近年来随着国内外汽车行业发展的日趋成熟,自动化生产成为模具冲压过程的首选。自动化生产对修边冲孔类模具的要求:①所有冲裁废料必须滑出冲压机床台面并滑到废料收集系统内,这就要求模具冲裁的废料滑出要顺畅可靠,一旦废料堆积必须停止生产,如果没有及时发现废料堆积可能会损坏模具;②无铁屑产生,否则造成外板质量缺陷必须停止生产,进行修模及模具的清洁,降低了生产效率。现介绍一种自动化生产的汽车发动机盖外板修边工序的工艺及废料滑落模拟的应用。
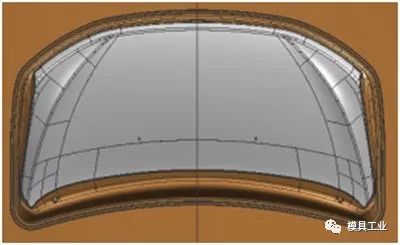
(a)工序①
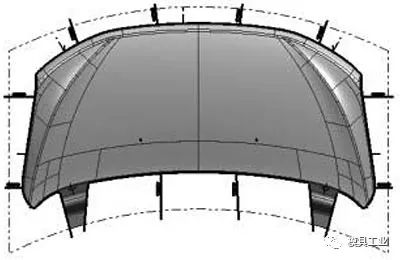
(b)工序②
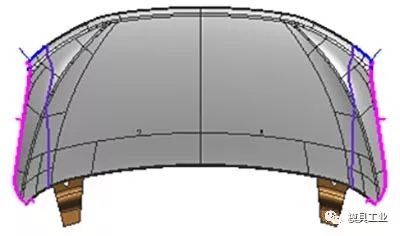
(c)工序③
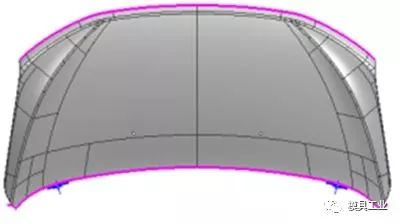
(d)工序④
图1 原工艺方案
图1所示为某轿车发动机盖外板,材料DC53D+ZF45/45-FD,料厚0.7mm,外形尺寸1630mm×820mm×80mm,属于大型车身外覆盖件,自动化生产,废料对角线长度要求小于450mm。冲压工序依次为:①拉深;②修边、侧修边、冲孔;③侧翻边;④切角、翻边、侧翻边。
原工艺修边方案见图1(b),采用全周修边,送料方向前后侧共6把废料刀,原工艺修边方案虽然具有修边模具结构简单、外形尺寸小等优点,但送料方向前后侧废料刀周围会出现掉铁屑的情况,影响成形零件的质量和模具外观的清洁度,同时降低了生产效率,并且废料切刀处废料为撕裂状态易产生毛刺,操作时存在刮伤板件外表面的隐患。为改变原工艺方案存在的不足,决定采用废料二次切断的新工艺,如图2所示。
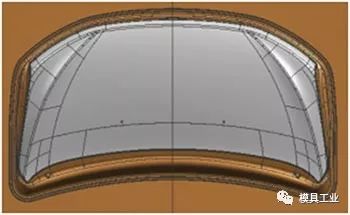
(a)工序①
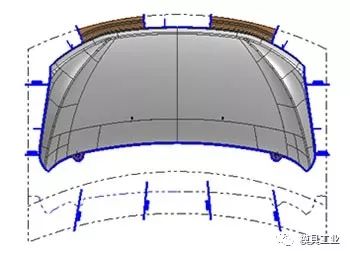
(b)工序②
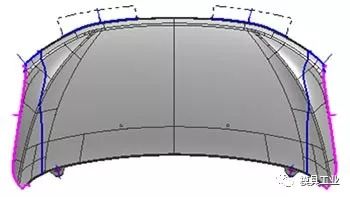
(c)工序③
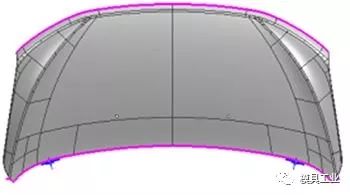
(d)工序④
图2 新工艺方案
图2所示新工艺采用二次切断的修边方式,取消了送料方向前后侧的废料刀,有效控制了铁屑的产生,且在冲裁间隙合理的情况下不会产生毛刺,降低制件外表面被划伤的概率。优化后冲压工序为:①拉深;②修边、侧修边、冲孔;③侧修边、侧翻边;④切角、翻边、侧翻边。
图2(b)所示为某汽车发动机盖外板的第二工序简图,针对第二工序模具要实现的功能进行分析。
(1)发动机盖外板修边,且同时满足二次切断的功能。
(3)发动机盖外板与挡风玻璃搭接方向冲两处三角形工艺孔,为后工序定位所用。
通过与客户进行技术交流,客户要求第二工序废料滑出机床外,因此根据工艺要求并结合客户需求进行了如下模具结构设计。
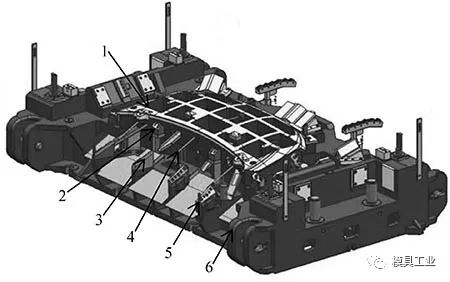
图3 下模结构
1.凸模 2.定位块 3.二次切断刀 4.废料导滑杆 5.废料挡板 6.下模座
从第二工序模具下模结构(见图3)可看出,模具前侧设计了废料导滑杆及二次切断刀,只有将一次切断废料顺利导滑到二次切断刀上,且二次切断刀长度足够时才能保证废料二次切断的顺利完成。废料能否顺利滑落通过人工检查存在一定的风险。现采用Adams软件进行模拟,通过以下4个步骤对模型进行废料滑落干涉检查、原因分析和模具修改。
将UG设计的实体及材料转换为“.x_t”文件格式,通过Adams软件读取数据,如图4、图5所示,设定模具及材料如图6所示。
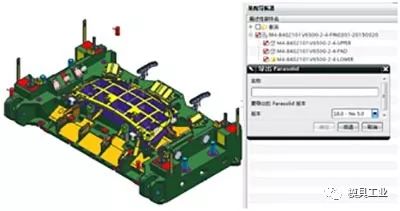
图4 UG实体数据转换
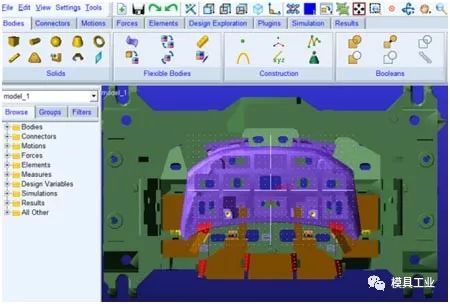
图5 Adams软件读取数据
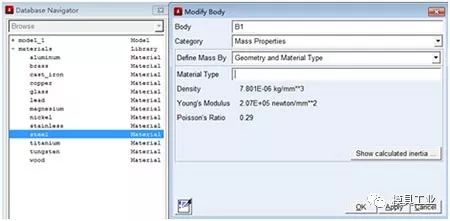
图6 设定材料
首先下模与板料都导入Adams后,在Settings中Gravity设置重力方向(选Z轴的负向)。其次将下模座、废料滑板等在仿真中不动的部分设置为固定副,如图7所示。最后设置接触关系,包括板料及可能与板料发生碰撞的物体,如废料切刀、废料滑板等,相关接触设置如图8所示。

