本文图形摘要
►
采用三维计算流体动力学(CFD)模型对MBR(膜生物反应器)的结构设计进行了研究。
►
悬浮固体混合液浓度
(MLSS)
的增加提高了剪切应力的均匀性
。
►
将气泡直径优化至
5mm
有助于改善剪切应力的分布
。
►
通过延长侧挡板的长度,改善了膜表面上的剪切应力均匀性
。
►新颖的原位曝气方法提高了膜的抗污性能。
本研究利用三维计算流体力学(CFD)模型模拟了平板膜生物反应器(MBR)的流体动力学特性,以解决膜污染问题并优化结构设计。通过调查改变剪切应力和液体速度的关键参数,对膜模块配置和操作条件进行了优化。发现混合液悬浮固体(MLSS)浓度增加会增加剪切应力,从而实现剪切应力的更均匀分布。通过将气泡直径优化为5mm,膜表面的剪切应力得到了优化,并且分布相对均匀。此外,延长侧边挡板长度显著改善了每个膜上剪切应力分布的均匀性。同时,还发现了一种新型的原位曝气方法,与传统曝气方式相比,可以将湍流动能增加200倍,从而实现了更均匀的气泡流线。因此,这种新型的原位曝气方法在MBR中展示出优越的膜抗污染潜力。本研究为MBR的结构设计和优化提供了一种新方法。CFD模型、优化技术和新型的原位曝气方法的创新组合对提升污水处理中膜分离技术性能具有重要意义。
膜生物反应器(
MBR
)技术,即生物反应器与膜分离相结合的技术,由于其占地面积小、自动化程度高、处理高效等优点,已成为当前市政污水处理和水再利用最具发展前景的技术之一。在
MBR
中,流体力学参数是直接影响停留时间、生物反应过程、污染物去除、膜污染和能耗的关键因素。因此,流体力学的研究已成为
MBR
领域的热门课题之一。深入了解
MBR
的流体力学性能对于提高
MBR
技术的运行效率和经济效益至关重要。
由于计算流体动力学(
CFD
)能够清楚地展示每个区域的液体流动和每个膜表面的剪切应力分布,因此
CFD
已被广泛应用于研究
MBR
的水力性能。与全尺寸实验相比,
CFD
虚拟实验具有较高的成本效益和可靠性。
CFD
广泛应用于
MBR
的结构优化,包括膜组件配置的优化和各种流体力学参数的影响研究。在这些参数中,曝气操作由于对
MBR
的运行性能和抗污能力的影响而受到更多关注
。本课题组提出一种新颖的原位曝气技术用于膜分离过程,使膜表现出兼具高截留率和高渗透性的特点。具体过程是制备了聚偏二氟乙烯(
PVDF
)
-Ni
导电膜,通过外加电场发生析氢反应实现原位曝气操作。由于原位曝气的作用,过滤系统表现出完全的刚果红染料截留率(
100%
)和非常高的渗透性(
137.5
±
6.8 Lm-2h-1bar-1
),在很大程度上打破了渗透性和选择性之间的“
Trade-off
”效应。课题组后续的研究发现原位曝气在渗透性和抗污方面有明显促进作用。尽管这些研究确认了原位曝气的优越性和潜在应用
,但在
MBR
与新颖原位曝气模式相结合的
CFD
模拟研究仍然缺乏。因此,有必要开展进一步的研究,以提升和优化原位曝气这一新型曝气模式的性能和应用领域。
在本研究中,我们开发了一个三维CFD模型,研究了MBR中的剪切应力和液体流速,并分析了各种操作参数对MBR流体力学的影响。通过优化膜组件配置改善了MBR的流体力学特性,并率先利用CFD模拟评估了原位曝气。本研究对于了解MBR流体力学有重要贡献,并为MBR的结构设计和优化提供了有价值的参考。
