修周期优化方法的研究[J].动力工程学报,2020,40(7):530-539.
[19] 赵世全,魏松涛.汽轮机持久效率分析[J].东方汽轮机,1999,(2):25-46.
[20]李国明,谢澄,郑磊,等.大型汽轮机通流改造中常见问题探讨[J].汽轮机技术,2019,61(6):473-478.
注:原文发表于《江西电力》2023年第2期
文章来源: 集控运行专业技术交流平台