图7 设置为固定副

图8 接触设置
先用Adams软件对废料的滑落运动进行模拟分析,输出模拟结果,根据Adams软件的错误提示(如图9所示,错误提示共2项问题),对数模进行排查后是因设计状态废料与废料切刀存在干涉,对废料切刀结构进行优化后重新做模拟分析。重新分析时,废料未能顺利滑到二次切刀上,卡在了二次切刀的侧面,如图10所示。

图9 错误提示
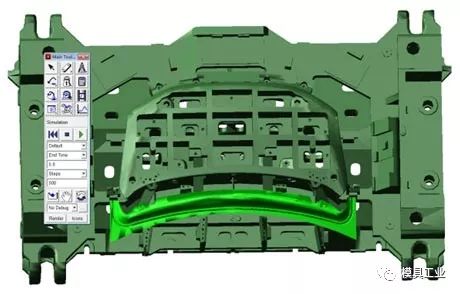
图10 废料未能顺利滑落
找出原因制定对策
废料未能顺利滑到二次切刀上的原因:①废料导滑杆角度过小;②废料导滑杆相对二次切刀Z向高度过低。解决方案:①将废料导滑杆角度加大到25°;②调整废料导滑杆Z向高度高于二次切刀10mm。模型修改后,废料顺利滑到二次切刀上,如图11所示。
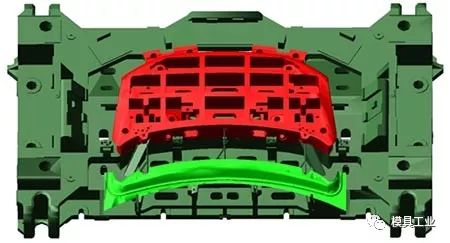
图11废料顺利滑落
对于废料不能自由滑落的情况,生产现场通过增加顶料气缸、挂钩、导杆等辅助手段使废料能够自由滑落,为了验证这些辅助方式的有效性和可行性,均可以运用Adams软件进行模拟验证。
经生产现场调试验证,一次合模切断的整块废料稳定地滑到二次废料切刀上,二次合模时完成切断,切断后的废料滑落顺畅,验证了该工艺方案的可行性,有效避免了制造过程的模具返工及不必要的成本浪费。
通过Admas软件的废料滑落模拟功能,将废料不能自由滑落的问题在零件设计、冲压工艺、模具设计等前期阶段通过既定的数据建立相关模型,再利用Admas软件进行运动仿真模拟,提前预测可能存在的废料滑落不畅问题,针对存在的问题提出解决方案。避免将问题遗留在模具制造阶段,既缩短了模具制造周期又降低了模具的返修、报废的风险,减少人为因素对模具制造周期的影响。