本研究设计了一个如图1所示实验室规模的MBR(长×宽×高=855 mm×340 mm×600 mm)。计算区域的尺寸基于实验室规模的平板(FS)MBR的实际尺寸(长×宽×高=
360
mm×320 mm×510 mm)。十个膜模块(长×宽×高=320 mm×220 mm×6 mm)安装在反应器中,每个膜模块上安装有两个膜。所有的膜模块平行排列,相邻模块之间距离为6 mm。为减少污泥流入,五根曝气管(长×直径=240 mm×12 mm)位于膜下方40 mm处,每根曝气管的两侧倾斜45度,分布着十一个曝气孔(直径2 mm)。实验采用孔径为0.1微米的平板超滤膜。为了节省计算量,CFD模型采用了一个对称面,如图1a所示。研究了9个关键参数,以确定MBR的最佳结构设计。在原位曝气过程中,当施加一定电压时,导电膜表面会通过析氢反应释放微气泡。
在数值模拟中,通过使用更细的网格可以提高计算精度。然而,这种改进是以增加计算时间为代价的。此外,增加网格密度带来的精度提高会出现递减的收益。为了确保本研究的最佳精度,我们在曝气管和膜之间的区域采用了平均尺寸为2 mm的六面体网格。由于该区域内的流动动力学非常复杂,所以这种更细的网格是必要的。另一方面,对于其他区域,5 mm的网格尺寸已经足够。为了连接不同的网格尺寸,我们采用了四面体网格。用于此次研究的网格总单元数量约为1.0×106。值得注意的是,在获得准确可靠的结果的同时,尽量减少计算成本,选择适当的网格尺寸至关重要。因此,本研究采用多种网格尺寸,以流动动力学的复杂性为指导,确保了准确性和计算效率之间的最佳平衡。
图
1. (a-c) MBR
的示意图及其配置参数
; (d-e)
网格细节
在MBR中,液体和固体颗粒的运动状态可以视为等效,从而将三相流简化为涉及气体和液体的二相气液流动。为了模拟这种流动,采用了欧拉模型,因为它能够更高效地模拟气液流动,并且适用于我们特定的研究问题,同时采用了k-ɛ湍流模型来模拟湍流流动。在本研究中,活性污泥被视为连续的液相,气泡大小被视为固定。由于膜的过滤通量明显低于曝气期间的流速,膜表面被视为不可渗透的静止壁面。在原位膜曝气的模拟过程中,膜表面被设置为气体进口,连续气泡被引入其中,这在先前的报告中已被证明是可行的。曝气孔口用作气体进口,液体表面则充当气体出口。在所有稳态案例中,分析对象被选为经过10,000次迭代后的稳定流场。本研究中的所有建模、网格划分和仿真计算均使用商业软件ANSYS FLUENT 19.1进行。
如图2a所示,曝气管直径(Da)从7毫米增加到13毫米,导致膜表面的剪切应力从0.5219帕增加到0.5956帕,并随着Da的进一步增加而降低到0.5417帕。膜对称面上的液体速度轮廓如图2a-c所示,显示在曝气管附近,液体速度约为0.5 m/s。随着液体向上游流向膜模块,模块之间较窄的距离导致较高的液体速度,最高可达约0.8 m/s。当液体接近液体表面时,它流向两侧,当它到达反应器壁时,它向下流动至底部。当Da大于13厘米时,如图2d所示,液面以下逐渐形成一个涡旋。流体环流区域的大小通常由膜与液体水平面之间的距离决定。如果距离过低,会导致缺乏流动区域,使液体难以循环;而如果距离过高,环流距离将增加,导致循环过程中能量消耗增加。因此,膜的最大剪切应力发生在13厘米的Da处,并且该值用于后续计算。
图2. (a) 膜与液体表面距离对剪切应力的影响; 对称面上的液体速度轮廓 (b, Da = 7 cm; c, Da = 13 cm; d, Da= 19 cm)
图3显示了膜间距对剪切应力的影响。随着膜间距从6毫米减小到4.5毫米,剪切应力从0.5956帕增加到0.6549帕(图3a)。这个结果可以归因于膜模块与中心位置更接近,增强了边缘膜的曝气效果(图3b-c)。在膜间距为6毫米时,对称平面上的液体速度轮廓如图3b所示,显示接近两个边缘膜的液体速度明显低于中间部分。这是因为在曝气管上升流动过程中,液体具有双曲线形状的速度剖面,这已有先前的报道。双曲线形状的流动有效地清洗了中间的膜模块,但对边缘膜没有相同的效果。进一步减小膜间距到3毫米,会导致膜表面的剪切应力从0.6549帕减小到0.5970帕(图3a)。这可能是因为当膜间距太窄时,较大的气泡难以通过,这可能有助于减少剪切应力和膜污染。当Db为4.5毫米时,所有的膜模块都能得到曝气,并且模块之间的液体流速相对较高(图3c)。因此,在本研究条件下,Db = 4.5毫米被认为是最适合的尺寸。
图3. (a) 膜间距对剪切应力的影响;对称面上的液体速度轮廓 (b. Db = 6 mm; c. Db = 4.5 mm; d. Db = 3 mm)
图4a描述了挡板与槽壁之间距离对剪切应力的影响。随着Dc的增加,膜表面上的平均剪切应力变化不到1%。这是因为挡板与槽壁之间的宽阔空间比膜组件之间的狭窄间隙对水流的阻力小。当Dc设定为9厘米时,液体表面下的两个涡旋的大小显著减小(图4b),而涡旋中的液体速度增加。这表明当Dc过小时,膜模块外的液体可能缺乏环流空间。当Dc增加到15厘米时,从膜模块到反应器底部的液体环流距离增加(图4d),导致液体流动过程中的能量消耗增加。相反,当Dc设定为12厘米时,剪切应力最大,而膜之间的液体速度相对均匀(图4c)。因此,在本研究条件下,Dc = 12厘米是最佳距离。
图4. (a) 挡板与槽壁距离对剪切应力的影响;对称面上的液体速度轮廓 (b. Dc = 9 cm; c. Dc = 12 cm; d. Dc = 15 cm)
膜与曝气管之间的距离(Dd)是膜生物反应器(MBR)的重要设计参数。图5a显示,将Dd减小到5.9厘米以下会逐渐降低膜表面的剪切应力。这是因为Dd调节了外部流体进入膜模块的区域。较小的Dd增加了液体的流入阻力,减少了循环流速,并导致上游液体被两侧流动液体更加明显地挤压。这导致膜模块中的曝气效果更加不均匀(图5b)。此外,液体在从曝气装置向上流动时呈双曲线形状的速度分布,可能是由于从曝气管道向上流动的液体被膜组装两侧的液体挤压所致(图5b)。能耗可以根据曝气速率和曝气系统的功耗计算得出。由于实现所需的流体力学条件需要增加曝气速率,因此应将Dd的大小最小化以避免增加能耗(图5d)。在考虑了流入阻力、远距离传输能耗和剪切应力的情况下,确定了最佳的Dd值为5.9 cm。
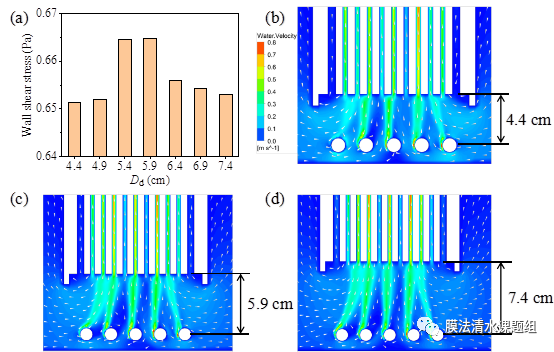
图5. (a) 膜与曝气管中心之间距离对剪切应力的影响; 对称面上的液体速度分布(b. Dd = 4.4 cm; c. Dd = 5.9 cm; d. Dd = 7.4 cm)
3.1.5. 曝气管中心与槽底之间的距离
(De)
根据图6a所示的结果,可以看出当曝气管中心与槽底之间的距离为1.6 cm时,剪切应力最大。值得注意的是,当距离增加或减小时,剪切应力显著减小。将De减小至0.6 cm会使得从曝气装置向上游动的液体流向中心弯曲,这可能是由于曝气管下方的空间减少所致。这反过来增加了液体流入膜模块两侧的速度,导致更加明显的双曲线形状(图6b)。当De增加到3.6 cm时,膜模块中喷射出的液体速度显著减小(图6d),表明曝气管中心与槽底之间过大的距离也会增加液体的循环阻力。
图6. (a) 曝气管中心与槽底之间距离对剪切应力的影响;对称面上的液体速度分布(b. De = 0.6 cm; c. De= 2.1 cm; d. De = 3.6 cm)
图7说明了混合液悬浮固体浓度与剪切应力的关系。需要注意的是,图7中的数值始终位于给定的颜色标尺范围内。观察到在相同曝气条件下,随着混合液悬浮固体浓度的增加,剪切应力也增加(图7a)。这个现象可以归因于浓缩污泥的高粘度,增加了污泥与膜表面之间的摩擦,从而增加了剪切应力。当混合液悬浮固体浓度为5 g/L时,应变率为0.1338 Pa·L·g-1。随着混合液悬浮固体浓度的增加,应变率迅速下降,然后稳定在约0.065 Pa·L·g-1(图7b)。随着混合液悬浮固体浓度超过10 g/L,剪切应力的增加更加明显,导致剪切应力更加均匀分布(图7c)。然而,从实际角度来看,高混合液悬浮固体浓度会增加流动阻力,阻碍污泥的循环。此外,悬浮颗粒丰富的浓缩污泥还会增加膜过滤的阻力。因此,在高混合液悬浮固体浓度下,需要增强曝气强度以促进液体流动。
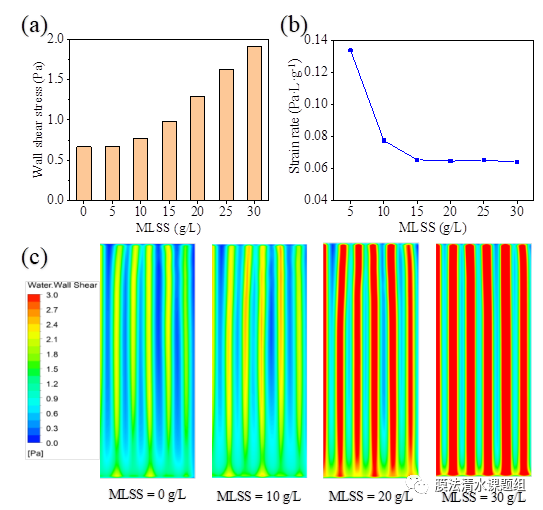
图7. (a) 混合液悬浮固体浓度对剪切应力的影响;(b) 应变率;©对称面上从左到右第四个膜的右侧表面的壁剪切应力分布
图8展示了曝气强度对流体力学的影响。结果表明,增加曝气强度对流动方向几乎没有影响,但显著增加了剪切应力(图8a)和流速(图8c)。此外,曝气强度还影响每个膜模块上的平均剪切应力,如图8b所示。当曝气速率为1 m/s时,所有膜表面的剪切应力保持在大约0.3 Pa左右。然而,这种均匀曝气效果会导致不利的膜污染控制。相反,当曝气速率大于3 m/s时,剪切应力与曝气速率呈线性增加。值得注意的是,边缘区域由于剪切应力较低,可能会遭受较高的膜污染率(图8b)。。
图8. (a) 曝气强度对剪切应力的影响;(b) 不同曝气强度下每个膜模块的平均剪切应力;© 对称面上的液体速度轮廓
在平板膜模块中,液体流动可以分为气泡流动和柱状流动两种形式。通常情况下,较大气泡产生的柱状流动会导致较大的剪切应力。然而,图9a说明1 mm的气泡可以产生更大的剪切应力,可能是因为它能够产生柱状流动和更大的湍流。当气泡直径为1毫米且整体液体速度相对较大时,虽然膜表面的剪切应力增加(图9b),但膜表面边缘的液体速度不够高,可能会加速边缘处的膜污染。此外,液位下方的两个涡旋被两个液体强烈运动的区域所取代(图9b)。当气泡直径增加到7毫米时,膜表面的剪切应力显著降低。这可能是由于膜之间的空隙较窄,无法容纳大直径气泡的通过,导致这些气泡的液体速度降低,进而使液体速度大幅下降(图9a和9e)。因此,增加膜之间的距离以确保大直径气泡的顺利通过是非常重要的。在本研究条件下,最佳的气泡直径为5 mm,可以在保持相对均匀分布的同时,提供足够的膜表面剪切应力。这凸显了在膜模块设计中考虑气泡直径和液体速度以减少污染和提高效率的重要性。
图9. (a) 气泡直径对剪切应力的影响;对称面上的液体速度轮廓图 (b. Df = 1 mm; c. Df = 3 mm; d. Df = 5 mm; e. Df = 7 mm)。
尽管有许多研究报告表明,在膜周围安装挡板可以增加膜表面的剪切应力,但挡板长度对流体力学的影响尚未知晓。为了填补这一知识空白,我们在不改变反应器的原始设计的情况下,延伸了反应器两侧的挡板,并增加了曝气管与槽底之间的距离,以研究剪切应力的分布(如图10a所示)。图10b的结果显示,逐渐延长挡板的长度使膜表面上的流速分布更加均匀。一旦挡板长度达到7 cm,挡板底部降低到低于曝气管的位置。在这种情况下,边缘处的膜可以与中间位置的膜一样受到相同的水流冲刷。因此,与原始设计相比,每个膜上的剪切应力的均匀性得到了显着改善(如图10c所示)。
图10. (a) MBR的改善效果;(b) 曝气强度为7 m/s时曝气管上方液体速度的等值线分布;© 曝气强度为7 m/s时10个膜表面的平均剪切应力。
原位曝气膜表面在膜生物反应器领域引起了广泛的关注。原位曝气可以在每个膜表面均匀生成气泡,比传统曝气方法更有效地冲洗膜表面。为了进一步研究其对膜生物反应器水动力学的影响,我们分析了不同曝气模式下的流速分布和湍流动能。研究结果显示,原位曝气显著增加了膜表面边缘附近的液体速度,并在膜之间产生了均匀的速度分布(图11b)。根据以前的报道,原位曝气的气泡直径可达到纳米级别。由于具有极大的表面积,原位曝气的气泡对膜表面提供了高效的剪切应力。通过结合外部曝气和原位曝气,可以优化膜表面上的剪切应力,并实现相对均匀的分布。此外,它还导致了更加均匀和更高的液体流速(图11c),并使湍流动能增加了多达200倍(图8d)。
图11. 对称面上的速度分布和湍流动能(a和d. 无原位曝气; b和e. 对所有膜应用原位曝气; c和f.对一半膜应用原位曝气);相同膜表面上的剪切应力等值线(g. 无原位曝气; h. 对一半膜应用原位曝气);气体速度流线(i. 无原位曝气; j. 使用原位曝气)
为了比较没有原位曝气时膜表面的剪切应力,原位曝气过程中,膜表面成为气体的进口,使得在CFD模型中很难被水流冲刷。在这种情况下,原位曝气可以将膜表面的剪切应力提高3倍以上,显著提高了膜表面的污染物去除效果,如图11g和11h所示。气体速度流线也显示出明显的差异,传统曝气方法产生的流线更靠近中心,几乎没有通过膜表面的边缘(图11i)。引入原位曝气后,所有膜表面呈现出均匀的气泡流线,降低了局部膜污染的可能性(图11j)。这些结果得到了现有文献的支持,验证了原位曝气的优越性。
关于各个相态的影响考虑方面,我们探讨了浓度对剪切应力的影响,该剪切应力影响液相和固相的分布。此外,我们还发现了一种新颖的原位曝气方法,与传统曝气方式相比,可将湍流动能增加200倍,从而实现更均匀的气泡流线,并在膜生物反应器中具有优越的防污潜力。总体而言,本研究提出的CFD模型、优化技术和新颖的原位曝气方法为膜生物反应器的结构设计和优化提供了综合方法,充分考虑了液相和固相,以减轻膜污染现象。
来源:膜法清水课题组 林红军教授、申利国教授和叶群峰副教授为主要作者。